Special Reports
2016 Quarter 3 Issue 28
Exhibition News of Chinaplas2016
As the Asian largest plastics & rubber exhibition, CHINAPLAS is always a platform to attract the top-level professional exhibitors and visitors globally, and it provides an interactive platform for the practitioners in plastic industry. The four-day exhibition of CHINAPLAS 2016 was grandly held in Shanghai New International Expo Center (Pudong) during April 25th~28th, which gathered more than 3,300 exhibitors and exhibiting groups from different countries worldwide. As the global leader in auxiliary equipment industry, Shini also presented perfectly in the exhibition, especially is the striking intelligent solutions which was well received by the partner and customer.
According to official data, revealed that there are over 40,000 visitors attending this exhibition on the first day. The total number of visitors during these four days was approximately 150,000, with 3,300 exhibitors covering 240,000 square meters. Both the number of exhibitor and visitor has reached the highest levels ever.
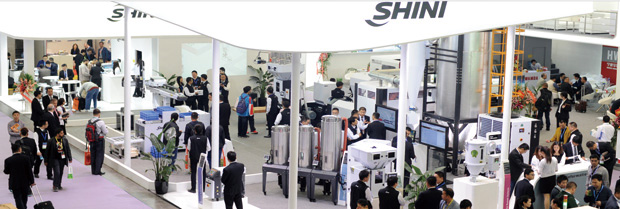
Intelligent System Solutions
Global manufacturing based countries have formulated corresponding national strategy to adapt transformation in new era and upgrade its industrial competitiveness. China’s proposal “Made in China 2025” activated the great strength of road for the Made in China, which was focused on the core of intelligent manufacturing: the intellectualization of production process, equipment manufacturing and product. It is estimated that in next 10 years, the intelligent manufacturing will be involved in each field, and the plastics and rubber industry has no exception. Similarly as China’s manufacturing in other fields, the plastics and rubber industry is getting into the new age of intelligent manufacturing with upgrade and transformation.
As the leading brand engaged in production of the plastic auxiliary equipment, Shini displayed the integrated control technology of sLink based on the network. Through the standard network carrier, it achieved central monitoring and data processing of the IMM’s host unit and all the peripheral auxiliary equipment. This technology received a great deal of acknowledgement from the partners and customers. There are quite a few manufacturers renowned in the industry, such as HAITIAN, BOTCH, YIZUMI, DONGHUA, Sumitomo and Victor Taichung etc., has embedded SHINI equipment along with sLink technology, to fulfill intelligent injection molding. At the same time, Shini demonstrated data acquisition system and MES system won the praise of the visitors correspondingly. The data acquisition system can process data acquisition and processing for related molding machines of customer’s entire plant, which set up a bridge between the molding equipment and the MES system, offering professional pre-processing of data acquisition for the MES system. After MES system processing the data it acquired in future step, it sent the data to the ERP system, which presented diverse advertisements for different users to make reasonable decisions in time. All the acquired data should be recorded as important information to provide accurate data foundation for the next process control and product improvement.
In the exhibition, we also displayed the SCIG (Shini Collective Storage System) and AGV (Automated Guided Vehicle) automation solutions. The process was after the products were packed in cartons, they were collected in the system; The AGV vehicle transported all these cartons to product area for delivery. After delivery, the vehicle moved to the material-turnover-area to pick other cartons for next storage, and then transported the cartons to product-delivery-area again with full-load system, and repeated this circulation. The SCIG system is applicable to the conveying after product’s piling up and collection. The multilayer empty carton was packed in the empty-carton-area on SCIG system, while the monolayer carton was conveyed to the product-stacking area by the conveying belt. After the products were picked out from the IMM and laid up in the cartons by Robots, the up-down server then piled up the full-load carton above another and transported other empty cartons to the product-stacking-area to repeat the circulation. Afterward, the finished cartons were conveyed to SCIG shipment area and waiting for the AGV vehicle for delivery. The AGV also named as automatic driverless cart. It is an automated guided vehicle, which can follow the required route to complete the appointed tasks according to preset course and program. For modern intelligent plant, AGV not only features reduced operator but also could withstand the heavy load.
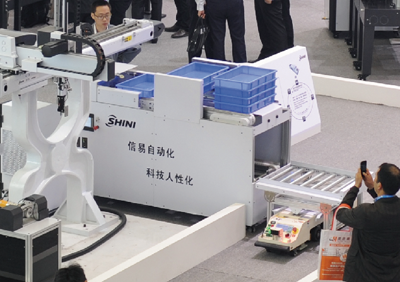
Intelligent Equipment
Large Drying and Dehumidifying System of energy saving model is equipped with intelligent control system of drying airflow, it can automatically adjust airflow according to the temperature of air exhausted from the hopper, which saves energy and prevents material over-drying. In addition, this set of equipment also outfitted with recycling device of regeneration heat, it maximum reduces the consumption power of machine and cut down the cost. This brand new design of drying hopper optimized the proportion of hopper structure, making more consistent drying time of material in the hopper, which ensures better drying effect.
