Experience Sharing
2020 Quarter 4 Issue 41
The Case of Central Material Processing System
A Precision
Manufacturing Technology Co., Ltd. in Guangdong Province is a national
high-tech enterprise mainly engaged in developing and manufacturing key
automotive parts and components, and the sales of electric equipment and machinery,
special copper strip, three-layer insulated wire and other products.
The customer plans to employ a set of central material processing system
for the production of three-layer insulation wire as per actual production demands.
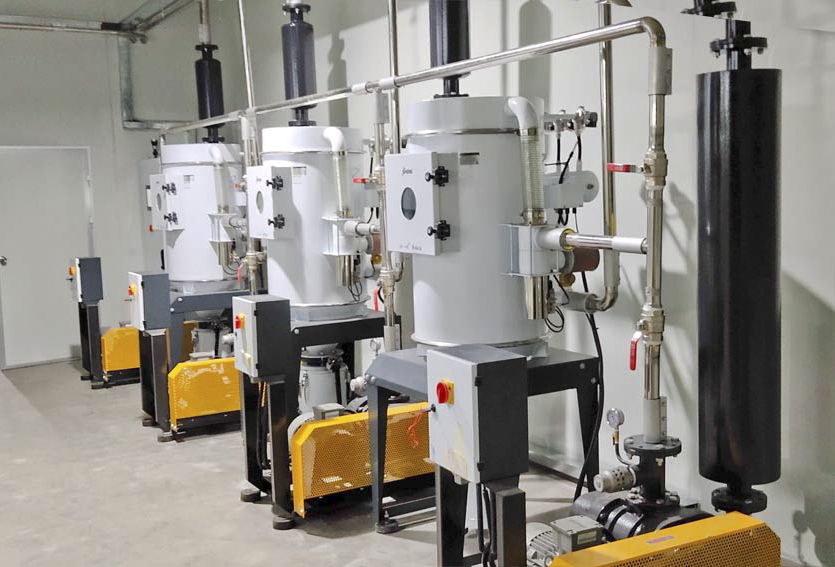
The three-layer insulated wire is a high-performance insulation wire newly developed in recent years. After in-depth communication with the customer, we customized an effective central material processing system for them according to their actual process requirements.
