Special Reports
2014 Quarter 1 Issue 18
The Application of P.I.D. Temperature Control System in Plastics Auxiliary Equipment
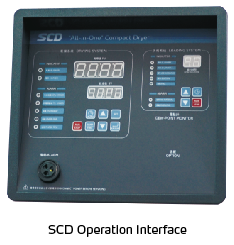
Temperature control system is widely applied in the industry of plastics auxiliary equipments, like temperature control for material drying, mold temperature control and cooling water temperature control. Both the controlling way and effect of temperature control system directly decide product quality, energy consumption and production efficiency. The traditional ON/OFF controlling way may make the target’s temperature fluctuate and bring bad temperature control accuracy. With P.I.D. control which can help eliminate inertia temperature error, it features precise temperature control, convenient setting of parameters and high reliability. Therefore, it’s widely used.
The control flow chart of temperature control system is as follows. P.I.D. controller calculates basing on the values of SV and PV. Then it will directly drive the contactor or solid-state relay to conduct PWM output. It controls the pipe heater’s ratio of on-off time within the setting control cycle to realize the control of heating power and thus to adjust the temperature.
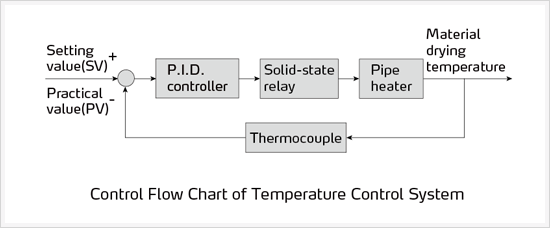
P.I.D. controller is a linear controller which produces the control deviation e(t) basing on the given value r(t) and the actual output c(t).
e(t)=r(t)-c(t)
Percentage (P), integral (I) and differential (D) of deviation value e(t) produce an control output through linear combination to control the target. Regular P.I.D. control system principle block diagram is shown as the following.
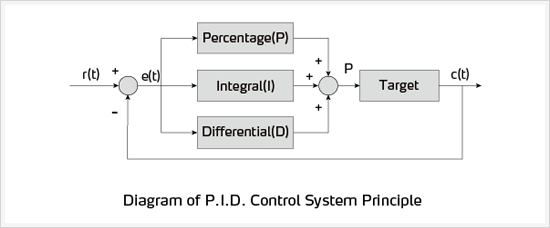
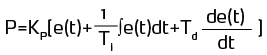
The above expression tells that the control output P is decided not only by deviation e(t) but also by proportional gain KP, integral time Ti and rate time Td.
For P.I.D. control system, it usually requires small temperature overshoot, short adjusting time and no static error. To achieve such an effect, the key lies in appropriate selection of parameters of percentage (P), integral (I) and differential (D)
Influence of each P.I.D. parameter on system:
1) When increasing the factor of proportionality (P), it will accelerate the system response. Besides, it’s helpful for reducing the static error. However, overlarge factor of proportionality brings the system bigger overshoot and vibration, which makes the stability turn bad.
2) Increase of the integral time (I) is helpful for decreasing the overshoot and vibration, which will make the system more stable. However, it will make the elimination of static differential slow down.
3) Increase of the differential (D) also can accelerate the system response. Besides, it can decrease the overshoot to improve the stability. However, the system gets weak at inhibiting ability toward interference and sensitive to it.
Special Reports
If you want to read other articles, back to2014 Quarter 1 Issue 18.