Special Reports
2013 Quarter 3 Issue 16
Starve Feeding
Stuffed feeding
In plastic molding, stuffed molding is usually the most popular. The so-called stuffed feeding is a molding method that screws are always fully filled by materials. It is because that in normal injection or extrusion process, plastics feeding capacity is always larger than theoretical capacity of injection molding machines or extruders.
Stuffed feeding may leads to the following problems:
Air bubbles
Moisture in material becomes vapor after heating and finds no way out to exhaust, then forms air bubble on the products.
Silver streaks
Moisture in the materials can not exhaust and forms silver streaks on the products.
Partly clouding
Bad textures making caused by gas residual.
Dark spots
Materials overheated and burned during extruding and then form products with dark spots.
Screw/Cylinder abrasion (when processing abrasive materials with fiber contain or barium sulfate) ---imported materials will increase the abrasion of screws of molding machines.
Starve feeding
To solve the above-mentioned problems, starve feeding technology is invented and becomes more and more popular. In starving feeding process, plastics feeding capacity is smaller than theoretical capacity of injection molding machines or extruders, therefore, the screws will not be fully filled.
How starve feeding solve the above-mentioned problems:
During starve feeding, the front end of the molding machine screw is not fully filled. When the material is preheated by the screw, vapor can escape from the material inlet. Therefore, products problems such as air bubble, silver streaks and clouding can be decrease greatly. These problems can also be solved by using a dryer or dehumidifier to dry up the materials, but the cost and energy consumption are much higher than adopting starve feeding. In addition, the pre-drying of materials can help reducing the material burning and abrasion of screw and cylinder.
Due to the incomplete filling of the molding machine screw, materials is not so heavily pressed in the cylinder, as along as the temperature rinsing is within a constant range, material burning will not happen and then black spots will not exist in products.
Shini loss-in-weight feeder
Shini loss-in-weight feeder is designed for starve feeding application. Adopting loss-in-weight principle, by detecting whether the pace of the material discharging in the hopper (also know as the feeding speed of the screw feeder) is the same with the set value of feeding speed, if not, a P.I.D. tuning will take place until error value is less than 1%.
• Color touch screen is equipped to make operation much easier.
• SIEMENS PLC and P.I.D. control to automatically adjust the screw speed to ensure stable feeding.
• Screw is made of wear-resisting stainless steel to ensure no contamination to materials.
• Full set screws to satisfy different materials feeding.
• Loss-in-weight feeding ensures uninterrupted, stable and precise material feeding.
• Materials storage hopper is standard equipped.
• Ethernet modular is optional to realize centralized monitoring.
• Feeding assemblies including vacuum generator, vacuum loader and suitable electrical and pneumatic elements are optional.
• Multi-components feeding control assembly is optional to satisfy proportional feeding of multiple materials.
• Multiple screws can be opted to handing materials of different properties and output.
In plastic molding, stuffed molding is usually the most popular. The so-called stuffed feeding is a molding method that screws are always fully filled by materials. It is because that in normal injection or extrusion process, plastics feeding capacity is always larger than theoretical capacity of injection molding machines or extruders.
Stuffed feeding may leads to the following problems:
Air bubbles
Moisture in material becomes vapor after heating and finds no way out to exhaust, then forms air bubble on the products.
Silver streaks
Moisture in the materials can not exhaust and forms silver streaks on the products.
Partly clouding
Bad textures making caused by gas residual.
Dark spots
Materials overheated and burned during extruding and then form products with dark spots.
Screw/Cylinder abrasion (when processing abrasive materials with fiber contain or barium sulfate) ---imported materials will increase the abrasion of screws of molding machines.
Starve feeding
To solve the above-mentioned problems, starve feeding technology is invented and becomes more and more popular. In starving feeding process, plastics feeding capacity is smaller than theoretical capacity of injection molding machines or extruders, therefore, the screws will not be fully filled.
How starve feeding solve the above-mentioned problems:
During starve feeding, the front end of the molding machine screw is not fully filled. When the material is preheated by the screw, vapor can escape from the material inlet. Therefore, products problems such as air bubble, silver streaks and clouding can be decrease greatly. These problems can also be solved by using a dryer or dehumidifier to dry up the materials, but the cost and energy consumption are much higher than adopting starve feeding. In addition, the pre-drying of materials can help reducing the material burning and abrasion of screw and cylinder.
Due to the incomplete filling of the molding machine screw, materials is not so heavily pressed in the cylinder, as along as the temperature rinsing is within a constant range, material burning will not happen and then black spots will not exist in products.
Shini loss-in-weight feeder
Shini loss-in-weight feeder is designed for starve feeding application. Adopting loss-in-weight principle, by detecting whether the pace of the material discharging in the hopper (also know as the feeding speed of the screw feeder) is the same with the set value of feeding speed, if not, a P.I.D. tuning will take place until error value is less than 1%.
• Color touch screen is equipped to make operation much easier.
• SIEMENS PLC and P.I.D. control to automatically adjust the screw speed to ensure stable feeding.
• Screw is made of wear-resisting stainless steel to ensure no contamination to materials.
• Full set screws to satisfy different materials feeding.
• Loss-in-weight feeding ensures uninterrupted, stable and precise material feeding.
• Materials storage hopper is standard equipped.
• Ethernet modular is optional to realize centralized monitoring.
• Feeding assemblies including vacuum generator, vacuum loader and suitable electrical and pneumatic elements are optional.
• Multi-components feeding control assembly is optional to satisfy proportional feeding of multiple materials.
• Multiple screws can be opted to handing materials of different properties and output.
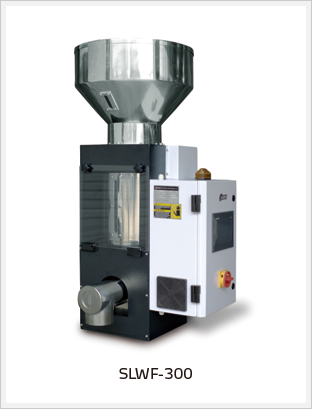
Special Reports
- The Principle and Application of Industrial Air Chiller
- Cold Mold Sweat Dehumidifier
- Temperature Control in Hot Runner System——Heaters
- New Brand Image Shines at CHINAPLAS 2013
- About CHINAPLAS 2013 of Shini-Syncro Extrusion
If you want to read other articles, back to2013 Quarter 3 Issue 16.