Experience Sharing
2022 Quarter 1 Issue 46
Application of Large Granulator in Plastic Recycling Industry
Plastics-related industries hold an important place in the world today. Over the years, the production of plastic products has been developed fast worldwide. Since the 21st century, the scale of China's plastic products industry has been growing continuously, and plastic parts have been widely used in construction and real estate, packaging industry, automobile, household appliances, consumer electronics, medical devices, and other industrial fields, which have great potential for the demands in the future market.
The continuous development of the plastic industry has inevitably produced a lot of plastic waste. Thus, the issue of plastics recycling has become increasingly important, and the problem urgently needs to be solved by all countries in the world.
Meanwhile, many influential institutions or platforms in the plastic industry have successively proposed taking the circular economy as the key point of promotion, pushing the industry towards environmental protection green and sustainable development direction. In such a wave, Shini has fully adapted to the trend and launched various solutions for plastic recycling. However, plastic granulators play an important role, and especially large granulators are an important link in plastic batch recycling.
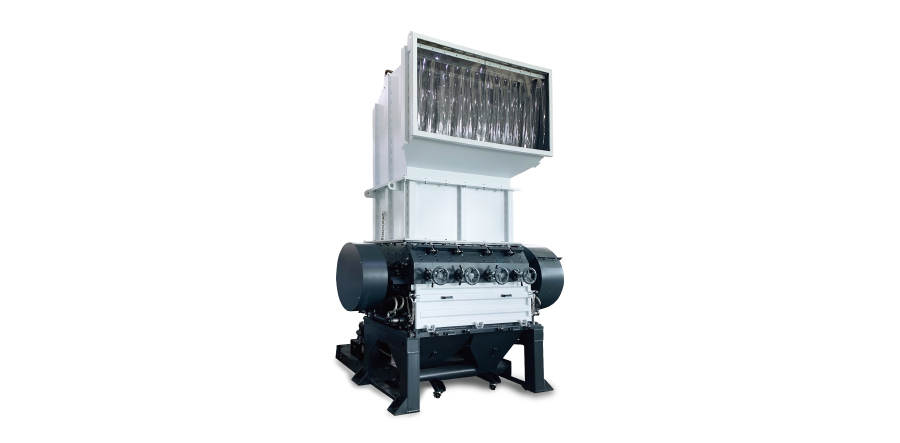
SG-50 series
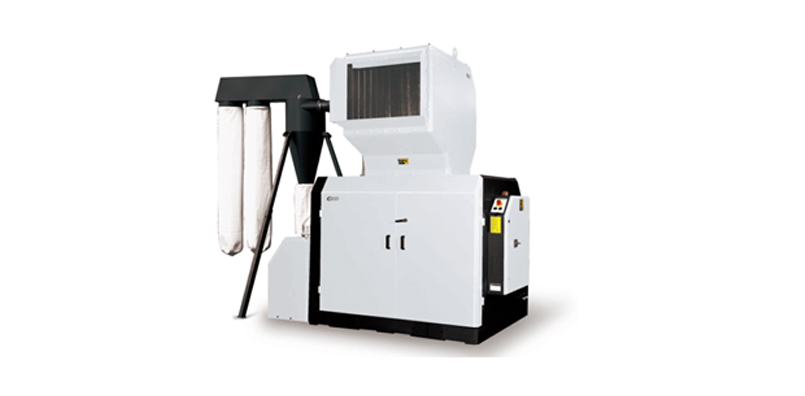
SG-50 series
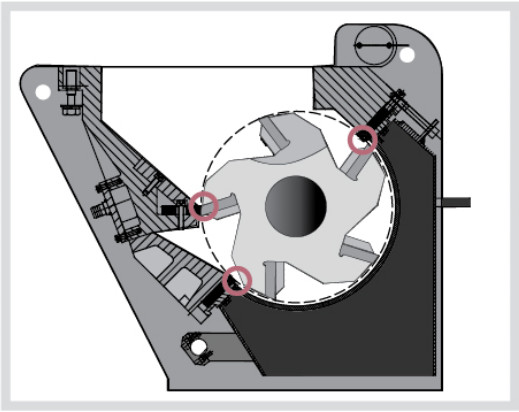
Cutter type 5*3
The continuous development of the plastic industry has inevitably produced a lot of plastic waste. Thus, the issue of plastics recycling has become increasingly important, and the problem urgently needs to be solved by all countries in the world.
