Special Reports
2021 Quarter 2 Issue 43
The Review of Chinaplas2021@Shini Group
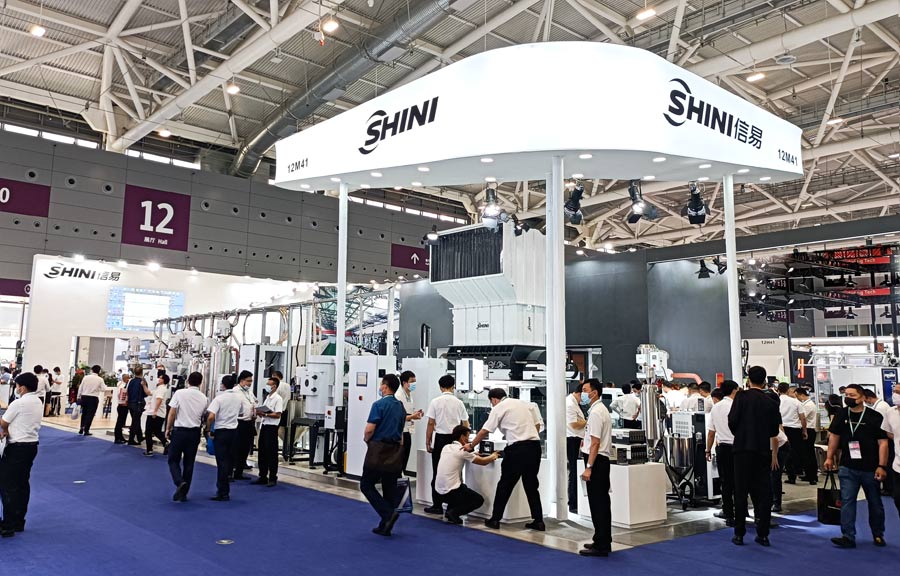
1.Central Material Processing Technology
This system is assembled with multiple new products and technologies, such as material conveying, automatic proportional mixing, smart dehumidifying and drying, material distribution, material consumption monitor for hopper receiver, and piping system, which achieves over all process integration of the materials from the input end to the output end. All the equipment supports the communicating function, and the central material control station is equipped with the cloud control module. Meanwhile, all these designs lay a solid foundation for the intelligent material processing system in the injection molding process.
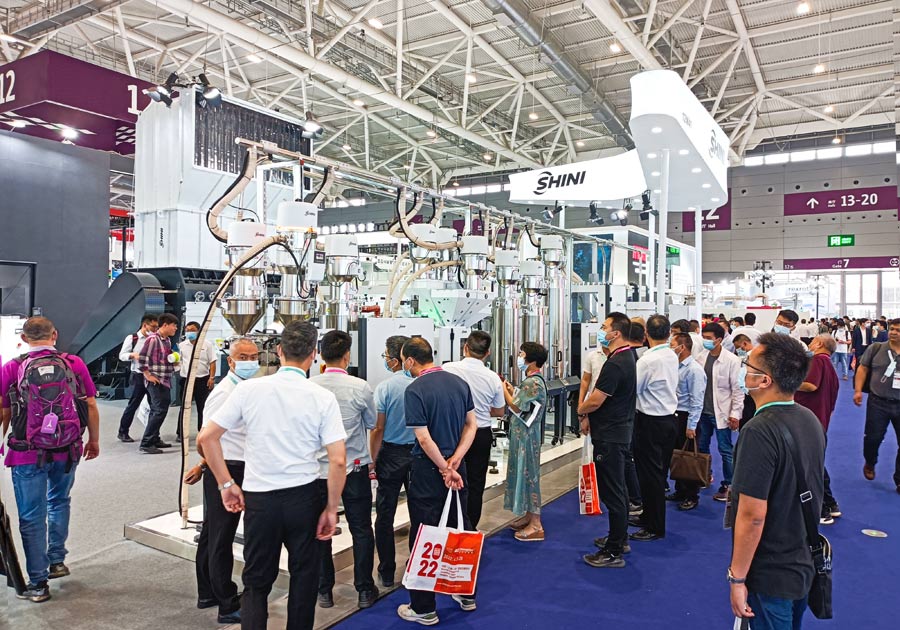
- Shini Material Consumption Monitor for Hopper Receiver
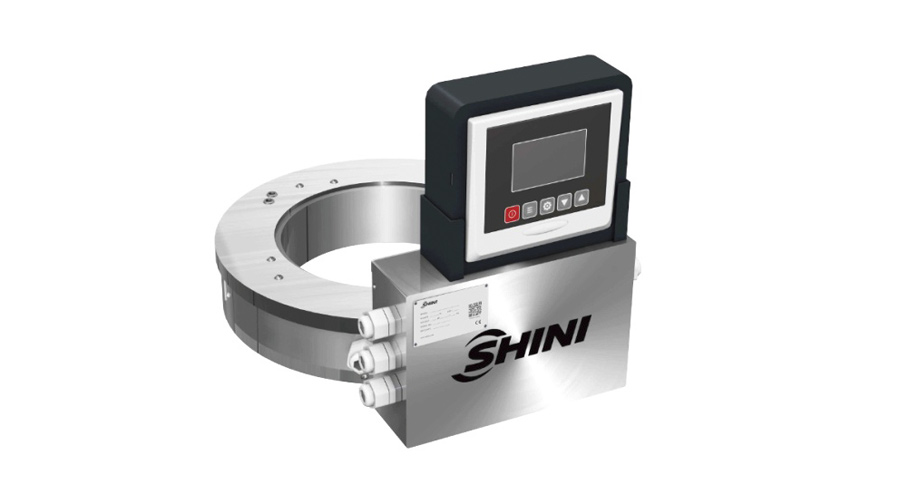
As a brand-new product, it conforms to the trend of intelligent molding, which is suitable for self-contained hopper loader and conveying system with the material shut-off function. It can monitor the dosage of materials conveying to the feed port of the injection molding machine and realize closed-loop detection of the material consumption. According to the comparison of consumed materials conveying to the IMM’s feed port and the product qualified ratio, the operator