Special Reports
2015 Quarter 1 Issue 22
sLink Protocol Solution
sLink Protocol Solution from Shini is the first of auxiliary equipment manufacture, it’s sole purpose is to integrate control of auxiliary equipment with IMM, extrusion, centralize control or PC from other supplier. sLink utilize license free and openly available Modbus TCP/RTU protocol. This is one of innovative simple solution from Shini.
Technology Features
Controllers of the auxiliary equipment have Ethernet function or RS485 communication ports, adopting industrial Modbus protocol which is commonly used all over the world for data communication.
The system can connect the injection molding machine and auxiliary equipment via Ethernet or RS485 communication ports. The injection molding machine and other upper computers can read data from slave stations like dryer, mold temperature controller, blender, loader, water chiller and robot for central control.
With this techology, the operator can set the main control unit at the office or other places for central control and operate the slave station on spot conveniently.
The protocol and data-collection software, checklists of each production machine can be set up which are convenient for searching of production process parameters and products quality analysis at end of the process.
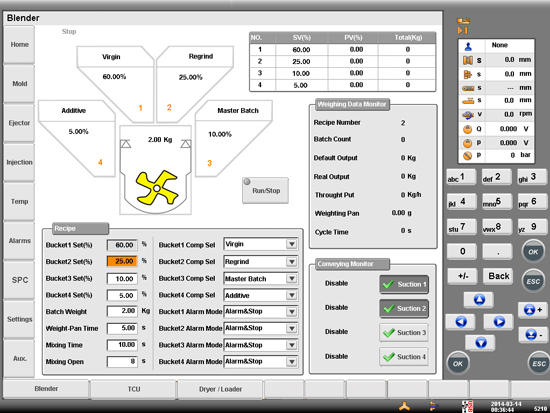
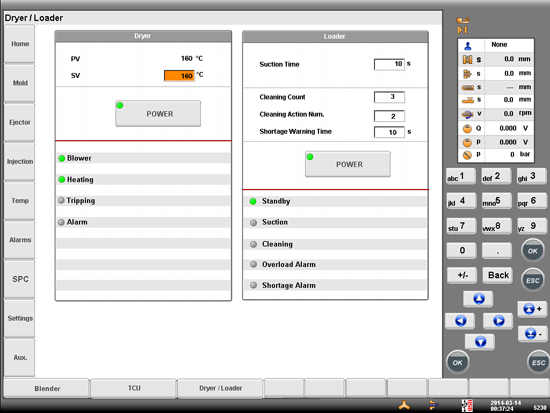
Application
Centralized monitoring system of large auxiliary equipment
The centralized monitoring system can connect the host machine with all the auxiliary equipments in workshop through Ethernet. By strong data management capability, direct and easy operation of the host machine, it can provide the customer with more advanced and efficient management capability which helps to meet the products quality and cost control requirements from the customer.
Injection control system integrated auxiliary monitoring function
Via Ethernet, the injection control system connects the auxiliary equipment to the injection molding machine which integrates the IMM’s control system with auxiliary monitoring function. The auxiliary monitoring function integrated injection control system will make the whole injection processing more efficient, more intelligent which can cut down the operators and lower the costs. Shini is now collaborating with the host machine’s factory actively which dedicated to integrate the host machine’s control system with Shini auxiliary equipment’s monitoring function. As to improve the automation degree of the whole technological process and enhance the market competitiveness.
Mold/material temperature centralized monitoring system
Via RS485, the system will connect several mould temperature controllers or dryers to the HMI. By the round touch panel of the colorful HMI, users can centralize monitoring mold’s various return temperature and various materials drying temperature. This system with easy operation is suitable for monitoring of large mold’s various return temperature and material workshop’s drying temperature applications.
Technology Features
Controllers of the auxiliary equipment have Ethernet function or RS485 communication ports, adopting industrial Modbus protocol which is commonly used all over the world for data communication.
The system can connect the injection molding machine and auxiliary equipment via Ethernet or RS485 communication ports. The injection molding machine and other upper computers can read data from slave stations like dryer, mold temperature controller, blender, loader, water chiller and robot for central control.
With this techology, the operator can set the main control unit at the office or other places for central control and operate the slave station on spot conveniently.
The protocol and data-collection software, checklists of each production machine can be set up which are convenient for searching of production process parameters and products quality analysis at end of the process.