Workshop Configuration
This system plan makes full use ofthe original equipments in the workshop. It converts the dehumidifiers and small drying hoppers (including 48 hoppers in 16 lines), employs the central vacuum hopper receiver SHR-6U-S, and mounts the adapter on the hopper dryer SHD-25 to ensure continuous production while saving the costs.
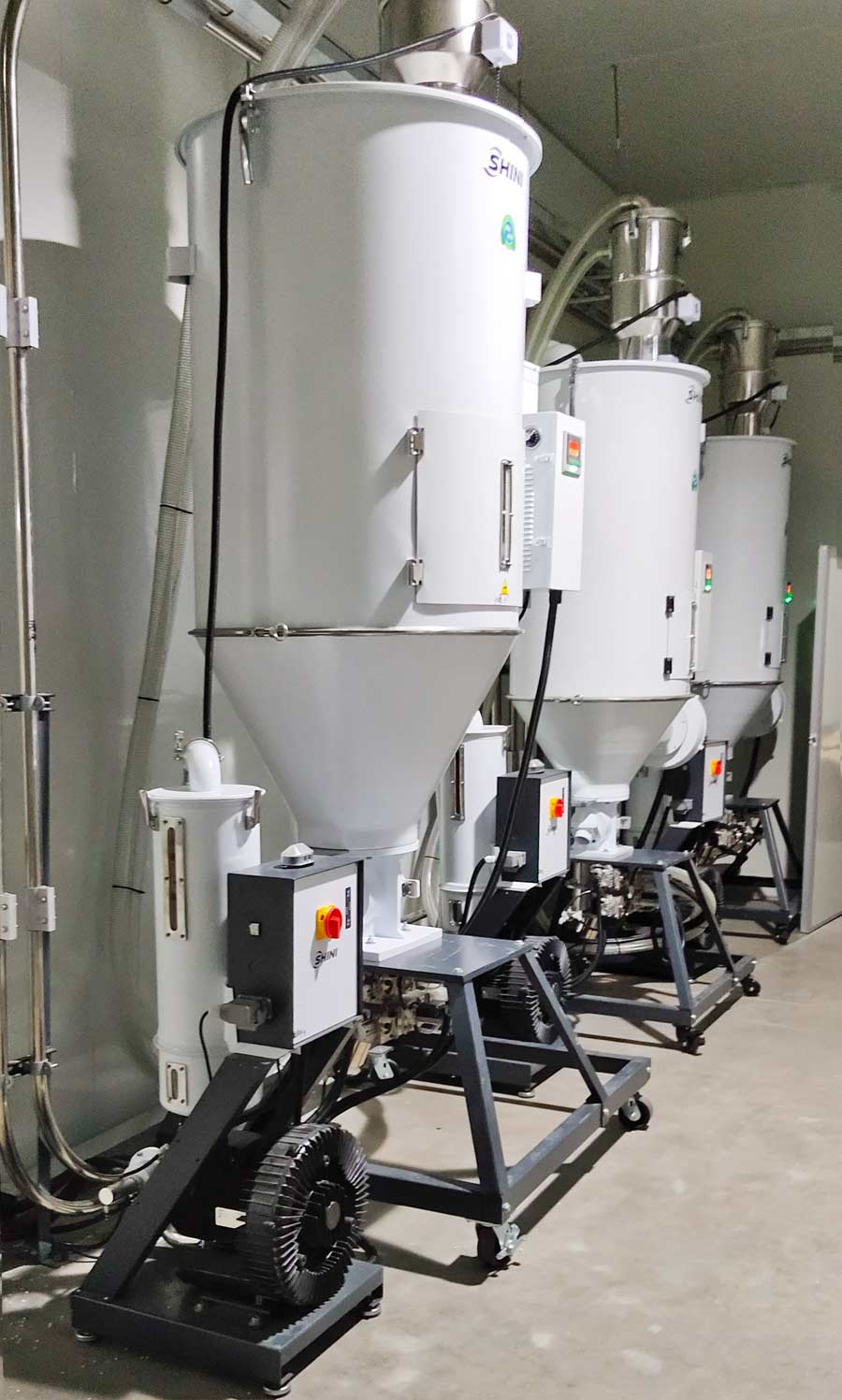
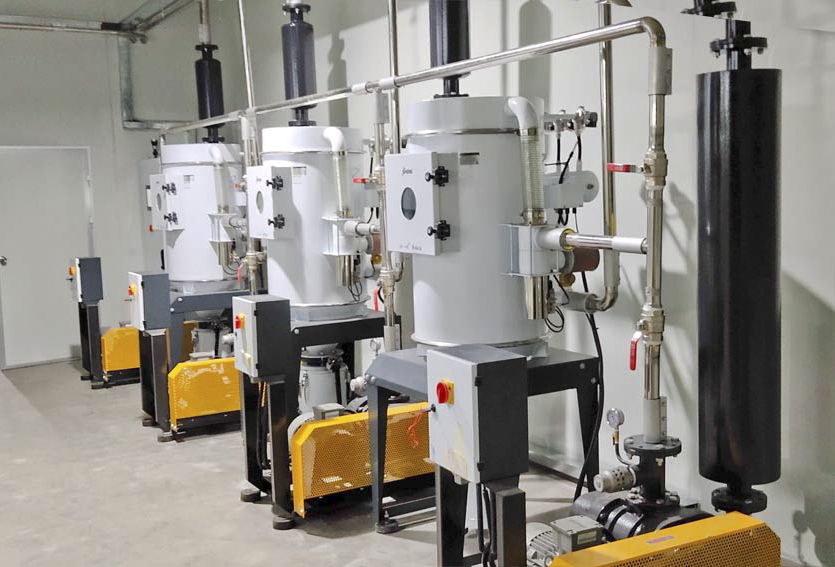
The three-layer insulated wire is a high-performance insulation wire newly developed in recent years. After in-depth communication with the customer, we customized an effective central material processing system for them according to their actual process requirements.