can record the product qualified ratio, monitor the production, and find the abnormalities of material consumption, which can improve the output with specific measures and cut down the production cost caused by the waste of materials. The standard RS485 communication function can transfer the real-time weight parameters collected to the host computer or intelligent system and compare with the calibration value to find the abnormalities and process improvement methods. Meanwhile, the product and material contact surfaces are made of stainless steel that can ensure no material contamination and the max. detection accuracy can reach +/-1%, which can control the production batch automatically according to the preset yield. Meanwhile, the SMM can also feed materials to the drying system to reduce conventional material drying and replace time and improve production efficiency.
- SEL Shini Central Material Distribution Station
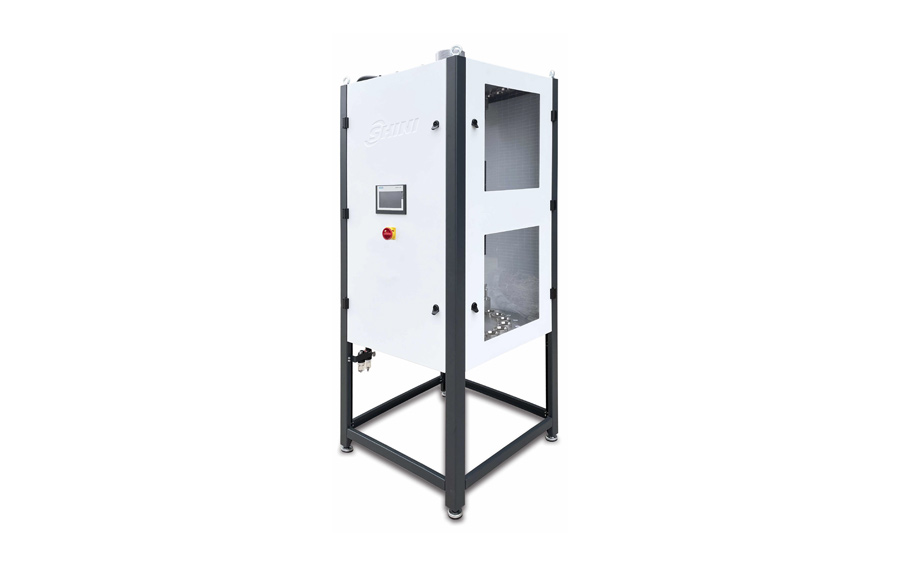
Shini Central Material Distribution Station SEL can control max. twenty material sources and 20 terminals, enabling the configuration of one material to any terminal. Fully automatic conveying without operation avoids human mistakes and pollution. The fully automated process is achieved through PLC control, and manual control is also available. It has a localization monitoring function and failure auto alarm function.