“One to three” Smart Modular Dryer SSMD-U consists of a Honeycomb Dehumidifier SD-200H-SM4 and three sets of modular drying hoppers (MHD-80U, MHD-120U and MHD-160). The drying air pipeline of each hopper and electrical connection line can be conveniently connected to the dehumidifier, which improves the efficiency of equipment installation. All the drying hoppers shares the main pipeline, through the main pipeline, the drying air is exhausted from the outlet of dehumidifier. Then via the branch pipe that on the main pipeline, it enters into different drying hoppers. After drying, the hot air is exhausted from the outlet and return to the main pipeline of return air. At last, it gets back to the Honeycomb Dehumidifier. During the process, there are the airflow sensor and adjusting valve equipped on each branch that entering the drying hopper. Once airflow sensor detected the variation of airflow, it will send this message to central control unit, and accordingly the unit will control the airflow adjusting valve to achieve airflow automatic adjustment and distribution. The automatic distribution technology of drying airflow according to needs mainly manifests that when the dew point of drying air is -40℃/-40℉, it can be automatically distributed to each drying hopper via automatic control system, which reaches rational use of drying air, reduces waste, and prevents material less or over drying. Meanwhile, the drying temperature of each hopper also can be controlled according to need independently.
Energy-saving Equipment
The common model of Dryer is a kind of plastic auxiliary equipment that used most frequently in the market and it is also one of the largest demands. Product technical requirement is not high, with comparatively a transparent price, it faces fierce competition. Different from the common models, Shini exhibited energy-saving dryer featuring obvious superiority, and the energy saving is the development trend that approved by the whole society, which not only benefits the people but profits the whole country. It adopts dual effective & energy-saving heater which helps save 30% energy more than the traditional heater. The energy-saving heater has self-protection function that making the machine won’t be damaged by the damage of blower and failure of contactor. It standard equipped with microcomputer control and RS485 communication function port for convenient central monitoring and data sharing.
At the same time, Shini also displayed the latest Air-cooled Water Chiller in this exhibition. It offers high Coefficient of Performance that exceeding the 1 grade of the China standard, sufficiently improved the energy efficiency. Meanwhile, its patent self-drive mixing tank efficiently balanced the water temperature of water tank. Combined with the optimized structure and production technology, it ensures the machine always working in the reliable condition.
Every Chinaplas has gathered the devoted efforts of each Shini member. From the preparation till the successful ending of exhibition, from product’s data editing to the professional service for the equipment, from product’s demonstration and design to the strict requirement of the details, all above endeavors fully showed our enthusiasm to make the customer more of surprises.
According to official data, revealed that there are over 40,000 visitors attending this exhibition on the first day. The total number of visitors during these four days was approximately 150,000, with 3,300 exhibitors covering 240,000 square meters. Both the number of exhibitor and visitor has reached the highest levels ever.
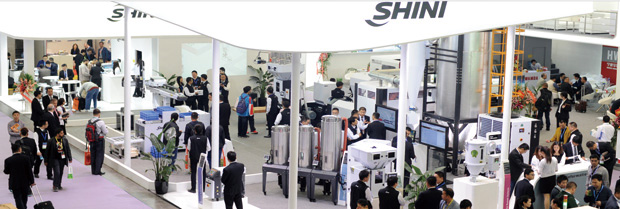
Global manufacturing based countries have formulated corresponding national strategy to adapt transformation in new era and upgrade its industrial competitiveness. China’s proposal “Made in China 2025” activated the great strength of road for the Made in China, which was focused on the core of intelligent manufacturing: the intellectualization of production process, equipment manufacturing and product. It is estimated that in next 10 years, the intelligent manufacturing will be involved in each field, and the plastics and rubber industry has no exception. Similarly as China’s manufacturing in other fields, the plastics and rubber industry is getting into the new age of intelligent manufacturing with upgrade and transformation.
As the leading brand engaged in production of the plastic auxiliary equipment, Shini displayed the integrated control technology of sLink based on the network. Through the standard network carrier, it achieved central monitoring and data processing of the IMM’s host unit and all the peripheral auxiliary equipment. This technology received a great deal of acknowledgement from the partners and customers. There are quite a few manufacturers renowned in the industry, such as HAITIAN, BOTCH, YIZUMI, DONGHUA, Sumitomo and Victor Taichung etc., has embedded SHINI equipment along with sLink technology, to fulfill intelligent injection molding. At the same time, Shini demonstrated data acquisition system and MES system won the praise of the visitors correspondingly. The data acquisition system can process data acquisition and processing for related molding machines of customer’s entire plant, which set up a bridge between the molding equipment and the MES system, offering professional pre-processing of data acquisition for the MES system. After MES system processing the data it acquired in future step, it sent the data to the ERP system, which presented diverse advertisements for different users to make reasonable decisions in time. All the acquired data should be recorded as important information to provide accurate data foundation for the next process control and product improvement.
