Experience Sharing
2013 Quarter 4 Issue 17
The Case of Large-scale System of Dehumidifying and Drying Combined with Central Feeding System
Clients Profile
A pipe manufacture corporation in a large industrial zone of Wuhan in Hubei is a new high tech enterprise mainly developing, producing, and marketing plastic pipe. It is invested and jointly controlled by a huge state-owned enterprise and a pipe industry company in Guizhou.
This corporation uses polyolefin as main materials. Its main business products are environmental friendly municipal pipelines, like pipelines for city water supply, water draining, fuel gas and construction, and special industrial pipelines for electricity supply, communication, chemical industry, motor vehicle and coal mine. Since it’s a corporation with mature technology, this corporation, built in 2012, introduces central feeding system used with large-scale system of dehumidifying and drying to replace manual feeding or semi-auto feeding.
Technical Parameters
•Raw material type: Polyolefin
•Raw material handling: Materials for producing gas pipes need to be dehumidified and dried and materials for producing other kinds of pipes just need to be dried by hot air. Drying time is 2-3hr.
•Machines: 9 extrusion lines of which the max extrusion output is 1500kg/hr and the minimum extrusion output is 350kg/hr.
Project Description
This system consists of a large-scale system of dehumidifying and drying and central feeding system.
Dehumidifying and drying system: There are 4 extrusion lines for producing gas pipes. Each extrusion line is equipped with large-scale dehumidifying and drying system. Each consists of two-stage drying: First stage, materials are dried with hot air dryer without dehumidifying. After material is dried, it is conveyed to second stage for further dehumidified and dried before it is conveyed to extrusion lines. There are also another 5 extrusion lines for producing pipes with solid walls. These 5 lines are equipped with large dryers. Two of them are equipped with two-stage drying, since their extrusion outputs are quite large.
Feeding system: Extrusion lines are designed for making large diameter pipes. Down time is not allowed during production. Platforms are made above the extrusion lines. On the platforms, there are material storage tanks. Materials in tanks can automatically fall off to material inlets of extrusion lines. All the materials are sent to the material storage tanks on each line after being dehumidified and dried. There are 5 blowers for the 9 extrusion lines. Two blowers are respectively used together with two extrusion lines whose extrusion outputs are quite large. All the blowers are roots blower of high air pressure and large air flow, which can ensure material conveying speed and meet the extruder’s requirement of materials quantity. Shut off valves are installed under dryers to ensure no blockage during material conveying. Each extrusion line has one material pipe of stainless steel which is placed along the platform and upright of workshop in 2.5-3m high. The central feeding system of the 9 extrusion lines adopt one “1-to-12”control station to control.
This system is completed in April and has been used since that time. Until now, it works well and realizes the initial target of greatly reducing labor cost and increasing production efficiency. All equipments, including dehumidifying pipes as well as air and material feeding pipes are made of stainless steel, which greatly makes the workshop look nice and clean. With centralized dehumidifying and drying as well as centralized conveying, it can make the working environment more comfortable to meet the clients’ requirements by lowering the temperature of extrusion workshop (which can reduce energy consumption of central air-conditioner) and reducing dust inside extrusion workshop, which gets good reputation from clients.
A pipe manufacture corporation in a large industrial zone of Wuhan in Hubei is a new high tech enterprise mainly developing, producing, and marketing plastic pipe. It is invested and jointly controlled by a huge state-owned enterprise and a pipe industry company in Guizhou.
This corporation uses polyolefin as main materials. Its main business products are environmental friendly municipal pipelines, like pipelines for city water supply, water draining, fuel gas and construction, and special industrial pipelines for electricity supply, communication, chemical industry, motor vehicle and coal mine. Since it’s a corporation with mature technology, this corporation, built in 2012, introduces central feeding system used with large-scale system of dehumidifying and drying to replace manual feeding or semi-auto feeding.
Technical Parameters
•Raw material type: Polyolefin
•Raw material handling: Materials for producing gas pipes need to be dehumidified and dried and materials for producing other kinds of pipes just need to be dried by hot air. Drying time is 2-3hr.
•Machines: 9 extrusion lines of which the max extrusion output is 1500kg/hr and the minimum extrusion output is 350kg/hr.
Project Description
This system consists of a large-scale system of dehumidifying and drying and central feeding system.
Dehumidifying and drying system: There are 4 extrusion lines for producing gas pipes. Each extrusion line is equipped with large-scale dehumidifying and drying system. Each consists of two-stage drying: First stage, materials are dried with hot air dryer without dehumidifying. After material is dried, it is conveyed to second stage for further dehumidified and dried before it is conveyed to extrusion lines. There are also another 5 extrusion lines for producing pipes with solid walls. These 5 lines are equipped with large dryers. Two of them are equipped with two-stage drying, since their extrusion outputs are quite large.
Feeding system: Extrusion lines are designed for making large diameter pipes. Down time is not allowed during production. Platforms are made above the extrusion lines. On the platforms, there are material storage tanks. Materials in tanks can automatically fall off to material inlets of extrusion lines. All the materials are sent to the material storage tanks on each line after being dehumidified and dried. There are 5 blowers for the 9 extrusion lines. Two blowers are respectively used together with two extrusion lines whose extrusion outputs are quite large. All the blowers are roots blower of high air pressure and large air flow, which can ensure material conveying speed and meet the extruder’s requirement of materials quantity. Shut off valves are installed under dryers to ensure no blockage during material conveying. Each extrusion line has one material pipe of stainless steel which is placed along the platform and upright of workshop in 2.5-3m high. The central feeding system of the 9 extrusion lines adopt one “1-to-12”control station to control.
This system is completed in April and has been used since that time. Until now, it works well and realizes the initial target of greatly reducing labor cost and increasing production efficiency. All equipments, including dehumidifying pipes as well as air and material feeding pipes are made of stainless steel, which greatly makes the workshop look nice and clean. With centralized dehumidifying and drying as well as centralized conveying, it can make the working environment more comfortable to meet the clients’ requirements by lowering the temperature of extrusion workshop (which can reduce energy consumption of central air-conditioner) and reducing dust inside extrusion workshop, which gets good reputation from clients.
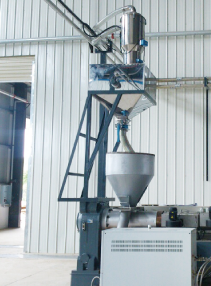
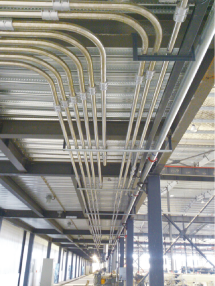
Experience Sharing
If you want to read other articles, back to2013 Quarter 4 Issue 17.