Experience Sharing
2014 Quarter 2 Issue 19
Application of Shini Central Material Handling System
A company specializes in lighting industry, mainly producing products, like connection terminal, connector, cooling fin, cooling clip, wiring harness and lighting switch lamp holder. It’s also a enterprise developing and producing fine blanking and plastic mold. It is located in an industrial development zone in Leqing city in Zhejiang province which is of developed industry and convenient transportation. Now the company needs a set of complete auxiliary system to meet production after it realizes complete modern operation and expands production scale which is the consequence of quick development and production demands of the company.
Shini designed a final solution according to the client requirements and send an engineer to examine on the spot, to measure to confirm some related data, and to learn customer requirements. Then work out a 1:1 3D construction drawing according to the situation on the ground, the data and the customer requirements. The whole set of project is installed completely according to the construction drawing and under strict supervision by a supervisor appointed by the customer. It’s of overall planning and scientific selection from planning to construction. Besides, the system configuration is considered from multiple perspectives; the construction is of rigorous science. It not only saves cost and time for equipment to be put into production for customers, but also improves efficiency of construction, saves construction cost and establishes a good image for Shini.
The system planning involves 20 sets of injection molding machine. The raw material is PBT and PA with glass fiber. The conveying distance is 30 meters long and 16 meters wide. Quite many auxiliary equipments are applied in the system. First of all, the conveying parts requires 8 sets of hopper dryer and a honeycomb dehumidifier SD-700H to work together to dehumidify and dry material. Besides, it can accurately control temperature to meet customer requirements toward drying with micro computer control. The material are conveyed to the dryer from the 8 hoppers first and then be sent to the injection molding machine by the distributor after a series of drying. Each injection molding machine has a material pipe. It can well realize switch of material for machines.
Furthermore, it is equipped with a central vacuum generator which possesses a new type of Shini central filter. It can effectively protect the blower. Secondly, we equip a hopper receiver for the injection molding parts. The visuality of hopper receiver enables us to see the material situation inside the hopper. The hopper receiver is suitable for this system, since its material capacity is not large. With a PLC central controller for a whole-process monitor, the system is of good reliability and expandability. In addition, the layout of pipes is based on the spot, which is safe, nice, cost saving and economically effective. The whole system is of smooth operation and easy control, which meets customer requirements of realizing auto operation and plays an important role in pushing developments for customers.
This system greatly saves cost of man power, resources and energy.
Shini designed a final solution according to the client requirements and send an engineer to examine on the spot, to measure to confirm some related data, and to learn customer requirements. Then work out a 1:1 3D construction drawing according to the situation on the ground, the data and the customer requirements. The whole set of project is installed completely according to the construction drawing and under strict supervision by a supervisor appointed by the customer. It’s of overall planning and scientific selection from planning to construction. Besides, the system configuration is considered from multiple perspectives; the construction is of rigorous science. It not only saves cost and time for equipment to be put into production for customers, but also improves efficiency of construction, saves construction cost and establishes a good image for Shini.
The system planning involves 20 sets of injection molding machine. The raw material is PBT and PA with glass fiber. The conveying distance is 30 meters long and 16 meters wide. Quite many auxiliary equipments are applied in the system. First of all, the conveying parts requires 8 sets of hopper dryer and a honeycomb dehumidifier SD-700H to work together to dehumidify and dry material. Besides, it can accurately control temperature to meet customer requirements toward drying with micro computer control. The material are conveyed to the dryer from the 8 hoppers first and then be sent to the injection molding machine by the distributor after a series of drying. Each injection molding machine has a material pipe. It can well realize switch of material for machines.
Furthermore, it is equipped with a central vacuum generator which possesses a new type of Shini central filter. It can effectively protect the blower. Secondly, we equip a hopper receiver for the injection molding parts. The visuality of hopper receiver enables us to see the material situation inside the hopper. The hopper receiver is suitable for this system, since its material capacity is not large. With a PLC central controller for a whole-process monitor, the system is of good reliability and expandability. In addition, the layout of pipes is based on the spot, which is safe, nice, cost saving and economically effective. The whole system is of smooth operation and easy control, which meets customer requirements of realizing auto operation and plays an important role in pushing developments for customers.
This system greatly saves cost of man power, resources and energy.
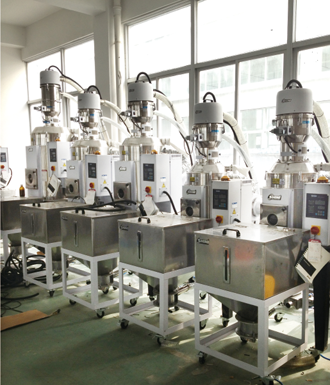