Workshop Configuration
This system plan makes full use ofthe original equipments in the workshop. It converts the dehumidifiers and small drying hoppers (including 48 hoppers in 16 lines), employs the central vacuum hopper receiver SHR-6U-S, and mounts the adapter on the hopper dryer SHD-25 to ensure continuous production while saving the costs.
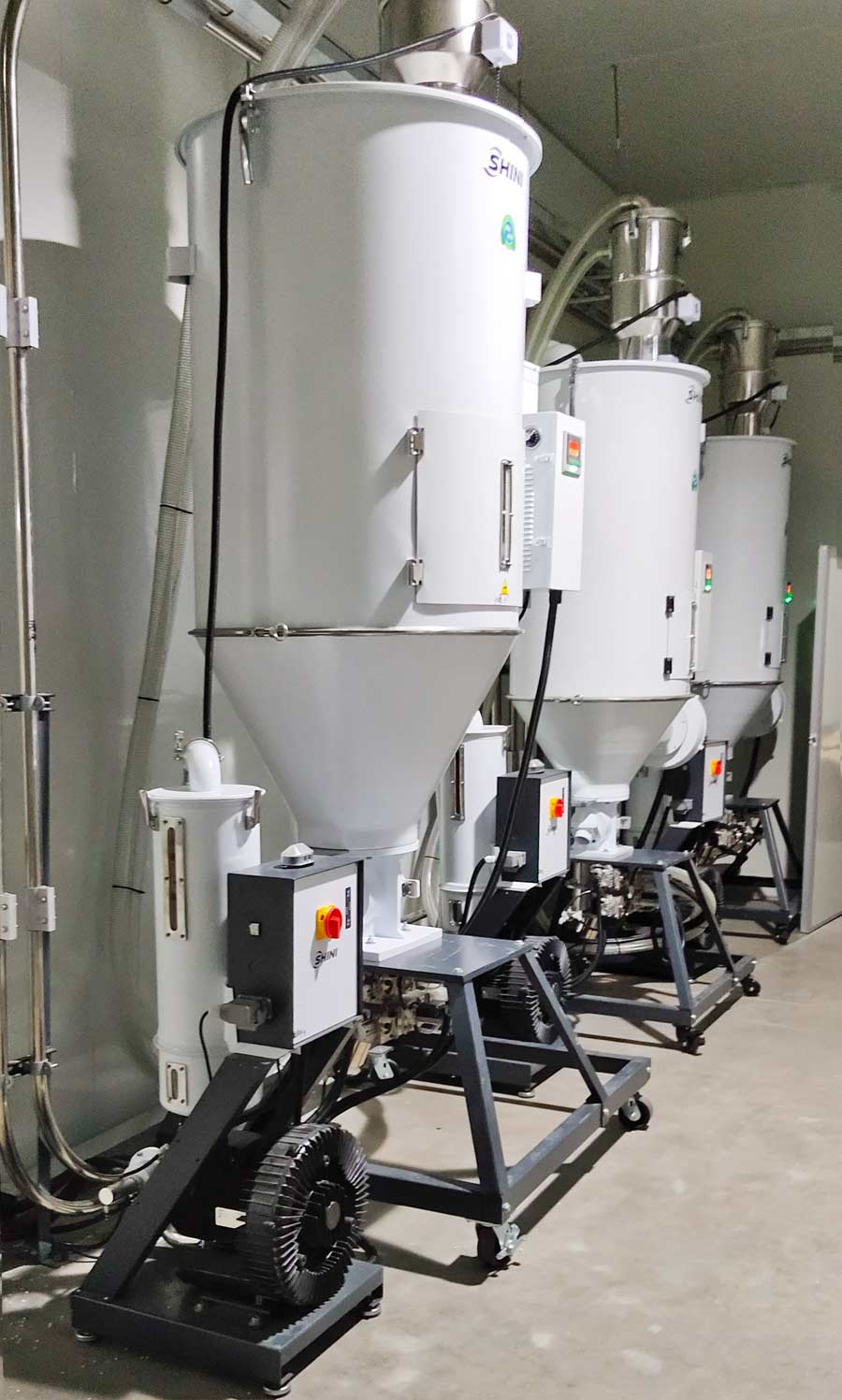
The Configuration of Material Room
There are three sets of SEHD Energy-efficient Hopper Dryers in the material room drying three kinds of materials respectively. Each hopper dryer has a Roots blower SRB, with another set of the Roots blower standby. These three kinds of materials are delivered independently without interference.
