Special Reports
2016 Quarter 4 Issue 29
Film Extrusion Process and Collocation of Extrusion Equipment
Plastic film, as a kind of common plastic products can be produced by sheet/film extrusion and blown extrusion, in which the blowing process occupies a very important position in the plastic molding process. The blown film uses screw to melt and extrude the material into the thin bubble, then using the compressed air to blow the bubble when it is hot, and finally obtains the film after the cooling and solidification. The product has a wide application, and has been used in various fields and industries, such as the commodities of plastic bag, plastic wrap, agricultural film and the protective film.
Generally, the better performed film production line consists of following major sections (take the triple extrusion line as example as fig.1)
1.Material Supply System
The material supply system fulfills the material conveying from the storage location to each ingredient’s temporary storage hopper of the co-extrusion extruder, it ensured the continuous production, reduced the labor, improved the working environment and reduced the accident occurrence. The material supply system equipped with material shortage alarm to remind the operator to refill material when it is almost used up.
2.Formula Mixture System
The formula mixture system accurately and uniformly mix the material in proportion as each layer’s formula requirement, as to satisfy the extrusion formula requirement during the application. At present, it commonly uses the co-extrusion process. Take triple layer co-extrusion as example, as to achieve the film cost and performance balance, each layer of film needs different functions. Therefore, it needs accurate control of material proportion in each layer to ensure each layer’s performance reach the process and cost requirement. The formula mixture system plays an important role in this process. It usually adopts gravimetric or loss-in-weight method to precisely control each ingredient’s proportional ratio in each layer, which collocates with the mixing device that eventually ensures the mixing uniformity.
3.Screw Heating and Material Extrusion Control System
Screw heating system fulfills the plastic material heating up to the process in specified temperature range. While the extrusion control system achieves the material extrusion according to the layer thickness ratio as formula requirement.
4.Die and Heating System
The die is the collection point of each layer as well as the thickness forming points before the film cooling down. The die quality will directly affect the film thickness property.
5.Thickness Measuring and Control System
It consists of two systems, which are coexisted during the application. The thickness measuring system fulfills the real-time measuring of film thickness on line. While the control system achieves the film thickness control according to real-time thickness by adjusting the air ring or automatic die as well as other execution units.
6.The Bubble Cooling and Control System
The material needs cooling after it is extruded from the die, and the cooling method contains inner and external cooling. When using the inner cooling system, it needs precise adjustment of the inlet /outlet airflow in bubble for precise control of the film width.
7.Rotary Hauling Control System
The rotary extruding has two parts: one is the hauling and the other to the rotation. The purpose of hauling is to achieve the film longitudinal stretching, while the purpose of rotation is to achieve better rolling up.
8.The Rolling Up System
The rolling up system collects the film after actual molding.
Aiming for material supplying in film production, Shini-Syncro launched the Sylink series of machine, which could reach the capacity from 50kg/h to 5000kg/h. The formula mixture system has eaSYbatch, SYdos and Smarty series. Except for the precise proportioning, all the series of machine could also achieve the film longitudinal control (extrusion control and hauling speed control).
For the aspect of thickness measuring and control system, we provide the thickness measuring system as eaSYmex, Combyscan, Optyscan to satisfy the measuring requirements of different films, as well as the automatic air ring and die control system to control the film thickness. On the aspect of inner cooling system, we provide the SYIBC reduced diameter control system of inner cooling, which accurately controls the film width between 300mm~20000mm with efficient cooling.
We provide highly integrated control system which combines all the control systems into a central control station.
Domestic matching production line, as Fig. 2.
Production film type: PVDC food package
Layer number: 3 layers
Output: 250kg/h
Thickness: 20~150um
Width: 600~1500mm
Die size: 400mm
It collocated with SYlink supply system, eaSYbatch-S-4 loss-in-weight proportioning and thickness ratio control system, measurement and control system.