In the exhibition, we also displayed the SCIG (Shini Collective Storage System) and AGV (Automated Guided Vehicle) automation solutions. The process was after the products were packed in cartons, they were collected in the system; The AGV vehicle transported all these cartons to product area for delivery. After delivery, the vehicle moved to the material-turnover-area to pick other cartons for next storage, and then transported the cartons to product-delivery-area again with full-load system, and repeated this circulation. The SCIG system is applicable to the conveying after product’s piling up and collection. The multilayer empty carton was packed in the empty-carton-area on SCIG system, while the monolayer carton was conveyed to the product-stacking area by the conveying belt. After the products were picked out from the IMM and laid up in the cartons by Robots, the up-down server then piled up the full-load carton above another and transported other empty cartons to the product-stacking-area to repeat the circulation. Afterward, the finished cartons were conveyed to SCIG shipment area and waiting for the AGV vehicle for delivery. The AGV also named as automatic driverless cart. It is an automated guided vehicle, which can follow the required route to complete the appointed tasks according to preset course and program. For modern intelligent plant, AGV not only features reduced operator but also could withstand the heavy load.
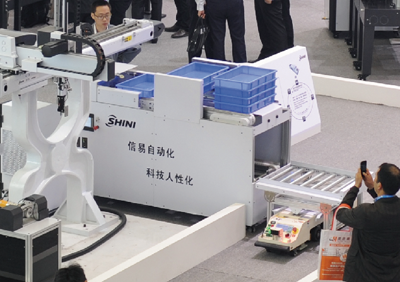
Intelligent Equipment
Large Drying and Dehumidifying System of energy saving model is equipped with intelligent control system of drying airflow, it can automatically adjust airflow according to the temperature of air exhausted from the hopper, which saves energy and prevents material over-drying. In addition, this set of equipment also outfitted with recycling device of regeneration heat, it maximum reduces the consumption power of machine and cut down the cost. This brand new design of drying hopper optimized the proportion of hopper structure, making more consistent drying time of material in the hopper, which ensures better drying effect.
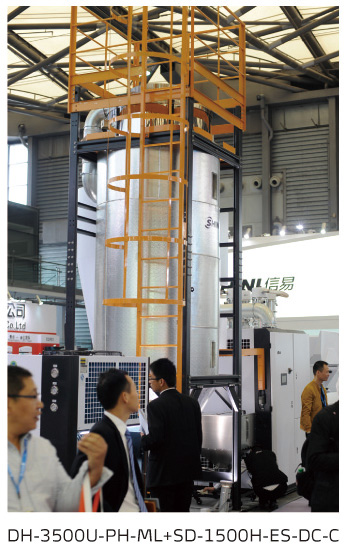
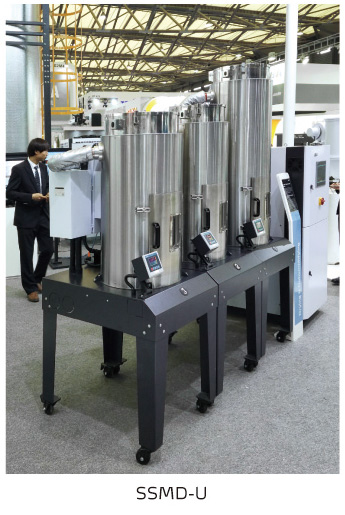
The common model of Dryer is a kind of plastic auxiliary equipment that used most frequently in the market and it is also one of the largest demands. Product technical requirement is not high, with comparatively a transparent price, it faces fierce competition. Different from the common models, Shini exhibited energy-saving dryer featuring obvious superiority, and the energy saving is the development trend that approved by the whole society, which not only benefits the people but profits the whole country. It adopts dual effective & energy-saving heater which helps save 30% energy more than the traditional heater. The energy-saving heater has self-protection function that making the machine won’t be damaged by the damage of blower and failure of contactor. It standard equipped with microcomputer control and RS485 communication function port for convenient central monitoring and data sharing.
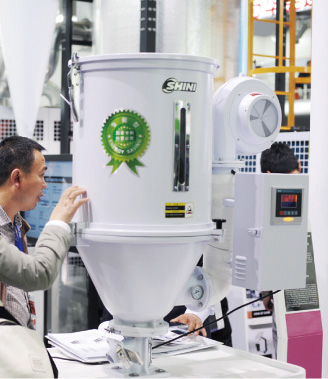
Every Chinaplas has gathered the devoted efforts of each Shini member. From the preparation till the successful ending of exhibition, from product’s data editing to the professional service for the equipment, from product’s demonstration and design to the strict requirement of the details, all above endeavors fully showed our enthusiasm to make the customer more of surprises.
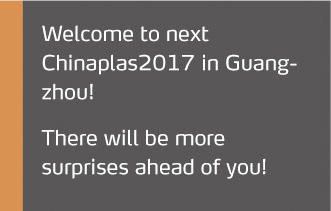
Special Reports
- sLink --Protocol Solution
- MES Intelligent Manufacturing Integrated System
- Introduction of Gram-meter Control System
- Shini Central Granulator—Regular & Budget Series
If you want to read other articles, back to2016 Quarter 3 Issue 28.