Special Reports
2013 Quarter 3 Issue 16
The Principle and Application of Industrial Air Chiller
In plastic molding industry, molding speed and film quality of film extruder have something to do with cooling time. Air-cooling cabinet produces cooling air by using chilled water from chiller and exchange heat in heat exchanger. However, industrial air chiller integrates the two into one unit to improve the cooling effect and simplify the structure of auxiliary equipments.
Classification of industrial air chiller
Based on different cooling principle, industrial air chiller can be divided into two types. One is evaporative air chiller whose working principle is when started up, negative pressure forms inside blower to make the outside air pass through a porous wet curtain so as to force dry bulb temperature of the air dropped to the same level of the wet bulb temperature of outside air. In other words, the dry bulb temperature in the blower outlet is 5-12℃ lower than that of the outside. The temperature difference is bigger when the outside air get drier and hotter, thus the cooling effect gets better and better. For evaporative air chiller, the price is lower than other type of air chiller and structure is much simpler, but its temperature controlling is not so favorable (depends on the temperature difference between ambient temperature and the wet curtain water). Usually, this kind of air chiller is used to lower the temperature and increase humidity of the workshop.
The other type is using refrigerating system to cool down the air and to force the air temperature to drop to the required value. The structure is more complicated and the price is much higher because refrigerating system is equipped. However, the cooling effect is improved greatly and temperature can be adjustable according to actual needs. In plastic molding fields, this kind of air chiller can be used to increase cooling speed of film and improve productivity. Also it can be used in spraying industry, household appliance and food industries.
Working Principle
This time, we introduce you the industrial air chiller with refrigerating system. This kind of air chiller can be divided into two types: direct cooling and indirect cooling types. What is the difference between those two cooling types and what are strengths and weaknesses? The following comparative introductions can give you a general idea of them.
1.Direct Cooling Type
In refrigerating system, low temperature low pressure gas is compressed into high temperature high pressure gas by compressor and then enters into the condenser (finned tube or tube-in-shell type) to cool down, and then goes into the drier filter to get dried and filtered, then it enters into the expansion valve to lower its temperature and pressure. At the same time, with the help of blower, outside air flow continuously cross evaporator. Heat quantity within air is taken away by heat exchanging. Therefore, the required air temperature is achieved.
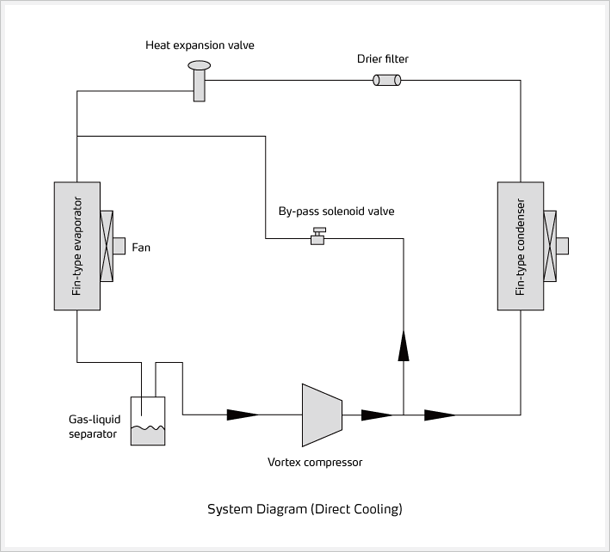
Classification of industrial air chiller
Based on different cooling principle, industrial air chiller can be divided into two types. One is evaporative air chiller whose working principle is when started up, negative pressure forms inside blower to make the outside air pass through a porous wet curtain so as to force dry bulb temperature of the air dropped to the same level of the wet bulb temperature of outside air. In other words, the dry bulb temperature in the blower outlet is 5-12℃ lower than that of the outside. The temperature difference is bigger when the outside air get drier and hotter, thus the cooling effect gets better and better. For evaporative air chiller, the price is lower than other type of air chiller and structure is much simpler, but its temperature controlling is not so favorable (depends on the temperature difference between ambient temperature and the wet curtain water). Usually, this kind of air chiller is used to lower the temperature and increase humidity of the workshop.
