Experience Sharing
2017 Quarter 2 Issue 31
Shini Central Conveying System Used in Auto Parts Industry
One Chongqing Company is specialized for producing auto parts, which mainly engaged in plastics injection molding, surface coating, plastics blow molding and surface draping, possessing 100 sets of equipment for plastics molding processing. The customer plans 12 sets of injection molding machines (five sets of double shooter), with 17 central vacuum hoppers in all to feed 17 components for conveying system. The material needs drying, so it shares three sets of Roots blowers (two for running and one for back up) to supply air for the whole system. Collocating with central filter and cyclone dust separator, it features high efficiency in dust separating, greatly protecting the roots blower.
The whole workshop is formed by 17 storage tanks, 17 sets of Dryers and 17 vacuum hoppers that convey 17 components through pieces of separate pipelines as a big network. Different separate nodes are connected through by two sets of Dryers, two sets of central filters, two rows of exhaust pipes and two sets of central control stations.
Focused on customer’s demands and chasing the pleasure to solve technical issues, Shini successfully completed this central conveying project. Especially in customer’s material room, the pipelines from distribution station to injection molding machine are laid irregularly that make a messed work site. If it takes traditional layout, a part of the space will be occupied, resulting a narrow workshop and depressed atmosphere. So, we particularly designed the “135° elbow”, two pieces in a group, which successfully lead the pipeline into the bottom of platform bypassing the barriers. It built pipes along the bottom that solves the difficulties of piping. Besides, it echoes with the layout of Dryer and blower, giving a clean and well arranged material room.
However, some customers have high demands on the material that requiring each IMM to equip with the small Dryer SHD-12SL and SHD-25SL. As the Dryer is small that is unavailable to mount central vacuum hopper directly, we especially designed the “hemispherical dome” hopper adapter to make perfect matching the hopper and Dryer. Collocating with proportional valve, this decent assembly has fully made use of the granule that largely cut down the cost.
Since its operation, the system has been well received by the customer relying on its reliable stable performance and a well arranged workshop.
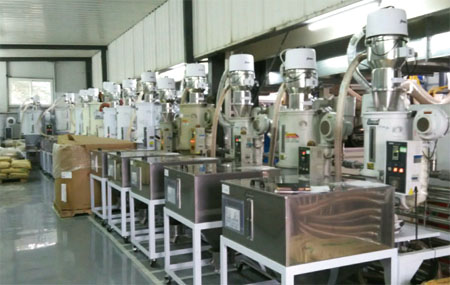
The whole workshop is formed by 17 storage tanks, 17 sets of Dryers and 17 vacuum hoppers that convey 17 components through pieces of separate pipelines as a big network. Different separate nodes are connected through by two sets of Dryers, two sets of central filters, two rows of exhaust pipes and two sets of central control stations.
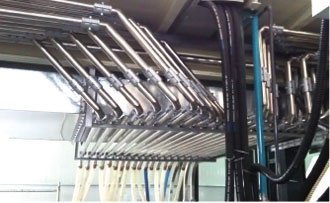
Focused on customer’s demands and chasing the pleasure to solve technical issues, Shini successfully completed this central conveying project. Especially in customer’s material room, the pipelines from distribution station to injection molding machine are laid irregularly that make a messed work site. If it takes traditional layout, a part of the space will be occupied, resulting a narrow workshop and depressed atmosphere. So, we particularly designed the “135° elbow”, two pieces in a group, which successfully lead the pipeline into the bottom of platform bypassing the barriers. It built pipes along the bottom that solves the difficulties of piping. Besides, it echoes with the layout of Dryer and blower, giving a clean and well arranged material room.
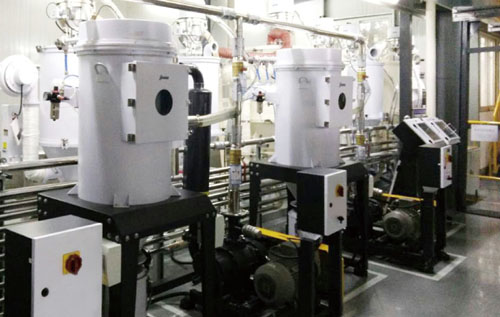
However, some customers have high demands on the material that requiring each IMM to equip with the small Dryer SHD-12SL and SHD-25SL. As the Dryer is small that is unavailable to mount central vacuum hopper directly, we especially designed the “hemispherical dome” hopper adapter to make perfect matching the hopper and Dryer. Collocating with proportional valve, this decent assembly has fully made use of the granule that largely cut down the cost.
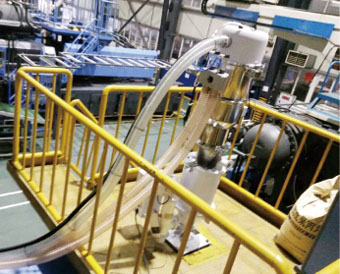
Since its operation, the system has been well received by the customer relying on its reliable stable performance and a well arranged workshop.
Experience Sharing
- Case Sharing of Central Conveying System
- Case studies -- Automation application on household appliance industry
If you want to read other articles, back to2017 Quarter 2 Issue 31.