2. Mold Temp. Control Technology
The mould temperature control technology presents the latest quick heating and cooling solution of Shini Group, and the whole plan is composed of a control station, high temp. The mould controller, a dual-purpose water/oil heater and intelligent flow regulator, provides the necessary product support for the high gloss molding process in a more flexible way.
- STM-W/O Shini Dual-purpose Water/Oil Heater
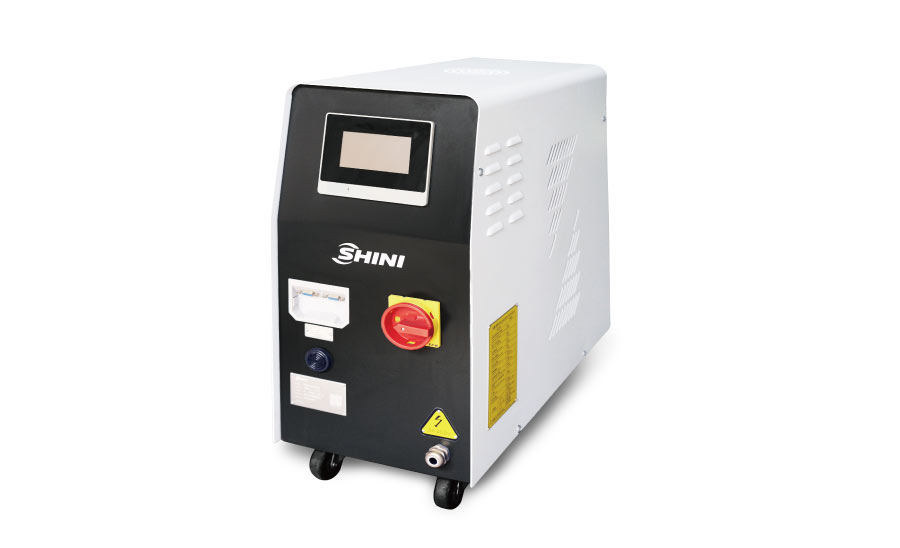
Shini latest STM-W/O series Dual-purpose Water/Oil Heater is used as mould heater and maintains mould temperature, which can also be used in other similar applications. This unit can use water or heating oil as the heat transfer medium according to different conditions, and the maximum temperature can reach90℃ (for water) and 160℃ (for oil). The heating power can switch between 3KW,6KW, and 9KW to meet various production process needs, thus giving play to multiple functions. Compared with most conventional button interfaces on the market, the 4.3” display screen adopts a more friendly, intuitive, and easy-to-operational touch panel. The P.I.D multi-stage temperature control system can maintain a mould temperature with an accuracy of ±0.5℃(0.9℉).
