Special Reports
2014 Quarter 2 Issue 19
Vacuum Drying Technology
Brief Introduction of Vacuum Drying Technology
The boiling point of water is proportional to the atmospheric pressure. That’s to say the boiling point of water will go up if the atmospheric pressure goes down and goes down if the atmospheric pressure decreases. The atmospheric pressure on the mountains which are of several thousand meters above sea level is much lower than the one at sea level. Therefore, the boiling point of water is low. It has been tested that the altitude increases by 300m, the boiling point of water will decrease about 1℃. Therefore, water boiling temperature is less than 100℃ on the high mountain.
Vacuum drying is based on the phenomenon mentioned above. It means put the material which needs to be drying under vacuum and negative pressure condition to lower the water boiling point. The water boiling point under normal atmospheric pressure is 100℃, However, it can lower to 80℃, 60℃ and 40℃ under vacuum and negative pressure condition. Then the water will start to evaporate, which enables drying heat sensitive material.
The Difference between the Vacuum Drying Technology and Rotor Dehumidifying & Drying Technology
Generally speaking, vacuum drying requires heating device to heat the material which needs to be dried by heat conduction or heat radiation to improve drying rate, and thus to offer enough heat for the water in the material, which will speed up evaporation. During drying process, the material which needs to be dried is always in the vacuum environment which helps some easy to be oxidized material during the high temperature drying process to maintain original properties better.
The honeycomb rotor dehumidifying & drying technology has a negative drying effect on some heat sensitive material. Sensitive material oxidized under the baking of high temperature air, which will harm the quality of finished products. Besides, the honeycomb rotor dehumidifying & drying system requires a regeneration system, which results high energy consumption.
Though the vacuum drying device has many advantages, it requires dryer to be equipped with vacuum system. What’s more, it also requires mounting a vacuum seal structure for the driving parts at the inlet and outlet of the large-scale continuous production equipment. However, such a structure brings some trouble to the users, since it’s easy for leakage to occur to it and requires regular maintenance. What’s worse, vacuum drying device is of high manufacturing cost and operating cost. But it’s still necessary to employ vacuum drying technology for some material because of the special drying property it possesses.
SVD Vacuum Dryer
The dehumidifying & drying device SVD vacuum dryer which Shini mass produces features All-in-one functions. They are dehumidifying, drying and conveying. It can effectively dehumidify and dry plastic material. The way it uses to dehumidify and dry is to vacuumize the drying hopper with the vacuum pump and maintain the vacuum pressure inside the drying hopper within the required range. Then the moisture inside the material will spread to the surface of the material. At the same time, the heating system keeps heating the material via. heat conduction, which gives enough heat and energy to the moisture on the surface of the material to overcome the mutual attraction among molecules. Then the moisture will be pumped out by the vacuum pump and thus to realize the dehumidifying and drying for the plastic material.
Reference Table for Actual Drying Performance & Power Consumption
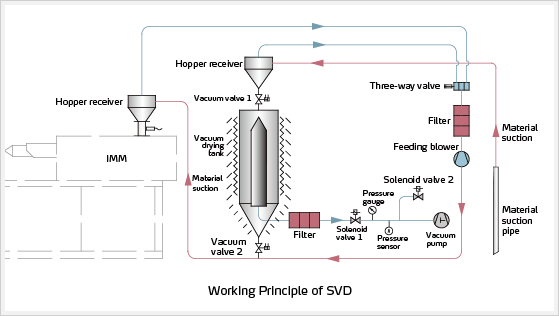
The boiling point of water is proportional to the atmospheric pressure. That’s to say the boiling point of water will go up if the atmospheric pressure goes down and goes down if the atmospheric pressure decreases. The atmospheric pressure on the mountains which are of several thousand meters above sea level is much lower than the one at sea level. Therefore, the boiling point of water is low. It has been tested that the altitude increases by 300m, the boiling point of water will decrease about 1℃. Therefore, water boiling temperature is less than 100℃ on the high mountain.
Vacuum drying is based on the phenomenon mentioned above. It means put the material which needs to be drying under vacuum and negative pressure condition to lower the water boiling point. The water boiling point under normal atmospheric pressure is 100℃, However, it can lower to 80℃, 60℃ and 40℃ under vacuum and negative pressure condition. Then the water will start to evaporate, which enables drying heat sensitive material.
