Experience Sharing
2014 Quarter 3 Issue 20
Application Case of Shini Central Conveying System
Today, China is the coantry of largest automobile production and sales in the world. It’s a great opportunity for related auto ancillary products manufacturers. Meanwhile, it’s also the challenge. The quantity of order keeps increasing along with the expansion of automobile production. The auto parts enterprise needs to ensure not only the product quantity but also the product quality. The central feeding system plays an important role in this aspect. The following case will be the best to prove it.
The molding technology co., LTD in Shenyang (a city in Liaoning Province) mainly specializes in developing and manufacturing of auto parts, plastic products, mold, paint spraying, machine manufacture and high-tech products of mold. So far, an investment of 250 million has been put into the first issue of the automobile bumper project. It produces 30,000 sets of automobile bumpers every year and reserves production ability of 50,000 sets. The investment for the second issue is about 100 million. The project is for manufacturing automotive interior plastic parts. It produces 10,000-15,000 pieces of automotive interior plastic parts every year. The company is one of the biggest suppliers of automotive interior plastic parts. Its main clients are BMW, GM, Huachen Jinbei and Benz.
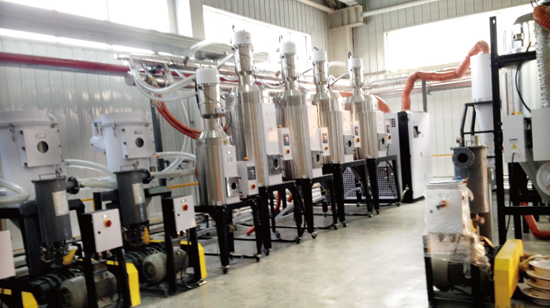
This system involves 10 injection molding machines which require dehumidifying and drying for material to ensure product quality. The feeding area has two floors. The dehumidifying drying system is on the upper floor while the storage hoppers are in the rooms on the bottom floor, which prevents the workshop from dust contamination. The material is conveyed to the dryer on the first floor via vacuum which is made by the blower. The material can be changed at random according to the material situation of the machine via the central material distribution station. One kind of material can serve for 3 injection molding machines at most. There are 4 injection molding machines equipped with volumetric dosers in the injection molding area. There are heat preservation tanks on the injection molding machines to prevent the material from being dampened again. Parts of material with glass fiber put forward requirements toward the pipelines of the whole system. The bend parts adopt glass bends while the straight parts are of stainless steel SUS 304 which is 2mm thick.
The advantage of this system lies in saving space: The dry area is relatively concentrated after setting up the steel platform, which can avoid stacking of a lot of materials and thus increase space between machines. As for working environment: With central storage & stacking of material and central dust collection which are far away from the molding production field, it greatly improves the working conditions around the main machine and reduces the dust contamination to improve the product quality. As for standard operation: Since there are material numbers for all material hoppers, it can effectively avoid mistakes for selecting material by setting the number of the material pipe and controller group.
The molding technology co., LTD in Shenyang (a city in Liaoning Province) mainly specializes in developing and manufacturing of auto parts, plastic products, mold, paint spraying, machine manufacture and high-tech products of mold. So far, an investment of 250 million has been put into the first issue of the automobile bumper project. It produces 30,000 sets of automobile bumpers every year and reserves production ability of 50,000 sets. The investment for the second issue is about 100 million. The project is for manufacturing automotive interior plastic parts. It produces 10,000-15,000 pieces of automotive interior plastic parts every year. The company is one of the biggest suppliers of automotive interior plastic parts. Its main clients are BMW, GM, Huachen Jinbei and Benz.
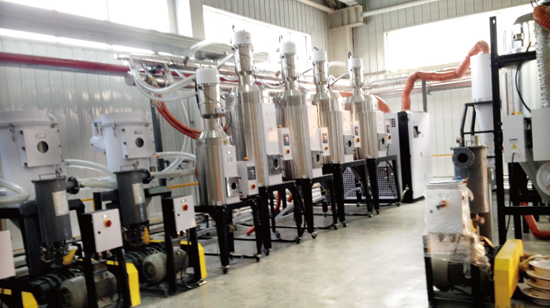
This system involves 10 injection molding machines which require dehumidifying and drying for material to ensure product quality. The feeding area has two floors. The dehumidifying drying system is on the upper floor while the storage hoppers are in the rooms on the bottom floor, which prevents the workshop from dust contamination. The material is conveyed to the dryer on the first floor via vacuum which is made by the blower. The material can be changed at random according to the material situation of the machine via the central material distribution station. One kind of material can serve for 3 injection molding machines at most. There are 4 injection molding machines equipped with volumetric dosers in the injection molding area. There are heat preservation tanks on the injection molding machines to prevent the material from being dampened again. Parts of material with glass fiber put forward requirements toward the pipelines of the whole system. The bend parts adopt glass bends while the straight parts are of stainless steel SUS 304 which is 2mm thick.
The advantage of this system lies in saving space: The dry area is relatively concentrated after setting up the steel platform, which can avoid stacking of a lot of materials and thus increase space between machines. As for working environment: With central storage & stacking of material and central dust collection which are far away from the molding production field, it greatly improves the working conditions around the main machine and reduces the dust contamination to improve the product quality. As for standard operation: Since there are material numbers for all material hoppers, it can effectively avoid mistakes for selecting material by setting the number of the material pipe and controller group.
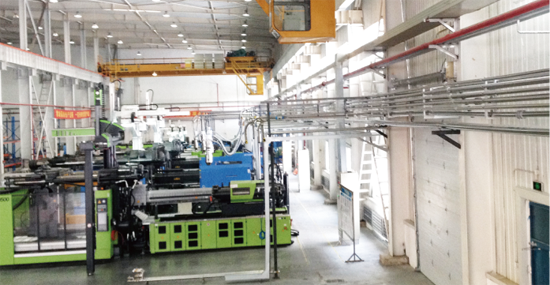
Experience Sharing
If you want to read other articles, back to2014 Quarter 3 Issue 20.