Generally, the better performed film production line consists of following major sections (take the triple extrusion line as example as fig.1)
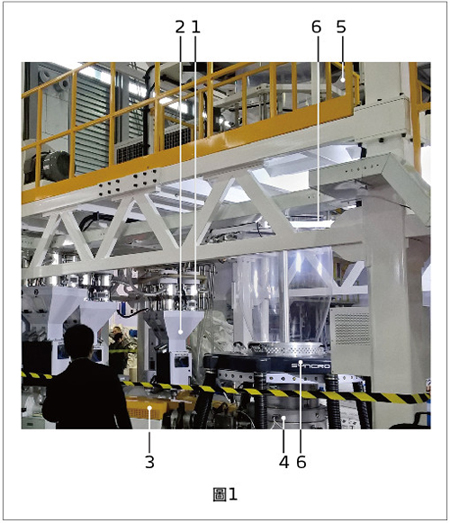
1.Material Supply System
The material supply system fulfills the material conveying from the storage location to each ingredient’s temporary storage hopper of the co-extrusion extruder, it ensured the continuous production, reduced the labor, improved the working environment and reduced the accident occurrence. The material supply system equipped with material shortage alarm to remind the operator to refill material when it is almost used up.
2.Formula Mixture System
The formula mixture system accurately and uniformly mix the material in proportion as each layer’s formula requirement, as to satisfy the extrusion formula requirement during the application. At present, it commonly uses the co-extrusion process. Take triple layer co-extrusion as example, as to achieve the film cost and performance balance, each layer of film needs different functions. Therefore, it needs accurate control of material proportion in each layer to ensure each layer’s performance reach the process and cost requirement. The formula mixture system plays an important role in this process. It usually adopts gravimetric or loss-in-weight method to precisely control each ingredient’s proportional ratio in each layer, which collocates with the mixing device that eventually ensures the mixing uniformity.
3.Screw Heating and Material Extrusion Control System
Screw heating system fulfills the plastic material heating up to the process in specified temperature range. While the extrusion control system achieves the material extrusion according to the layer thickness ratio as formula requirement.
4.Die and Heating System
The die is the collection point of each layer as well as the thickness forming points before the film cooling down. The die quality will directly affect the film thickness property.
5.Thickness Measuring and Control System
It consists of two systems, which are coexisted during the application. The thickness measuring system fulfills the real-time measuring of film thickness on line. While the control system achieves the film thickness control according to real-time thickness by adjusting the air ring or automatic die as well as other execution units.
6.The Bubble Cooling and Control System
The material needs cooling after it is extruded from the die, and the cooling method contains inner and external cooling. When using the inner cooling system, it needs precise adjustment of the inlet /outlet airflow in bubble for precise control of the film width.
7.Rotary Hauling Control System
The rotary extruding has two parts: one is the hauling and the other to the rotation. The purpose of hauling is to achieve the film longitudinal stretching, while the purpose of rotation is to achieve better rolling up.
8.The Rolling Up System
The rolling up system collects the film after actual molding.
Aiming for material supplying in film production, Shini-Syncro launched the Sylink series of machine, which could reach the capacity from 50kg/h to 5000kg/h. The formula mixture system has eaSYbatch, SYdos and Smarty series. Except for the precise proportioning, all the series of machine could also achieve the film longitudinal control (extrusion control and hauling speed control).
For the aspect of thickness measuring and control system, we provide the thickness measuring system as eaSYmex, Combyscan, Optyscan to satisfy the measuring requirements of different films, as well as the automatic air ring and die control system to control the film thickness. On the aspect of inner cooling system, we provide the SYIBC reduced diameter control system of inner cooling, which accurately controls the film width between 300mm~20000mm with efficient cooling.
We provide highly integrated control system which combines all the control systems into a central control station.
Domestic matching production line, as Fig. 2.
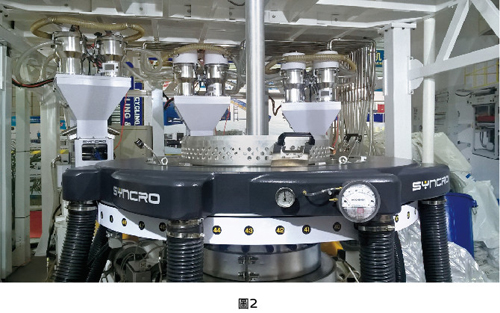
Production film type: PVDC food package
Layer number: 3 layers
Output: 250kg/h
Thickness: 20~150um
Width: 600~1500mm
Die size: 400mm
It collocated with SYlink supply system, eaSYbatch-S-4 loss-in-weight proportioning and thickness ratio control system, measurement and control system.
Special Reports
- Application of Auxiliary Equipment in MIM
- The New Technology of Shini Water Chiller
- The Selection and Application of Hot Runner System
If you want to read other articles, back to2016 Quarter 4 Issue 29.