Experience Sharing
2014 Quarter 1 Issue 18
The Successful Application of Shini Central Chilling Water System
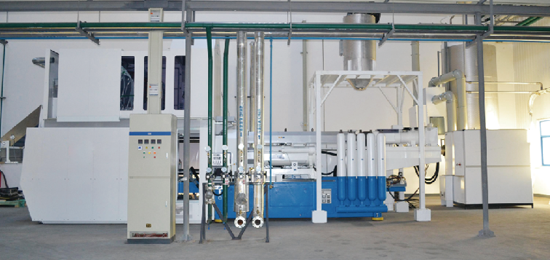
In 2013, Shini built a central chilling water system for this company. Here are the client’s requirements: the main pipe flow is 90.0m3/h; the constant pressure is 6bar; the outlet water temperature is 8~11℃; the temperature difference is 1~3℃; in the mold water pressure is at 4bar and the flow is 9.0m3/h; in the dehumidifying system water pressure is at 6bar and the flow is 18.0m3/h. Shini send related technical personnels to the company and select the suitable model to meet client’s requirements basing on practical situation. They also design suitable pipelines for the client.
System Features:
•Combine 4 sets of water chiller module at 120 KW each. Total refrigerating capacity is 480KW.
•Adopt closed loop pipeline and possess functions of differential pressure with automatic water filling, exhausting and stopping for automatic pressure relief.
•Use anti-vibrating connector to connect the main machine and the main pipe.
•Failures occurs in one water chiller module won’t stop the whole central water chilling system.
•With microcomputer for precise control, it can display outlet water temperature, return water temperature and water pressure. When the module of water chillers is running, it will automatically make the corresponding water chiller stop or start according to work load, which is more energy-saving.
•Level of protection: IP54
This system applies to the molding machine whose molding ability is 1350kg/hr. Its products are PET preforms and the product quantity of each mold is 160 cavities. Therefore, it’s necessary to strictly control its refrigerating capacity and cold water pressure. The whole system’s temperature should be controlled within 8℃~11℃. The main pipe is DN125; its pressure is 6bar and the throughput is 108m3/h. The branch pipe to the molding machine is DN100 and its throughput is controlled to be 90m3/h while the water temperature is 8℃; the throughput is controlled to be 90m3/h and the water temperature be 8℃. The water outlet pipe of the molding machine is DN150. The branch pipe to the mold is DN25 and its pressure is 4bar while its throughput is 9.0m3/h; its water temperature is 8℃. The water outlet pipe of the mold is DN50. The branch pipe to the dehumidifying system is DN40; its water pressure is 6bar; throughput is 18m3/h and the water temperature is 8℃. The water outlet of the dehumidifying system is DN50. All pipes of the water outlet confluence adopt DN150 and their throughput is 108m3/h. The pipe which connects the water outlet and the machine is DN125. With high pressure water pump of world known brand, its throughput is 120m3/h. The deviation of the whole pipe pressure should be controlled under 1bar and the temperature difference be 3℃.
In order to avoid insufficient of water pressure and damages caused by forced shutdown, there are water flow switch installed at the return water port and water outlet. Besides, there are temperature gauges installed at the return water port and water outlet for precisely measuring the water temperature of the water inlet and outlet. What’s more, there are water pressure gauges at the inlet and outlet of all branch pipes for real-time monitor of water pressure.
There are auto devices of exhausting, supplying water and pressure relief at the pipes between all confluences of water outlets and the water inlet of water pump for better preventing water chillers from damages which are caused by short of water and over pressure. This system is completed in Sept. 2013 and has passed through client’s all kinds of rigorous tests. It meets the working conditions for the client. Besides, it has been approved by the engineers in the client’s company. It still works well now. This case further shows Shini’s strong technical strength and reflects shini’s positioning of high-end brand in international field.
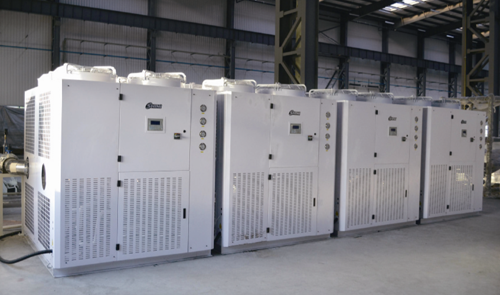
Experience Sharing
- Analysis of Irregular Material Metering of SGB
- The Application of Granulating and Recycling System in Recycle Industry
If you want to read other articles, back to2014 Quarter 1 Issue 18.