Experience Sharing
2016 Quarter 4 Issue 29
Case Sharing of Central Conveying System
One Group in Hunan province founded in September 1996 is a large private enterprise which has import and export license that integrated the research, production and trade. The company is the global largest thermos manufacturer. It has been honored as the “No.1 sales in China for ten years”.
The client requires planning two workshops in Hunan and Xinjiang provinces with central conveying system for injection molding machine (A represents Xinjiang workshop, B represents Hunan workshop as below), in which the workshop A is planned with 11 sets of central conveying system in 380~550 tons, while the workshop B is planned with 12 sets of central conveying system in 380~550 tons for injection molding machine. Other than different conveying distance and room locations, the auxiliary equipment and conveying method of workshop B is the same. It usually adopts two kinds of materials that no need of drying and dehumidifying. Each unit maximum dosing amount is 50KG/hr. As the steel-frame structure of workshop and plant, which height is up to 7m. As to reduce constructional difficulties and costs, the pipeline is supported by the pipe frame standing on the ground instead of fixing on the wall, which not only features good sight but also saves cost. Each IMM adopts a piece of pipe, with shut-off suction box installed at bottom of storage tank, which ensures no residual in pipeline after each conveying. The latest model of central filter SCSF-200-F-E could reach 5um filtration accuracy. It adopts Taiwan Roots blower SRB-100-V collocated with 11kw Siemens motor, featuring stable air flow with small pressure variation. The control station employing SIEMEMNS PLC to control the SCCS-100-G-C, and the 10.4” large colorful panel monitors all stations’ working condition.
In addition, this system unit also equipped with 6 sets of Volumetric Dosers. The client requires 4% of additional masterbatch, therefore, SCM-16mm screw is selected to meet the client’s requirement of masterbatch in production. Meanwhile, it employs the Water Chiller SIC-14W-R2 adopting CFC-free refrigerant with excellent refrigeration effect, as well as the 1/2’’ 4-in-4-out water flow regulator, to cool down the moulds in two sets of IMM simultaneously.
The two systems of workshop A and B will be completed in May and June successively. The system works stably since the acceptance, which achieved the original intention for client in conveying system application. Except for cost saving, it makes the workshop cleaner and tidier. In a word, the advantage of central conveying system perfectly fulfilled in this system.
The client requires planning two workshops in Hunan and Xinjiang provinces with central conveying system for injection molding machine (A represents Xinjiang workshop, B represents Hunan workshop as below), in which the workshop A is planned with 11 sets of central conveying system in 380~550 tons, while the workshop B is planned with 12 sets of central conveying system in 380~550 tons for injection molding machine. Other than different conveying distance and room locations, the auxiliary equipment and conveying method of workshop B is the same. It usually adopts two kinds of materials that no need of drying and dehumidifying. Each unit maximum dosing amount is 50KG/hr. As the steel-frame structure of workshop and plant, which height is up to 7m. As to reduce constructional difficulties and costs, the pipeline is supported by the pipe frame standing on the ground instead of fixing on the wall, which not only features good sight but also saves cost. Each IMM adopts a piece of pipe, with shut-off suction box installed at bottom of storage tank, which ensures no residual in pipeline after each conveying. The latest model of central filter SCSF-200-F-E could reach 5um filtration accuracy. It adopts Taiwan Roots blower SRB-100-V collocated with 11kw Siemens motor, featuring stable air flow with small pressure variation. The control station employing SIEMEMNS PLC to control the SCCS-100-G-C, and the 10.4” large colorful panel monitors all stations’ working condition.
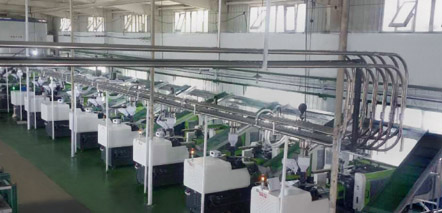
In addition, this system unit also equipped with 6 sets of Volumetric Dosers. The client requires 4% of additional masterbatch, therefore, SCM-16mm screw is selected to meet the client’s requirement of masterbatch in production. Meanwhile, it employs the Water Chiller SIC-14W-R2 adopting CFC-free refrigerant with excellent refrigeration effect, as well as the 1/2’’ 4-in-4-out water flow regulator, to cool down the moulds in two sets of IMM simultaneously.
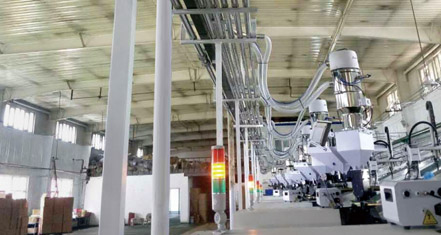
The two systems of workshop A and B will be completed in May and June successively. The system works stably since the acceptance, which achieved the original intention for client in conveying system application. Except for cost saving, it makes the workshop cleaner and tidier. In a word, the advantage of central conveying system perfectly fulfilled in this system.
Experience Sharing
- STM and Extruder Integrated Control
- Central Conveying System Facilitates Enterprise’s Transformation and Upgrading
- Shini Modular Dryer Used in Pelletizing Industry
- Case Studies -- Shini Automation Application in Food Industry
If you want to read other articles, back to2016 Quarter 4 Issue 29.