The materials are temporarily stored in the storage tank, and are transported into the vacuum hopper receivers on drying hoppers via three sets of Separate-vacuum Hopper Loaders SAL-5HP-UG. Then, they are transported into the hoppers of the extruder after being dried by the roots blowers. During the whole process, it only requires manual feeding to the mixer, and all subsequent processes are automatic, thus improving the production efficiency and saving many processes and labor works.
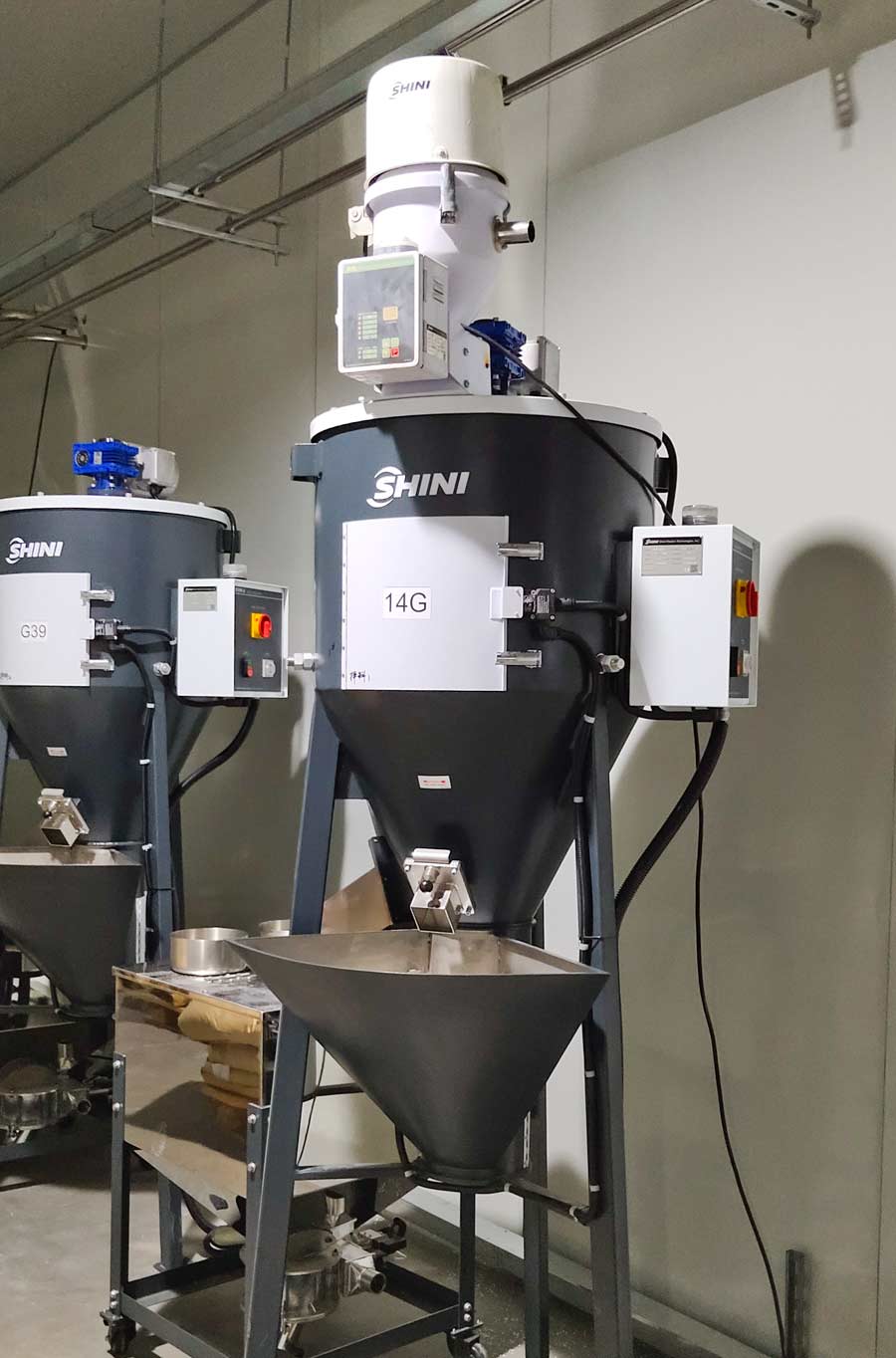
System Establishment
To put the system into operation as soon as possible, improve the customer factory’s working efficiency, and reduce the manpower impact on production, Shini raced against the time and successfully delivered the project as scheduled with high quality relying on the engineering technicians from all production bases