This product has a pump reverse emptying function, and it can eliminate the fluid in the mould by the one-button press when replacing the mould to improve the mould replacing speed. This also ensures continuous production of the pipeline in case of micro leakage, and it is designed with the negative pressure running function. When activating the negative pressure running function, it can reverse the equipment’s outlet and inlet and temporarily repair the micro leaking points of the equipment’s outlet to ensure continuous production. Thus, the equipment can be repaired after it finishes the production orders. The product has multiple safety protectors and alarms for the reverse phase, pump overload, overheat, and low-level circumstances to ensure safety when using the equipment. With the supports of the RS485 interface, it lays the foundation of data sharing and realizes data interconnection with other intelligent devices or systems, which consolidates the basis of intelligent molding. Besides, this series of products are designed with many options, such as medium-return temperature, flow, and digital pressure gauge, to meet a broader range of molding process demands.
- Shini Mould Temp. Controllers
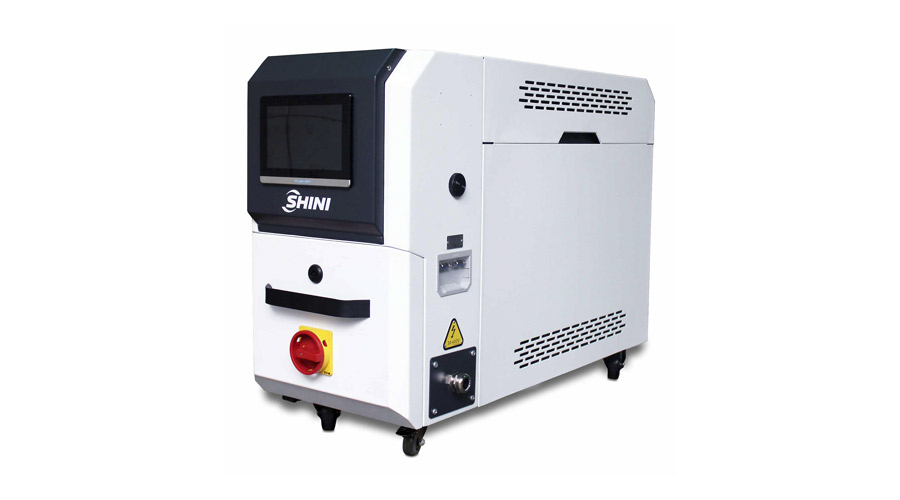
STM-SPW high-end high-temp. water heater is mainly used to heat the mould and maintain a constant temperature. Besides, when used in other fields with similar demands, this series of