Experience Sharing
2016 Quarter 4 Issue 29
Shini Modular Dryer Used in Pelletizing Industry
The plastic pelletizing is to make various shape and size plastics into uniform to be convenient particles for later processing after melting, extruding, granulating processes. There are three types of plastic pelletizing applications, firstly, the plastic modification processing, by mixing the plastic material, additive, modifier and various functional additives together with modification for pelletizing, as to obtain the modified plastic particles in particular property. Secondly, the plastics recycling, it re-pelletizes the recycled waste plastic products after isolating, cleaning and shredding. Thirdly, the extruder pelletizing, as the polymer maybe in solution and powder state after production, it requires pelletizing for convenient post processing.
A high-tech limited company in Guangdong is engaged in R&D, production and sales of the high performance modified plastics, which is the new technology key enterprise of national torch plan. Their major products include flame-retarded resin, reinforced and toughened resin, plastic alloy and functional masterbatch four series. It is the largest domestic modified plastics manufacturer with most complete range of product series. As the product is the extruding modified plastics, it requires the Drying and Dehumidifying System to obtain a certain degree of dryness before delivery. Therefore we recommended Shini Modular Dryer according to the actual demands, which can be flexibly customized to satisfy different applications. The company purchased Shini large Modular Dryer since 2013, including the Dryer, Honeycomb Dehumidifier, cyclone dust collector, oil filter and auto loader. Because of customers’ special demands, most of the systems are customized.
The special design of dying hopper DH-U ensures enough space between the hopper outlet and floor as to place the container bag or storage tank, it’s convenient for the customer to pack the modified materials. All hoppers contact surfaces with material are made of stainless steel to ensure no contamination. The down-blowing design evenly disperses the hot air to maintain the plastic drying and uniform temperature, with improved drying efficiency. Double-layer insulation reduces heat loss. It equipped with the safety ladder and guide rail for convenient equipment repair and maintenance. The pneumatic butterfly valve mounted at the discharge port to control material discharging is convenient for material discharging after being dried. The ladders are equipped both inside and outside the hopper for easy hopper cleaning.
The Honeycomb Dehumidifier is mainly used to collocate with the Dryer to dehumidify the high hygroscopic engineering plastics that could obtain -40℃/-40℉ below dew-point of the drying air, with maximum drying airflow up to 4,000m3/hr. Adopting the full molecular sieve honeycomb for dehumidifying to achieve better effectiveness compared with the silica gel honeycomb. P.I.D temperature control technology precisely controls the regenerative temperature to ensure full regeneration for low dew-point of drying air. The double-cooler design ensures lower return air temperature and dew-point. The built-in filter ensures material free of dust contamination.
The dehumidifying pipes are made of stainless steel, which possess small wind resistance, good sealing property and strength with decent pipe layout and durability. It mounts the cyclone dust separator at the hopper air outlet to collect the dust in return air, thus to ensure smooth flow in pipeline and reduce the load of return air filter. As there’s the oil component in material which would enter in the honeycomb with airflow, which would reduce the service life of the honeycomb. For honeycomb protection, it equips with the oil filter to filter the oil substance in the return air. The auto loader feeding the drying hopper consists of Separated-vacuum Hopper Loader and vacuum hopper receiver, which guarantees the maximum production demands, largely reduces the labor cost. Besides, the standard cable trunking made the cable follow the trunking for safe and decent layout.
This series of Drying and Dehumidifying system has been delivered to the customer since 3 months ago. The effective material processing greatly improved the production efficiency and product quality. It satisfied the customer’s demands with decent system layout, space saving and better workshop environment, which has well-received by the customer.