The other type is using refrigerating system to cool down the air and to force the air temperature to drop to the required value. The structure is more complicated and the price is much higher because refrigerating system is equipped. However, the cooling effect is improved greatly and temperature can be adjustable according to actual needs. In plastic molding fields, this kind of air chiller can be used to increase cooling speed of film and improve productivity. Also it can be used in spraying industry, household appliance and food industries.
Working Principle
This time, we introduce you the industrial air chiller with refrigerating system. This kind of air chiller can be divided into two types: direct cooling and indirect cooling types. What is the difference between those two cooling types and what are strengths and weaknesses? The following comparative introductions can give you a general idea of them.
1.Direct Cooling Type
In refrigerating system, low temperature low pressure gas is compressed into high temperature high pressure gas by compressor and then enters into the condenser (finned tube or tube-in-shell type) to cool down, and then goes into the drier filter to get dried and filtered, then it enters into the expansion valve to lower its temperature and pressure. At the same time, with the help of blower, outside air flow continuously cross evaporator. Heat quantity within air is taken away by heat exchanging. Therefore, the required air temperature is achieved.
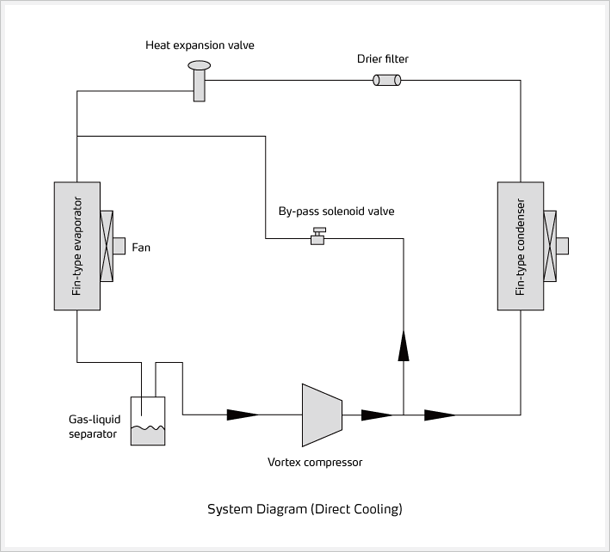
2.Indirect Cooling Type
In refrigerating system, compressor compresses the low temperature low pressure gas into high temperature high pressure gas, and then the gas enters into the condenser (finned tube or tube-in-shell type) to get cooled, pass through filter to get dried and filtered, enter into expansion valve to lower its temperature and pressure, and then it comes into the evaporator (tube-in-shell type or plate heat exchanger) to lower the temperature of cooling medium such as water, after that cooling medium was conveyed into the liquid heat transfer coil, with the help of blower, cooling medium exchange heat with the air and heat contained in air is taken away, thus required air temperature is achieved.
3.The difference between the two cooling types.
The structure of direct cooling system is much simpler and with less components which help to lower the initial cost. Also because of the simple structure, the probability of troubles and failures is much lower. However, the return air of the direct cooling system is from the surrounding air which is easily affected by the environment and condition. So the deviation of outlet air temperature controlling is a little bigger.
Compared with the direct cooling system, the indirect ones have much complicated structure and bigger size for more components, such as pump, water tank and evaporator, are added in the system. Indirect cooling system adopts cooling medium which is quite stable in temperature to exchange heat with the air. The temperature control is much preciser than direct cooling system. The operation of refrigerant system is less influenced by evaporation condition.
Therefore, the direct cooing system is more competitive in applications without temperature accuracy requirements while the indirect cooling system is better at temperature controlling precision and can better satisfy the customers.
Industrial Air Chiller
In plastic molding industry, air chiller can work together with film extruder. Usually the suitable temperature for film extrusion is about 15-20℃ which can be met by direct cooling system. The development of industrial air chiller can help customers reduce the cost of purchasing other relevant equipment and improve competitiveness.
• Temperature range: 10℃~20℃
• Air quantity: ≥3000m³/h
• Temperature control accuracy: ±1℃
• Cop of refrigerating system can reach to 3.5
• Direct cooling with simple structure, easy to operate.
• Blower is optional and the size is changeable according to the air quantity and temperature requirements.
• When ambient temperature is low, outlet air temperature can be adjusted by supplying external air.