Meanwhile, many influential institutions or platforms in the plastic industry have successively proposed taking the circular economy as the key point of promotion, pushing the industry towards environmental protection green and sustainable development direction. In such a wave, Shini has fully adapted to the trend and launched various solutions for plastic recycling. However, plastic granulators play an important role, and especially large granulators are an important link in plastic batch recycling.
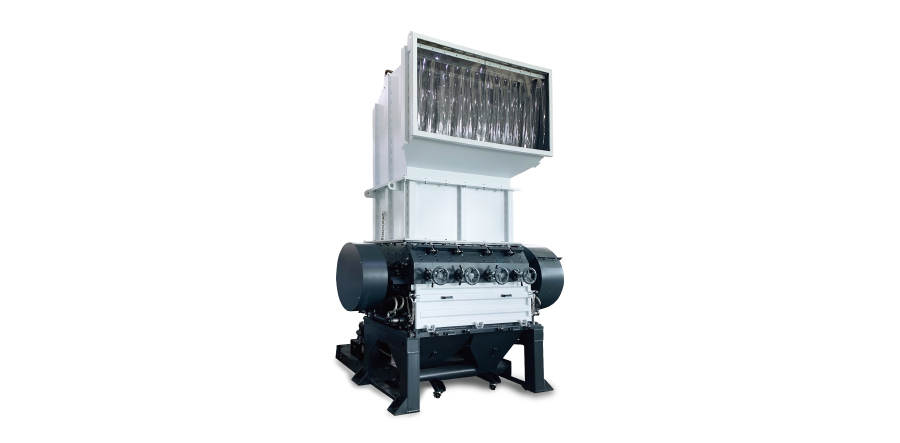
SG-50 series
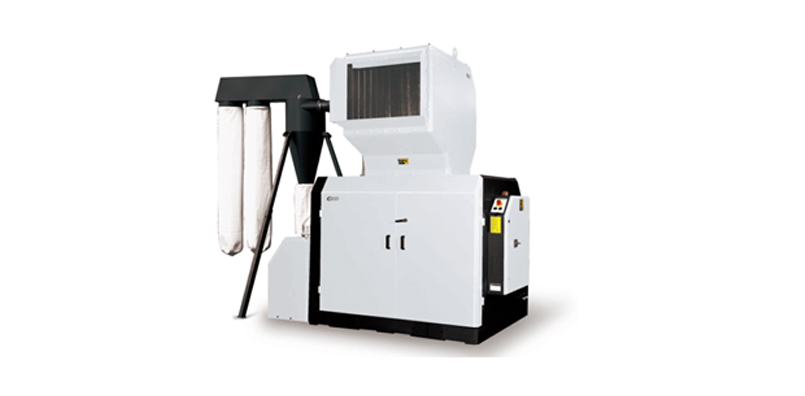
SG-50 series
According to different market demands, Shini can provide large granulators of various sizes and specifications to the market, such as SG-50,SG-70, SG-90, etc., covering many different application levels. The maximum crushing capacity can reach up to 4000kg/hr, which meets the demands of varying plastic recycling capacities.
According to the working condition, the structure of the large granulator can be divided into different configurations, suitable for crushing various large or thick wall plastic products, including wastes generated after the injection molding, blow molding, or extrusion molding, thus achieving centralized crushing, recycling, and reuse. According to the shape, material, and size of the materials to be crushed, it can adjust the granulator's cutter structure appropriately. For example, for large size plastic products with empty shells, reducing the row of the cutter can increase the adequate space of the cutting, making it easy for the blade to catch and crush the products; For solid thick-wall materials, expanding the row of the blade can improve the cutting efficiency of the blades per unit time and the crushing capacity.
