Special Reports
2017 Quarter 1 Issue 30
Vacuum Drying Technology
Introduction of Vacuum Drying Technology
Water boiling point is proportional to atmospheric pressure which means as pressure increases, so does water boiling point and vice versa. Therefore, the atmospheric pressure on thousand-kilometer high mountains is much lower than on the sea level. And water boiling point is low on the high mountain due to the low pressure. People once made the test taking purified water as the example: the boiling point drops about 1℃ in every 300m rise of the height. So, it needn’t reach 100℃/212OF for the water to start boiling on the high mountain.
Vacuum drying just according to above phenomenon to expose the to-be-dried material in negative pressure status with lowered water boiling point. The water boiling point under normal atmospheric pressure is 100℃/212OF, while dropping to 80℃/176OF, 60℃/140OF and 40℃/104OF in negative vacuum condition, then it starts evaporating and fulfills the drying process of thermo sensitivity to materials.
Distinction between Vacuum Drying and Honeycomb Drying & Dehumidifying Technologies
Generally, as to improve the drying efficiency, it needs to equip with the heating device to heat up the material by heat transfer or thermal radiation, offering sufficient heat to materials with accelerated vaporizing speed of the vapor. In the drying process, as the to-be-dried material is always at the negative pressure status, the isolated air environment better keeps original characteristics of some materials that easily cause oxidizing and chemical reaction during the high-temp. drying process.
Relatively, the honeycomb drying and dehumidifying technology doesn’t have perfect drying effect to some heat sensitive materials that easily causing the oxidation under high-temperature baking, which finally affects product quality. The honeycomb drying and dehumidifying system requires regeneration system, creating higher energy consumption.
The vacuum drying equipment has many advantages, but it needs the vacuum system. Furthermore, it should add a vacuum motive-seal structure at the inlet/outlet for some large continuous production equipment. As this assembly of structure can easily cause leakage, it requires regular checking, resulting maintenance burdens. Though manufacturing and maintenance cost of this equipment is high, the vacuum drying process is more suitable for some materials due to its unique drying property.
Status Quo and Developmental Tendency of Vacuum Drying Technology
With the development of science technology, the drying technology and equipment have made much progress, in which the combination of vacuum and other drying method as well as heating technologies give new meaning and vitality of the vacuum drying device. As the vacuum drying technology could be fully dried in low temperature, it has been widely used in food, medicine, chemicals, biology and other manufacturing fields. The vacuum drying equipment for our plastic materials can be divided into hot-air heating and conduction heating according to material heating method. Vacuum drying equipment uses hot-air heating method though quick but will change material’s physical properties due to oxidation. Vacuum drying equipment uses conduction heating that can avoid material oxidation but is quite slow. The general tendency of vacuum drying development is innovative, energy-consumption, reduced cost with improved economical efficiency.
Shini SVD Vacuum Dryer
SVD Vacuum Dryers are newly mass-produced equipment of Drying and Dehumidifying series, assembling the drying, dehumidifying and conveying into one unit, which could achieve efficient drying and dehumidifying for plastic materials. The drying and dehumidifying principle: vacuum pump vacuumizes the drying hopper and ensures the vacuum degree is always maintained at the setting range, spreading the moisture from materials inside onto their surface under pressure difference. At the same time, the heating system continually heats the to-be-dried materials by heat transfer. After water molecule gaining sufficient heat and kinetic energy from material surface, overcoming the attraction between molecules, it dries and dehumidifies the plastic materials.
SVD Features
1.It adopts high-efficient vacuum pump to vacuumize the plastic material, then heats and dries the material by heat transfer, which saves about 50% power consumption compared with the conventional Dehumidifying Dryer of same specification.
2.The hopper body and conducting strip adopt hard aluminium-alloy design that is light, with superior heat transfer performance.
3.Insulated drying hopper design prevents heat loss, and saves energy;
4.Insulated layer of drying hopper adopts double-open design which is easy maintenance.
5.Closed conveying system can avoid damped materials due to air contacting after drying.
6.Adopt LCD touch control HMI, with direct and convenient operation.
7.Possess one-week timer and overheat protection, with user-friendly;
8.Adopt P.I.D temperature control, and the accuracy could reach ±1℃/0.18OF.
9.Adopt heat transfer for the heating that avoids material performance changing due to oxidation.