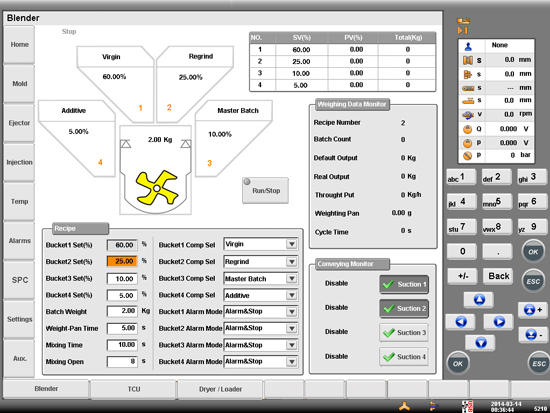
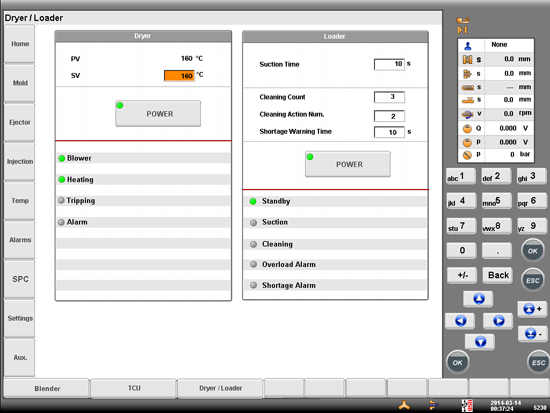
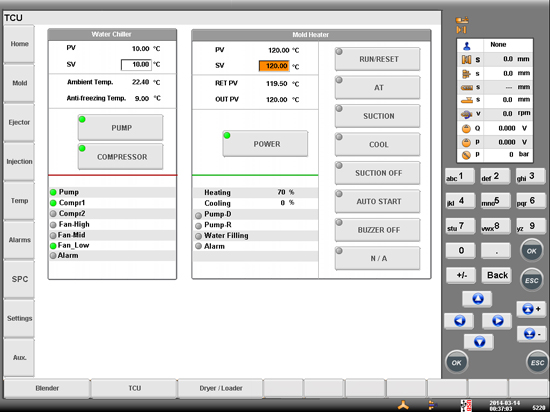
Centralized monitoring system of large auxiliary equipment
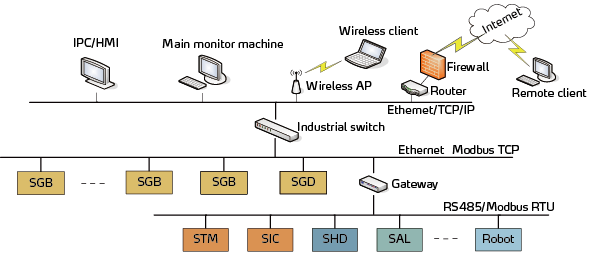
The centralized monitoring system can connect the host machine with all the auxiliary equipments in workshop through Ethernet. By strong data management capability, direct and easy operation of the host machine, it can provide the customer with more advanced and efficient management capability which helps to meet the products quality and cost control requirements from the customer.
Injection control system integrated auxiliary monitoring function
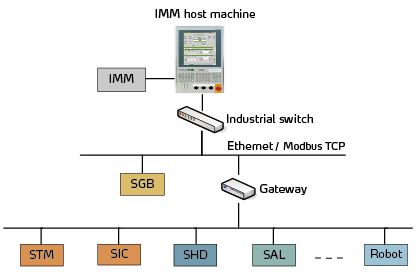
Via Ethernet, the injection control system connects the auxiliary equipment to the injection molding machine which integrates the IMM’s control system with auxiliary monitoring function. The auxiliary monitoring function integrated injection control system will make the whole injection processing more efficient, more intelligent which can cut down the operators and lower the costs. Shini is now collaborating with the host machine’s factory actively which dedicated to integrate the host machine’s control system with Shini auxiliary equipment’s monitoring function. As to improve the automation degree of the whole technological process and enhance the market competitiveness.
Mold/material temperature centralized monitoring system
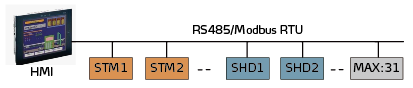
Via RS485, the system will connect several mould temperature controllers or dryers to the HMI. By the round touch panel of the colorful HMI, users can centralize monitoring mold’s various return temperature and various materials drying temperature. This system with easy operation is suitable for monitoring of large mold’s various return temperature and material workshop’s drying temperature applications.
Special Reports
- The Preview of Shini Auxiliary Equipment on Chinaplas2015 Show
- Mold Sweat Dehumidifier Upgrade
- Teflon Coating Applied in SGB
- Shini Robot Introduction
- Hot runner introduction
- Shini Japan
If you want to read other articles, back to2015 Quarter 1 Issue 22.