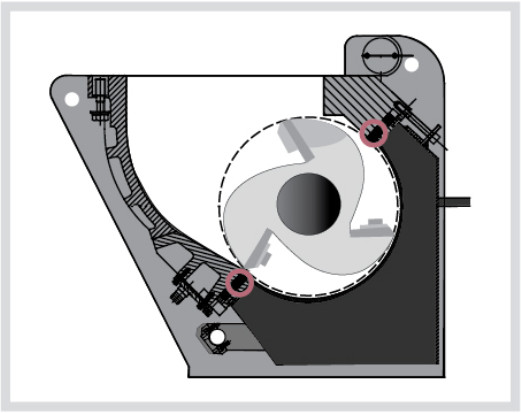
Cutter type 3*2
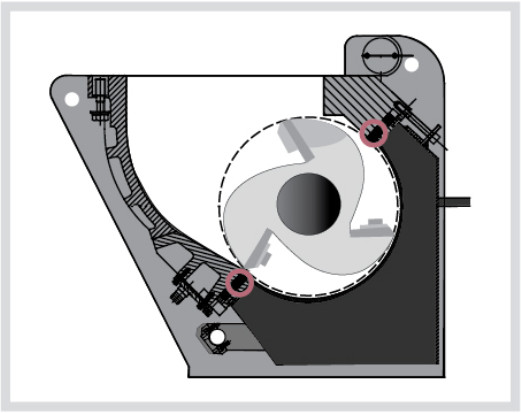
Cutter type 3*2
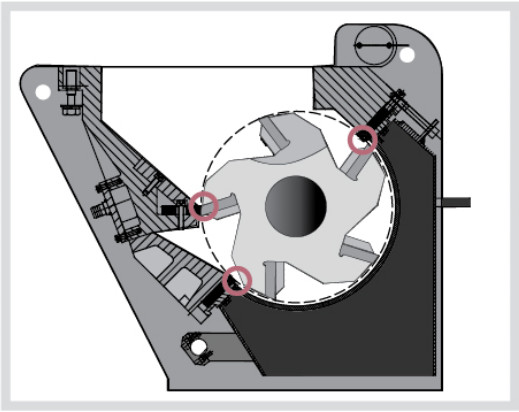
Cutter type 5*3
Real case:
A company in Zhejiang specializes in all kinds of foamed cottons, which produces many wastes of foamed cottons in different shapes and results in heavy crushing tasks. In the early stage, the factory only has a small granulator, and it needs manual cutting and splitting during crushing. Otherwise, it will not feed and crush, resulting in insufficient output and low working efficiency. After knowing the demands and "pain points" of the customer, Pinghu Shini proposed to use two Regular series granulators SG-90200B and customize the feed port crushing plant, thus significantly improving the production capacity and making whole bundle feeding directly available to achieve the productivity reaching up to 4000kg/hr.
A company in Zhejiang specializes in all kinds of foamed cottons, which produces many wastes of foamed cottons in different shapes and results in heavy crushing tasks. In the early stage, the factory only has a small granulator, and it needs manual cutting and splitting during crushing. Otherwise, it will not feed and crush, resulting in insufficient output and low working efficiency. After knowing the demands and "pain points" of the customer, Pinghu Shini proposed to use two Regular series granulators SG-90200B and customize the feed port crushing plant, thus significantly improving the production capacity and making whole bundle feeding directly available to achieve the productivity reaching up to 4000kg/hr.
Experience Sharing
- A Step Towards the "New" Progress with Mutual Trust
- The Application of Plastic Molding Auxiliary Equipment in Auto Parts Industry
- Case Sharing – The Application of Central Material Processing System in Auto Parts Industry
- Automation in electric tools industry
If you want to read other articles, back to2022 Quarter 1 Issue 46.