across the regions. That was all on the basis of our solid strength and sufficient coordination ability when facing serious manpower shortage caused by synchronous works of many projects during the COVID-19 pandemic period.
There are three sets of SEHD Energy-efficient Hopper Dryers in the material room drying three kinds of materials respectively. Each hopper dryer has a Roots blower SRB, with another set of the Roots blower standby. These three kinds of materials are delivered independently without interference.
The materials are temporarily stored in the storage tank, and are transported into the vacuum hopper receivers on drying hoppers via three sets of Separate-vacuum Hopper Loaders SAL-5HP-UG. Then, they are transported into the hoppers of the extruder after being dried by the roots blowers. During the whole process, it only requires manual feeding to the mixer, and all subsequent processes are automatic, thus improving the production efficiency and saving many processes and labor works.
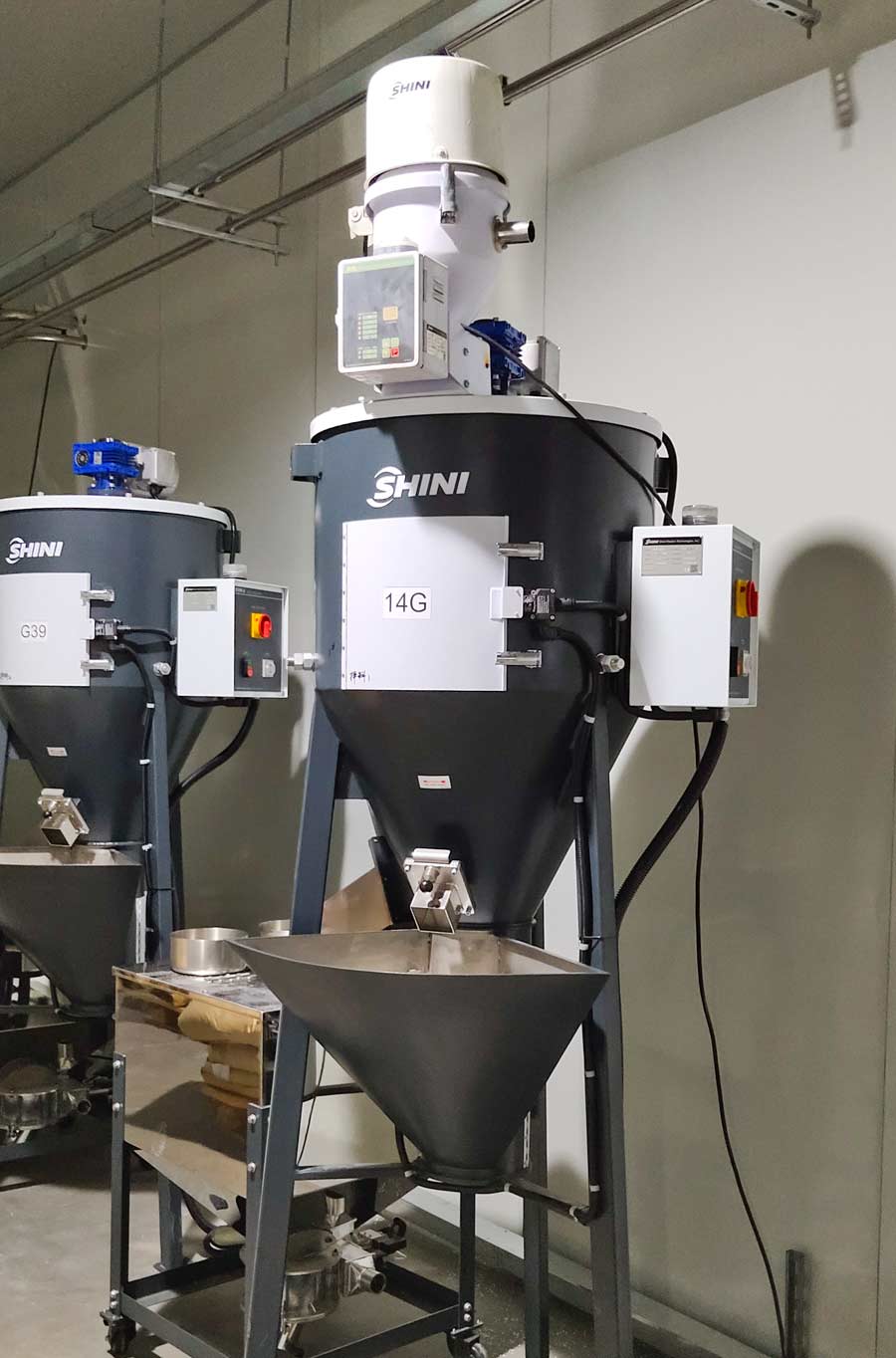
System Establishment
To put the system into operation as soon as possible, improve the customer factory’s working efficiency, and reduce the manpower impact on production, Shini raced against the time and successfully delivered the project as scheduled with high quality relying on the engineering technicians from all production bases across the regions. That was all on the basis of our solid strength and sufficient coordination ability when facing serious manpower shortage caused by synchronous works of many projects during the COVID-19 pandemic period.
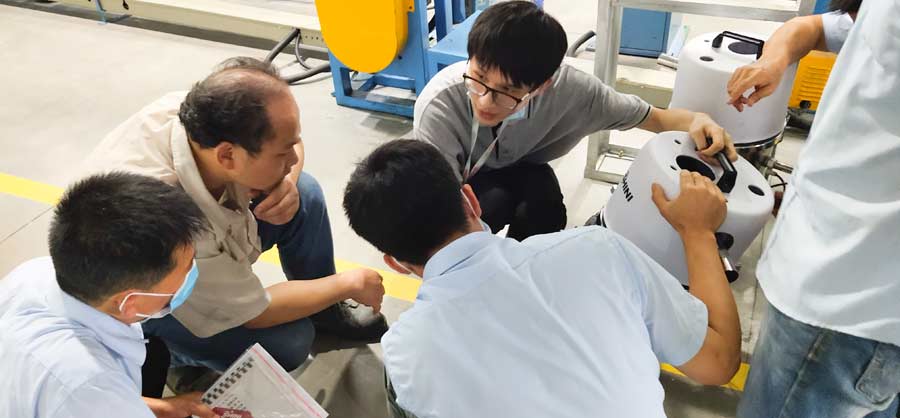
Experience Sharing
If you want to read other articles, back to2020 Quarter 4 Issue 41.