A high-tech limited company in Guangdong is engaged in R&D, production and sales of the high performance modified plastics, which is the new technology key enterprise of national torch plan. Their major products include flame-retarded resin, reinforced and toughened resin, plastic alloy and functional masterbatch four series. It is the largest domestic modified plastics manufacturer with most complete range of product series. As the product is the extruding modified plastics, it requires the Drying and Dehumidifying System to obtain a certain degree of dryness before delivery. Therefore we recommended Shini Modular Dryer according to the actual demands, which can be flexibly customized to satisfy different applications. The company purchased Shini large Modular Dryer since 2013, including the Dryer, Honeycomb Dehumidifier, cyclone dust collector, oil filter and auto loader. Because of customers’ special demands, most of the systems are customized.
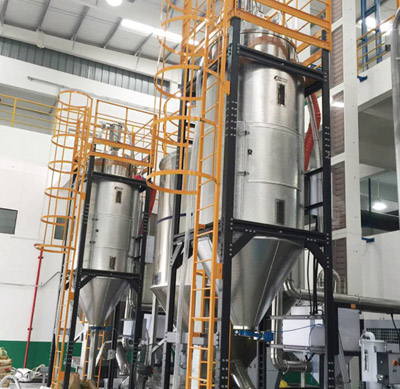
The special design of dying hopper DH-U ensures enough space between the hopper outlet and floor as to place the container bag or storage tank, it’s convenient for the customer to pack the modified materials. All hoppers contact surfaces with material are made of stainless steel to ensure no contamination. The down-blowing design evenly disperses the hot air to maintain the plastic drying and uniform temperature, with improved drying efficiency. Double-layer insulation reduces heat loss. It equipped with the safety ladder and guide rail for convenient equipment repair and maintenance. The pneumatic butterfly valve mounted at the discharge port to control material discharging is convenient for material discharging after being dried. The ladders are equipped both inside and outside the hopper for easy hopper cleaning.
The Honeycomb Dehumidifier is mainly used to collocate with the Dryer to dehumidify the high hygroscopic engineering plastics that could obtain -40℃/-40℉ below dew-point of the drying air, with maximum drying airflow up to 4,000m3/hr. Adopting the full molecular sieve honeycomb for dehumidifying to achieve better effectiveness compared with the silica gel honeycomb. P.I.D temperature control technology precisely controls the regenerative temperature to ensure full regeneration for low dew-point of drying air. The double-cooler design ensures lower return air temperature and dew-point. The built-in filter ensures material free of dust contamination.
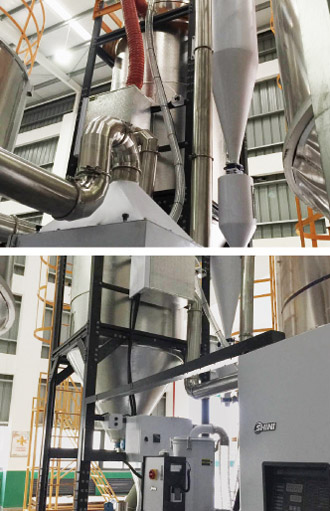
The dehumidifying pipes are made of stainless steel, which possess small wind resistance, good sealing property and strength with decent pipe layout and durability. It mounts the cyclone dust separator at the hopper air outlet to collect the dust in return air, thus to ensure smooth flow in pipeline and reduce the load of return air filter. As there’s the oil component in material which would enter in the honeycomb with airflow, which would reduce the service life of the honeycomb. For honeycomb protection, it equips with the oil filter to filter the oil substance in the return air. The auto loader feeding the drying hopper consists of Separated-vacuum Hopper Loader and vacuum hopper receiver, which guarantees the maximum production demands, largely reduces the labor cost. Besides, the standard cable trunking made the cable follow the trunking for safe and decent layout.
This series of Drying and Dehumidifying system has been delivered to the customer since 3 months ago. The effective material processing greatly improved the production efficiency and product quality. It satisfied the customer’s demands with decent system layout, space saving and better workshop environment, which has well-received by the customer.
Experience Sharing
- STM and Extruder Integrated Control
- Case Sharing of Central Conveying System
- Central Conveying System Facilitates Enterprise’s Transformation and Upgrading
- Case Studies -- Shini Automation Application in Food Industry
If you want to read other articles, back to2016 Quarter 4 Issue 29.