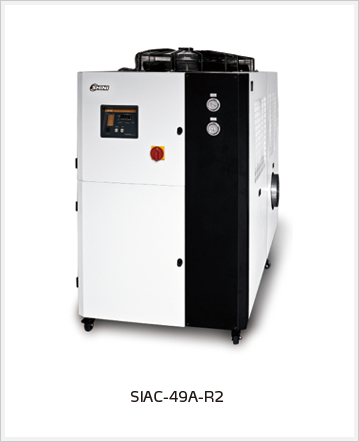
In refrigerating system, compressor compresses the low temperature low pressure gas into high temperature high pressure gas, and then the gas enters into the condenser (finned tube or tube-in-shell type) to get cooled, pass through filter to get dried and filtered, enter into expansion valve to lower its temperature and pressure, and then it comes into the evaporator (tube-in-shell type or plate heat exchanger) to lower the temperature of cooling medium such as water, after that cooling medium was conveyed into the liquid heat transfer coil, with the help of blower, cooling medium exchange heat with the air and heat contained in air is taken away, thus required air temperature is achieved.
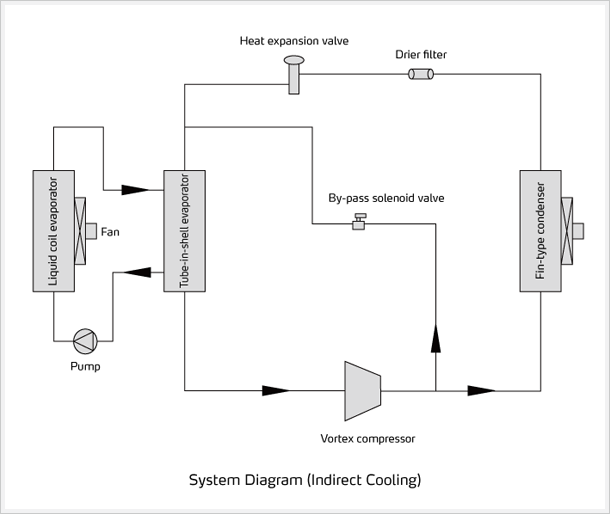
3.The difference between the two cooling types.
The structure of direct cooling system is much simpler and with less components which help to lower the initial cost. Also because of the simple structure, the probability of troubles and failures is much lower. However, the return air of the direct cooling system is from the surrounding air which is easily affected by the environment and condition. So the deviation of outlet air temperature controlling is a little bigger.
Compared with the direct cooling system, the indirect ones have much complicated structure and bigger size for more components, such as pump, water tank and evaporator, are added in the system. Indirect cooling system adopts cooling medium which is quite stable in temperature to exchange heat with the air. The temperature control is much preciser than direct cooling system. The operation of refrigerant system is less influenced by evaporation condition.
Therefore, the direct cooing system is more competitive in applications without temperature accuracy requirements while the indirect cooling system is better at temperature controlling precision and can better satisfy the customers.
In plastic molding industry, air chiller can work together with film extruder. Usually the suitable temperature for film extrusion is about 15-20℃ which can be met by direct cooling system. The development of industrial air chiller can help customers reduce the cost of purchasing other relevant equipment and improve competitiveness.
• Temperature range: 10℃~20℃
• Air quantity: ≥3000m³/h
• Temperature control accuracy: ±1℃
• Cop of refrigerating system can reach to 3.5
• Direct cooling with simple structure, easy to operate.
• Blower is optional and the size is changeable according to the air quantity and temperature requirements.
• When ambient temperature is low, outlet air temperature can be adjusted by supplying external air.
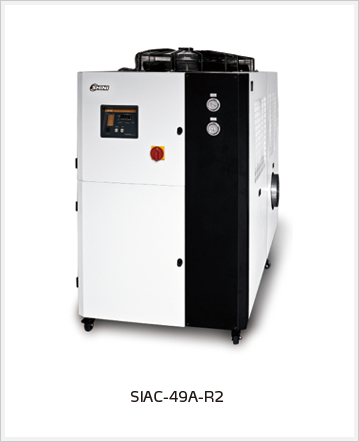
Special Reports
- Starve Feeding
- Cold Mold Sweat Dehumidifier
- Temperature Control in Hot Runner System——Heaters
- New Brand Image Shines at CHINAPLAS 2013
- About CHINAPLAS 2013 of Shini-Syncro Extrusion
If you want to read other articles, back to2013 Quarter 3 Issue 16.