Experience Sharing
2014 Quarter 3 Issue 20
Integration Case of Shini Central Material Handling System
Client Information
The company locates in a large industrial district in Guizhou. It’s a high-tech enterprise mainly managing in development, manufacture and marketing of plastic pipes. It’s invested by an state owned enterprise and a pipe industry company in Guizhou. Taking polyolefin as its main material, its main products are environmental protection municipal pipelines for water supplying, water drainage, gas and building, etc., and industry pipelines for electric power, communication, chemical industry, cars and coal mine, etc. Its branch company in Wuhan has had a set of system put into use, which brings good influence, like high efficiency and low cost. Therefore, it decides to introduce Shini central feeding system and dehumidifying drying system to replace the traditional single machine and manual feeding.
Technical Parameters
•Material type: Polyolefin (new material)
•Material processing: It requires dehumidifying and drying to manufacture gas pipeline; however, it just requires drying for manufacturing other pipelines. The drying time is 2-3hr.
•Machine: There are 11 extrusion production lines (One of them is reserved.). The largest consumption of extrusion line is 1000kg/hr while the one of the minimum extrusion line is 2-3hr.
•Power supply: The power supply for the user is 3Ф/380V/50Hz and the voltage is 24V DC.
Planning Statement
The system consists of dehumidifying drying system and central feeding system.
Dehumidifying drying system: Materials for manufacturing gas pipes require dehumidifying and drying to ensure product quality and safe use. There are 2 extrusion lines for manufacturing gas pipes. Both of them are equipped with large-scale dehumidifying drying system. The other 9 extrusion lines are for manufacturing solid pipes. All of them are equipped with large-scale dryers. Materials will be directly conveyed to the extrusion lines after being dried.
Feeding system: The pipes the company produces are of large size. Considering that the material throughput is large and the production of pipes requires no running out of material, the system is equipped with the roots blower which is of high pressure & large air volume to ensure the conveying speed of the materials and meet the requirement of the extruder toward the material quantity. There is a shut-off valve under the dryer to ensure no material blockage. Each extrusion line has one material pipe. In addition, the stainless steel pipes are laid along the uprights. The laying height is 4.8m. The central feeding system of the 9 extrusion lines adopts a 1-to12 control station to control.
The system was completed in March and has been putting into use. So far, it’s running well and realizes the initial planning aim which is to greatly reduce the labor cost and improve the production efficiency. With central dehumidifying & drying and central conveying, it lowers the temperature in the workshop (reduces the energy consumption of the central air conditioner) and reduces dust in the workshop, which makes the working environment more comfortable and meet the client’s requirements.
For extrusion lines of large material consumption, each line will consume dozens of tons of materials. Consequently, the workload for workers is getting harder and harder. The labor cost is extremely high. The labor cost for manual feeding becomes an issue which the enterprise must deal with. Therefore, it has become a trend to adopt the integration of large dehumidifying drying system and central feeding system for such an extrusion lines.
The company locates in a large industrial district in Guizhou. It’s a high-tech enterprise mainly managing in development, manufacture and marketing of plastic pipes. It’s invested by an state owned enterprise and a pipe industry company in Guizhou. Taking polyolefin as its main material, its main products are environmental protection municipal pipelines for water supplying, water drainage, gas and building, etc., and industry pipelines for electric power, communication, chemical industry, cars and coal mine, etc. Its branch company in Wuhan has had a set of system put into use, which brings good influence, like high efficiency and low cost. Therefore, it decides to introduce Shini central feeding system and dehumidifying drying system to replace the traditional single machine and manual feeding.
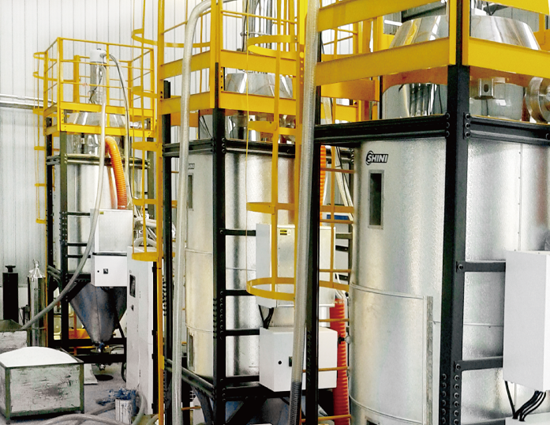
Technical Parameters
•Material type: Polyolefin (new material)
•Material processing: It requires dehumidifying and drying to manufacture gas pipeline; however, it just requires drying for manufacturing other pipelines. The drying time is 2-3hr.
•Machine: There are 11 extrusion production lines (One of them is reserved.). The largest consumption of extrusion line is 1000kg/hr while the one of the minimum extrusion line is 2-3hr.
•Power supply: The power supply for the user is 3Ф/380V/50Hz and the voltage is 24V DC.
Planning Statement
The system consists of dehumidifying drying system and central feeding system.
Dehumidifying drying system: Materials for manufacturing gas pipes require dehumidifying and drying to ensure product quality and safe use. There are 2 extrusion lines for manufacturing gas pipes. Both of them are equipped with large-scale dehumidifying drying system. The other 9 extrusion lines are for manufacturing solid pipes. All of them are equipped with large-scale dryers. Materials will be directly conveyed to the extrusion lines after being dried.
Feeding system: The pipes the company produces are of large size. Considering that the material throughput is large and the production of pipes requires no running out of material, the system is equipped with the roots blower which is of high pressure & large air volume to ensure the conveying speed of the materials and meet the requirement of the extruder toward the material quantity. There is a shut-off valve under the dryer to ensure no material blockage. Each extrusion line has one material pipe. In addition, the stainless steel pipes are laid along the uprights. The laying height is 4.8m. The central feeding system of the 9 extrusion lines adopts a 1-to12 control station to control.
The system was completed in March and has been putting into use. So far, it’s running well and realizes the initial planning aim which is to greatly reduce the labor cost and improve the production efficiency. With central dehumidifying & drying and central conveying, it lowers the temperature in the workshop (reduces the energy consumption of the central air conditioner) and reduces dust in the workshop, which makes the working environment more comfortable and meet the client’s requirements.
For extrusion lines of large material consumption, each line will consume dozens of tons of materials. Consequently, the workload for workers is getting harder and harder. The labor cost is extremely high. The labor cost for manual feeding becomes an issue which the enterprise must deal with. Therefore, it has become a trend to adopt the integration of large dehumidifying drying system and central feeding system for such an extrusion lines.
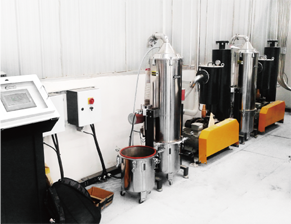
Experience Sharing
If you want to read other articles, back to2014 Quarter 3 Issue 20.