models applies to PT100 thermoelectric resistance and overall SSR temperature control, which has more stable temperature accuracy control than the standard TCU STM-PW maximum heating temperature can reach 200℃. Equipped with the electronic flow meter and pressure gauge, it’s easy to monitor the water flow rate and pressure in real-time, going through the RS485 interface to achieve information intelligent monitoring and management.
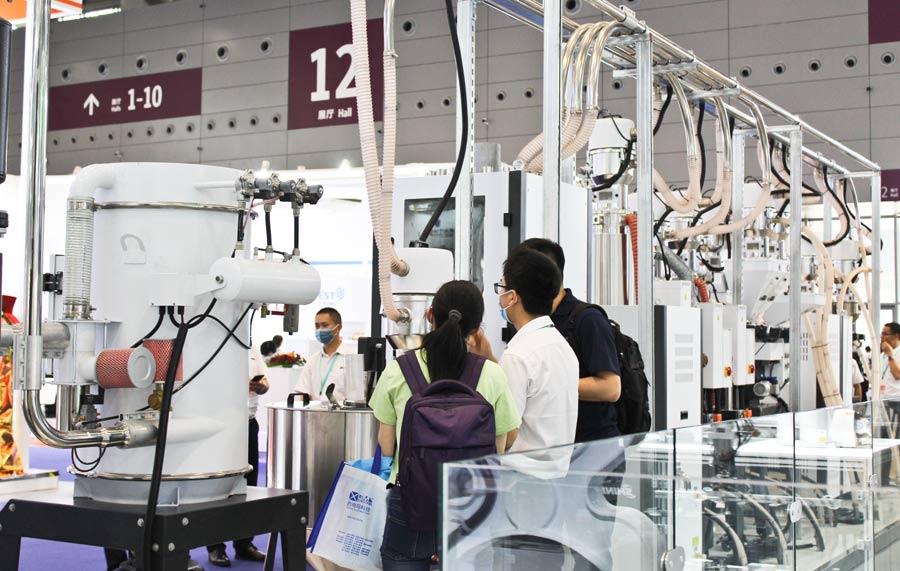
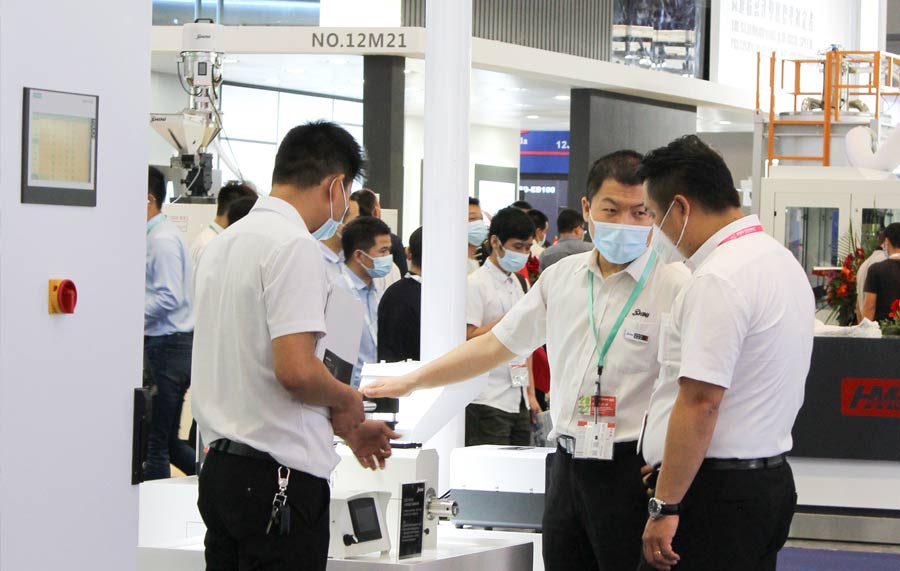
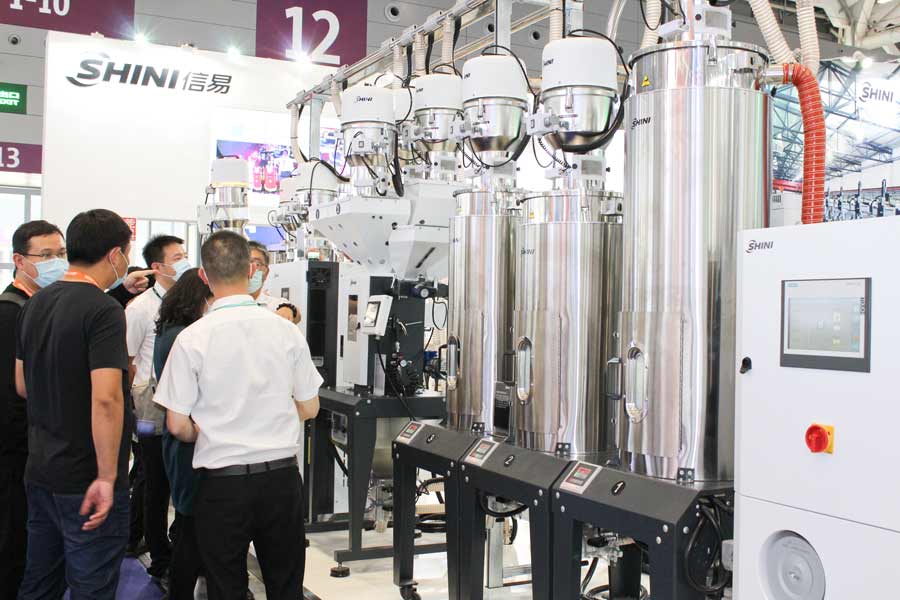
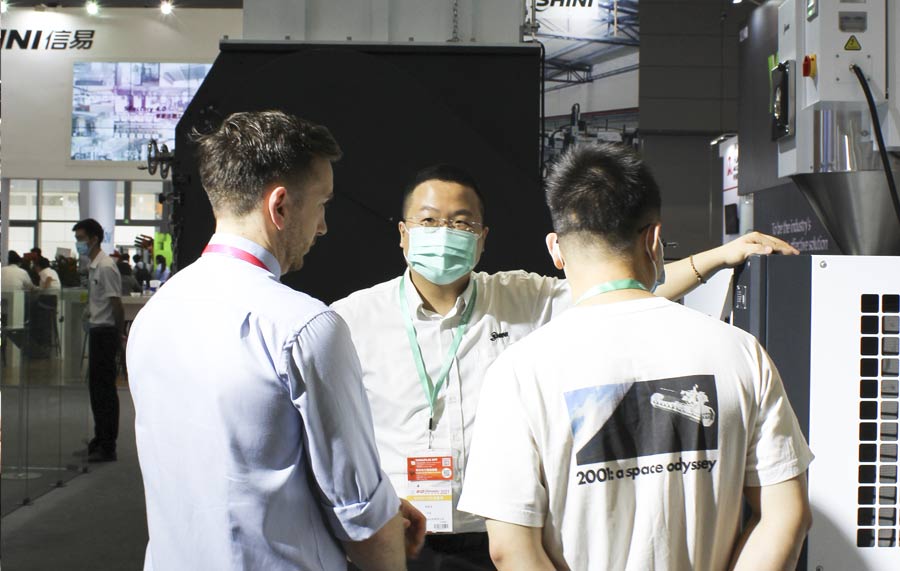
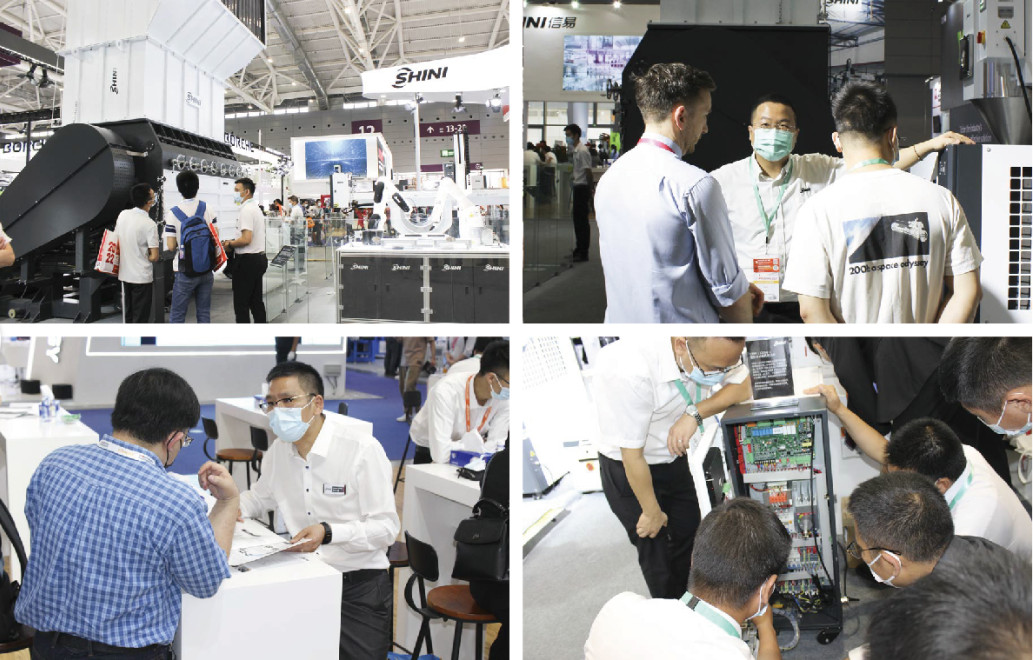
Special Reports
If you want to read other articles, back to2021 Quarter 2 Issue 43.