Experience Sharing
2017 Quarter 1 Issue 30
Case Analysis of Central Conveying System
Material central conveying system plays a more and more important role in plastic industry. It’s well-known for high efficient, energy-saving, individualization automated and modern plant images.
In this case, we analyzes one of Automotive Interior Co., Ltd in Hubei that is specialized in developing, production, selling automotive exterior, interior and engine cabin plastic parts including dashboard, door protector, bumper, spoiler and fender……
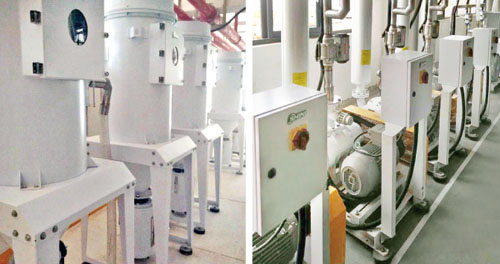
This company has 19 injection molding machines and 4 double shots: the main materials are ABS, PMMA with total dosage of 1950kg/hr requiring the drying. Materials for double shots need dehumidifying, so we equipped 23 sets of Dryers for customers.
This system adopts two-layer platforms. At right side of first-layer platform, it has 7 blowers in straight line, 4 Roots blowers (three in work and one back up), and three high-pressure blowers (two in work and one back up). According to material dosage and workshop of the customer, we selected the SRB-80-V and SCVG-75-SS, which feed the IMM in workshop and Dryer in material room respectively, dividing the Dryers into two groups —— 12 sets/group and 11 sets/group. Furthermore, the IMM is divided into three zones, which has 4 sets of double shots in a zone, 7 sets of middle IMMs in a zone and 8 sets of front IMMs in a zone.
The 4 Roots blowers and 3 high-pressure blowers all adopt stainless steel pipe in connection with pneumatic ball valves to achieve automatic switching to back-up blower during blower fails. Moreover, two of the three high-pressure blowers have covers of white silencers, with unified installation of control box right on the wall, which not only ensure the aesthetics of overall layout, but also satisfy customer’s requirement of noises.
The 24 stations of Central Control Station ——SCCS-200-G-C-10.4”, equipped with Siemens color touch screen and PLC. It’s obvious that one unit feeds the IMM in workshop, and one unit feeds the Dryer in material room. And it adopts “interlocked software” to solve material supplying problems when IMMs in different zones using one material. Two material distribution stations SMDS-6*6 equipped with 24 groups of 1-in-3-out manifold in two-layer stacking.
The second layer is similar as the first layer, which only differs in 5 central filters ——SCSF-200F-E right above. And over the storage tank, it has 19 Hopper Dryers and 4 Dehumidifying Dryers on the platform, with capacity from 100kg to 500kg in drying of different materials. In addition, there’s a square hole in length of 2.3m and width of 1.1m above material distribution station on the first layer for pipeline to reach IMM in workshop.
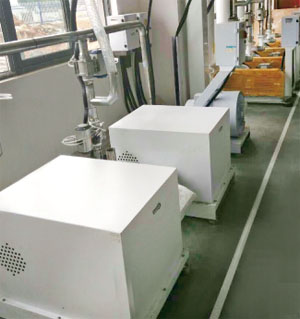
However, pipeline along the way is in 4 layers. Some have 5 layers of supports and some are tensioned to ceiling with fixation directly or by pull rod, or fixed by joist steel. The whole welding process protects the integrity of workshop, prevents mutual effect of whole pipeline and water pipe and air pipe on site, which obtains excellent layout and customer’s recognition.
Since delivery of this system, its good performance largely improved production efficiency and products’ quality, which has been well-received by the customer.
In this case, we analyzes one of Automotive Interior Co., Ltd in Hubei that is specialized in developing, production, selling automotive exterior, interior and engine cabin plastic parts including dashboard, door protector, bumper, spoiler and fender……
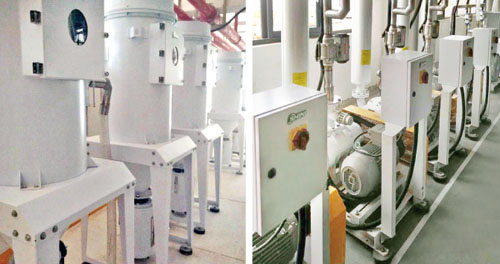

The 4 Roots blowers and 3 high-pressure blowers all adopt stainless steel pipe in connection with pneumatic ball valves to achieve automatic switching to back-up blower during blower fails. Moreover, two of the three high-pressure blowers have covers of white silencers, with unified installation of control box right on the wall, which not only ensure the aesthetics of overall layout, but also satisfy customer’s requirement of noises.
The 24 stations of Central Control Station ——SCCS-200-G-C-10.4”, equipped with Siemens color touch screen and PLC. It’s obvious that one unit feeds the IMM in workshop, and one unit feeds the Dryer in material room. And it adopts “interlocked software” to solve material supplying problems when IMMs in different zones using one material. Two material distribution stations SMDS-6*6 equipped with 24 groups of 1-in-3-out manifold in two-layer stacking.
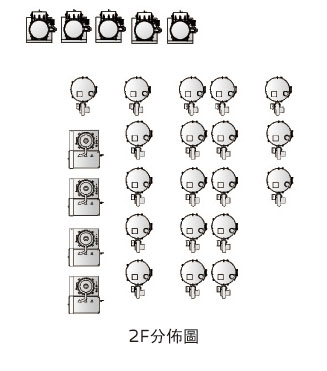
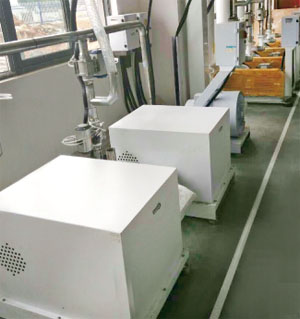
Since delivery of this system, its good performance largely improved production efficiency and products’ quality, which has been well-received by the customer.
Experience Sharing
- Gravimetric Blender SGB Applied in Spinning Industry
- Small Central Conveying System Used in Auto Parts Industry
- SHINI ST5 Robot Application
If you want to read other articles, back to2017 Quarter 1 Issue 30.