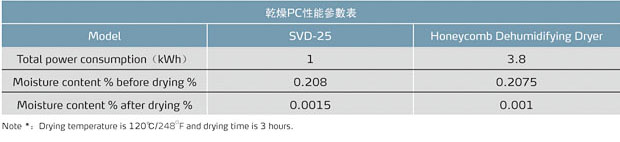
Water boiling point is proportional to atmospheric pressure which means as pressure increases, so does water boiling point and vice versa. Therefore, the atmospheric pressure on thousand-kilometer high mountains is much lower than on the sea level. And water boiling point is low on the high mountain due to the low pressure. People once made the test taking purified water as the example: the boiling point drops about 1℃ in every 300m rise of the height. So, it needn’t reach 100℃/212OF for the water to start boiling on the high mountain.
Vacuum drying just according to above phenomenon to expose the to-be-dried material in negative pressure status with lowered water boiling point. The water boiling point under normal atmospheric pressure is 100℃/212OF, while dropping to 80℃/176OF, 60℃/140OF and 40℃/104OF in negative vacuum condition, then it starts evaporating and fulfills the drying process of thermo sensitivity to materials.
Distinction between Vacuum Drying and Honeycomb Drying & Dehumidifying Technologies
Generally, as to improve the drying efficiency, it needs to equip with the heating device to heat up the material by heat transfer or thermal radiation, offering sufficient heat to materials with accelerated vaporizing speed of the vapor. In the drying process, as the to-be-dried material is always at the negative pressure status, the isolated air environment better keeps original characteristics of some materials that easily cause oxidizing and chemical reaction during the high-temp. drying process.
Relatively, the honeycomb drying and dehumidifying technology doesn’t have perfect drying effect to some heat sensitive materials that easily causing the oxidation under high-temperature baking, which finally affects product quality. The honeycomb drying and dehumidifying system requires regeneration system, creating higher energy consumption.
The vacuum drying equipment has many advantages, but it needs the vacuum system. Furthermore, it should add a vacuum motive-seal structure at the inlet/outlet for some large continuous production equipment. As this assembly of structure can easily cause leakage, it requires regular checking, resulting maintenance burdens. Though manufacturing and maintenance cost of this equipment is high, the vacuum drying process is more suitable for some materials due to its unique drying property.
Status Quo and Developmental Tendency of Vacuum Drying Technology
With the development of science technology, the drying technology and equipment have made much progress, in which the combination of vacuum and other drying method as well as heating technologies give new meaning and vitality of the vacuum drying device. As the vacuum drying technology could be fully dried in low temperature, it has been widely used in food, medicine, chemicals, biology and other manufacturing fields. The vacuum drying equipment for our plastic materials can be divided into hot-air heating and conduction heating according to material heating method. Vacuum drying equipment uses hot-air heating method though quick but will change material’s physical properties due to oxidation. Vacuum drying equipment uses conduction heating that can avoid material oxidation but is quite slow. The general tendency of vacuum drying development is innovative, energy-consumption, reduced cost with improved economical efficiency.
Shini SVD Vacuum Dryer
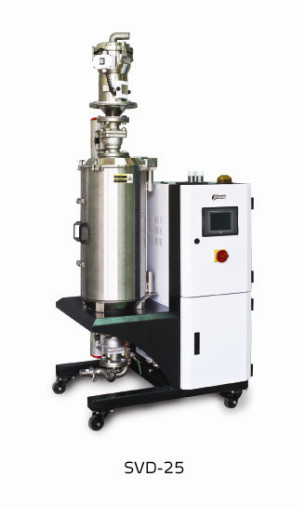
SVD Features
1.It adopts high-efficient vacuum pump to vacuumize the plastic material, then heats and dries the material by heat transfer, which saves about 50% power consumption compared with the conventional Dehumidifying Dryer of same specification.
2.The hopper body and conducting strip adopt hard aluminium-alloy design that is light, with superior heat transfer performance.
3.Insulated drying hopper design prevents heat loss, and saves energy;
4.Insulated layer of drying hopper adopts double-open design which is easy maintenance.
5.Closed conveying system can avoid damped materials due to air contacting after drying.
6.Adopt LCD touch control HMI, with direct and convenient operation.
7.Possess one-week timer and overheat protection, with user-friendly;
8.Adopt P.I.D temperature control, and the accuracy could reach ±1℃/0.18OF.
9.Adopt heat transfer for the heating that avoids material performance changing due to oxidation.
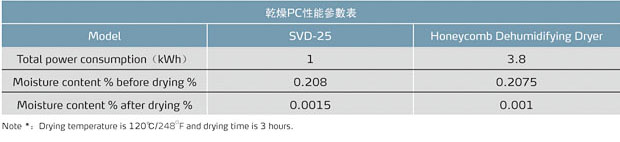
Special Reports
If you want to read other articles, back to2017 Quarter 1 Issue 30.