The Difference between the Vacuum Drying Technology and Rotor Dehumidifying & Drying Technology
Generally speaking, vacuum drying requires heating device to heat the material which needs to be dried by heat conduction or heat radiation to improve drying rate, and thus to offer enough heat for the water in the material, which will speed up evaporation. During drying process, the material which needs to be dried is always in the vacuum environment which helps some easy to be oxidized material during the high temperature drying process to maintain original properties better.
The honeycomb rotor dehumidifying & drying technology has a negative drying effect on some heat sensitive material. Sensitive material oxidized under the baking of high temperature air, which will harm the quality of finished products. Besides, the honeycomb rotor dehumidifying & drying system requires a regeneration system, which results high energy consumption.
Though the vacuum drying device has many advantages, it requires dryer to be equipped with vacuum system. What’s more, it also requires mounting a vacuum seal structure for the driving parts at the inlet and outlet of the large-scale continuous production equipment. However, such a structure brings some trouble to the users, since it’s easy for leakage to occur to it and requires regular maintenance. What’s worse, vacuum drying device is of high manufacturing cost and operating cost. But it’s still necessary to employ vacuum drying technology for some material because of the special drying property it possesses.
SVD Vacuum Dryer
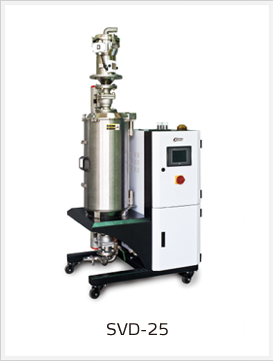
The dehumidifying & drying device SVD vacuum dryer which Shini mass produces features All-in-one functions. They are dehumidifying, drying and conveying. It can effectively dehumidify and dry plastic material. The way it uses to dehumidify and dry is to vacuumize the drying hopper with the vacuum pump and maintain the vacuum pressure inside the drying hopper within the required range. Then the moisture inside the material will spread to the surface of the material. At the same time, the heating system keeps heating the material via. heat conduction, which gives enough heat and energy to the moisture on the surface of the material to overcome the mutual attraction among molecules. Then the moisture will be pumped out by the vacuum pump and thus to realize the dehumidifying and drying for the plastic material.
Reference Table for Actual Drying Performance & Power Consumption
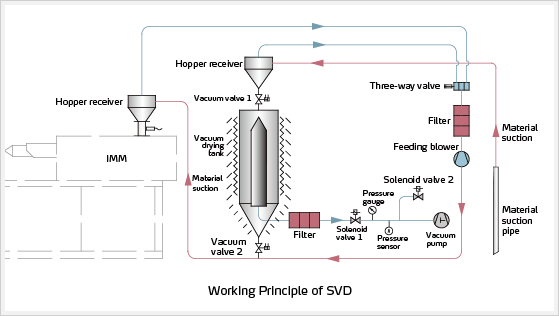
Reference Table for Actual Drying Performance & Power Consumption
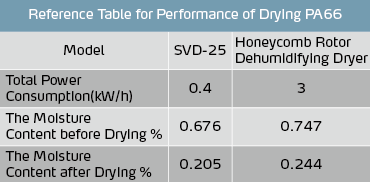
Notes*: The drying temperature is 75℃ and the time for drying is 6 hours.
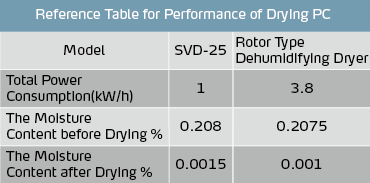
Notes*: The drying temperature is 120℃ and the time for drying is 3 hours.
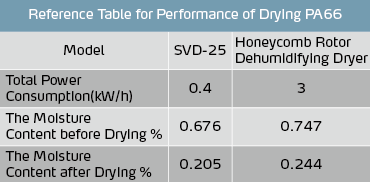
Notes*: The drying temperature is 75℃ and the time for drying is 6 hours.
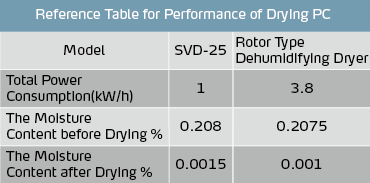
Notes*: The drying temperature is 120℃ and the time for drying is 3 hours.
The above two forms tell that the vacuum drying is more energy-saving than the traditional honeycomb dehumidifier for achieving the same drying effect.
Special Reports
If you want to read other articles, back to2014 Quarter 2 Issue 19.