Special Reports
2014 Quarter 2 Issue 19
The Application of Liquid Master Batch
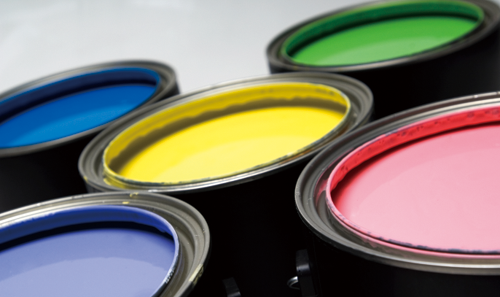
Liquid master batch is a colorant dedicated to a new type of molecular material. It’s made by three ingredients which are pigments or dyes, carriers and additives. It’s an aggregation which is made by evenly attaching over-volume pigments or dyes to the resin. As for application, most plastic processing enterprises adopt master batch particles for coloring when producing products of films, pipes, section bars and filaments. Now what we mainly talk about are liquid master batch and its advantages over master batch particles in application.
Liquid master batch is plastic master batch which takes organic liquid as a carrier and well disperses micro pigments of minimum diameters into the carrier. It’s mainly applied to films, pipes, profiles and filaments for coloring. Compared with master batch particles, liquid master batch have incomparable advantages over other ways of coloring in film extrusion and wire-drawing of fiber, since it can effectively eliminate color points and spots on the surface of the products.
With liquid as carrier, liquid master batch has more pigment content than master batch particles in the same unit weight. The add ratio is greatly reduced(For color products, the add ratio of the liquid master batch usually is within 0.6~2.0% while for transparent parts is only within 0.2~0.5%). Thus it greatly reduces cost of coloring. What’s more, liquid is all-pervasive. Therefore, liquid master batch has remarkable dispersing effect. It has higher intensity of coloring and covering. The products made from it are of better glossiness. Furthermore, the organic liquid is completely compatible with plastic materials, which not only makes no harm for the plastics but also improves some processing techniques of plastics in actual application, like reducing the processing temperature, increasing mobility, and so on, and thus enhances some physical properties of the plastics.
It’s liquid and the organic liquid is completely compatible with the plastic material. Consequently, besides pigments, many additives of different functions (such as opening slip agent, anti-static agent, transparent agent, weather resistant agent, antioxidant, release agent and blowing agent.) can be added properly according to customer requirements, which makes the liquid master batch be capable of coloring the plastic products as well as have all kinds of functions.
Liquid master batch is of better metering precision. Besides, peristaltic pump which is of easy operation and auto production, it requires no worker for metering and mixing, which costs less working hours and reduce production cost of coloring plastic products. Unlike the traditional way of coloring which brings quite a lot of pressure on overall cost for manufacturers, the new type of liquid master batch greatly reduces overall cost.
1.Reduce deviations which may occur during the production process. Since the whole production process basically is complete automation and simplification, it only requires technician to adjust and start it. Thus, it greatly improves the production efficiency.
2.It requires no mixing equipment, which helps save space and energy.
Since it’s directly conveyed to the feeding port after metering, it requires no mixing equipment and thus saves space and energy the equipment costs.
3. Reduce color changing time and material loss. The design principle of peristaltic pump brings no material contamination to the pump head during operation. Besides, it only needs to change the flexible pipe to finish color changing, and thus saves time and staff for cleaning devices, like mixing tank and hopper, etc, which the traditional color material requires. The properties of liquid master batch decide that there is little pigment left with the screw and barrel, which brings easy cleaning and greatly reduces time and material for cleaning the machine. Depending on the size of the machine, the color changing process just requires several minutes to half an hour. However, However, for the traditional materials, the process takes 1~3 hours. Therefore, the liquid master batch can largely reduce down time and improve production efficiency.
As mentioned above, the liquid master batch brings simple processing conditions, easy operation, clean coloring, uniform & stable color, high qualified products rate and economic benefit. Therefore, the liquid master batch will be more widely applied to coloring in the future.
Liquid master batch is plastic master batch which takes organic liquid as a carrier and well disperses micro pigments of minimum diameters into the carrier. It’s mainly applied to films, pipes, profiles and filaments for coloring. Compared with master batch particles, liquid master batch have incomparable advantages over other ways of coloring in film extrusion and wire-drawing of fiber, since it can effectively eliminate color points and spots on the surface of the products.
With liquid as carrier, liquid master batch has more pigment content than master batch particles in the same unit weight. The add ratio is greatly reduced(For color products, the add ratio of the liquid master batch usually is within 0.6~2.0% while for transparent parts is only within 0.2~0.5%). Thus it greatly reduces cost of coloring. What’s more, liquid is all-pervasive. Therefore, liquid master batch has remarkable dispersing effect. It has higher intensity of coloring and covering. The products made from it are of better glossiness. Furthermore, the organic liquid is completely compatible with plastic materials, which not only makes no harm for the plastics but also improves some processing techniques of plastics in actual application, like reducing the processing temperature, increasing mobility, and so on, and thus enhances some physical properties of the plastics.
It’s liquid and the organic liquid is completely compatible with the plastic material. Consequently, besides pigments, many additives of different functions (such as opening slip agent, anti-static agent, transparent agent, weather resistant agent, antioxidant, release agent and blowing agent.) can be added properly according to customer requirements, which makes the liquid master batch be capable of coloring the plastic products as well as have all kinds of functions.
Liquid master batch is of better metering precision. Besides, peristaltic pump which is of easy operation and auto production, it requires no worker for metering and mixing, which costs less working hours and reduce production cost of coloring plastic products. Unlike the traditional way of coloring which brings quite a lot of pressure on overall cost for manufacturers, the new type of liquid master batch greatly reduces overall cost.
1.Reduce deviations which may occur during the production process. Since the whole production process basically is complete automation and simplification, it only requires technician to adjust and start it. Thus, it greatly improves the production efficiency.
2.It requires no mixing equipment, which helps save space and energy.
Since it’s directly conveyed to the feeding port after metering, it requires no mixing equipment and thus saves space and energy the equipment costs.
3. Reduce color changing time and material loss. The design principle of peristaltic pump brings no material contamination to the pump head during operation. Besides, it only needs to change the flexible pipe to finish color changing, and thus saves time and staff for cleaning devices, like mixing tank and hopper, etc, which the traditional color material requires. The properties of liquid master batch decide that there is little pigment left with the screw and barrel, which brings easy cleaning and greatly reduces time and material for cleaning the machine. Depending on the size of the machine, the color changing process just requires several minutes to half an hour. However, However, for the traditional materials, the process takes 1~3 hours. Therefore, the liquid master batch can largely reduce down time and improve production efficiency.
As mentioned above, the liquid master batch brings simple processing conditions, easy operation, clean coloring, uniform & stable color, high qualified products rate and economic benefit. Therefore, the liquid master batch will be more widely applied to coloring in the future.
Special Reports
If you want to read other articles, back to2014 Quarter 2 Issue 19.