Experience Sharing
2022 Quarter 1 Issue 46
Case Sharing – The Application of Central Material Processing System in Auto Parts Industry
As people’s consuming ability enhances, automobiles have entered thousands of households and become essential tools of the family. Among many automobile production cycles, it has taken up an increasing proportion to use plastic parts due to their superior performances and cost. Therefore, the molding process of related automotive plastic accessories is becoming increasingly important, which has become a significant research field.
In producing automotive plastic accessories, the pretreatment of materials is an essential link, including material conveying, dehumidifying and drying, auto proportioning, etc. Owing to the automatic, digitalized, and humanized characteristics, the central material processing system can provide an excellent solution for material pretreatment. It has gradually become the popular operation mode. Besides, equipment division and layout make the plant’s 5S management more effective, making it more friendly for the operator to use and manage the equipment. Moreover, plastic auto conveying vastly reduces the cost loss in material transport in traditional operation mode. It facilitates the centralized management of the materials.
An Auto Parts Co., Ltd. in Chongqing mainly sells auto interior accessories and spare parts. The materials they commonly use are plastic PP granules and regrinds. The company has eight injection molding machines of 470t to 2400t. The control system reserves the expansion space, laying a solid foundation to expand production in the future. Moreover, it only needs to add the hardware to improve productivity, thus optimizing the cost while meeting the customer’s demands.
In the whole system, the materials are stored in the material storage tank to prevent misoperation during material supplement. The material storage tank is equipped with the material error-proofing function, which uses the wireless barcode scanning guns to scan the granule’s code. It started material suction when the code scanned is consistent with the system preset or the required material’s code. The whole system design integrates drying, dust-removing, storage, and material conveying in one. It only needs manual work to feed the materials in the tank. Then, switch to the correct material in the material distribution station and control station as demands, and the system can run automatically.
All pipe fittings are supported and fixed by workshop columns, walls, suspended ceilings, or other supports, making a neat workshop neat and in good order. That makes full use of the upper space and always keeps a good look and feel. Besides, the dust collective bin is placed away from the production site to maintain a clean environment.
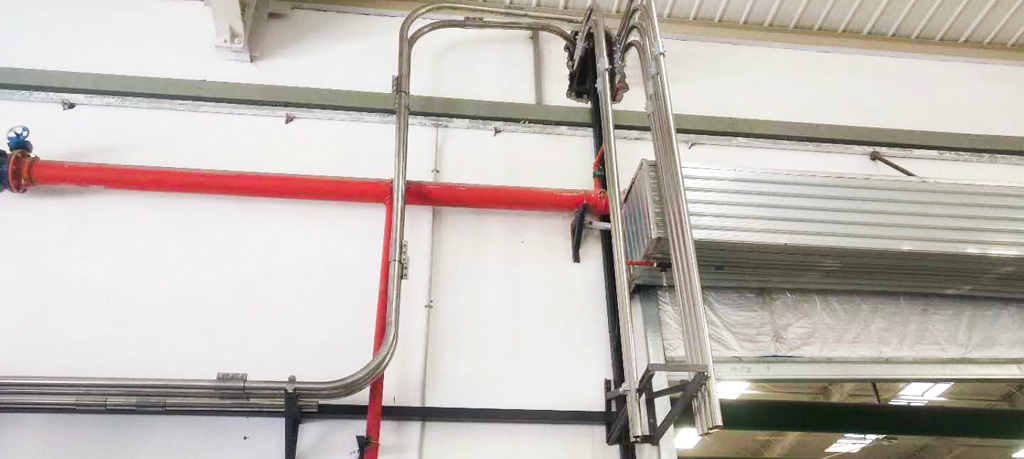
In the future, the era driven by the data is coming toward us, and the data from production, running equipment, etc., will push forward the progress of informatization. Therefore, Shini launched the central material processing system based on self develop sFactory Smart Plant software, providing the intelligent and integrated material processing solution. In addition, the Shini material processing solution can match other auxiliary equipment and systematic plans in practice to make all develop in-depth and expand in scope, providing the market with one-stop, simple, and practical solutions.
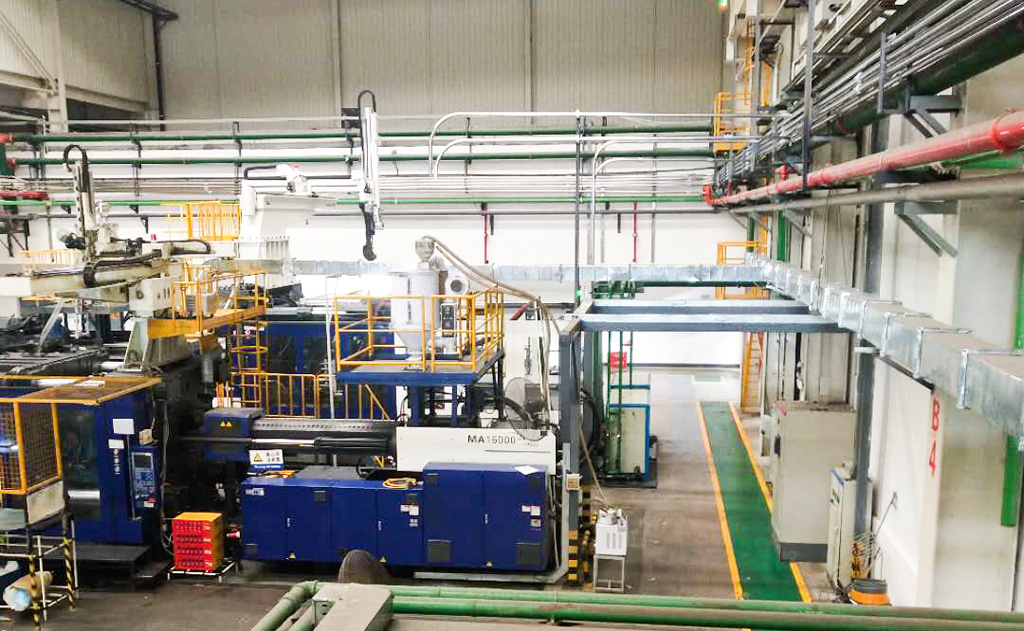
In producing automotive plastic accessories, the pretreatment of materials is an essential link, including material conveying, dehumidifying and drying, auto proportioning, etc. Owing to the automatic, digitalized, and humanized characteristics, the central material processing system can provide an excellent solution for material pretreatment. It has gradually become the popular operation mode. Besides, equipment division and layout make the plant’s 5S management more effective, making it more friendly for the operator to use and manage the equipment. Moreover, plastic auto conveying vastly reduces the cost loss in material transport in traditional operation mode. It facilitates the centralized management of the materials.
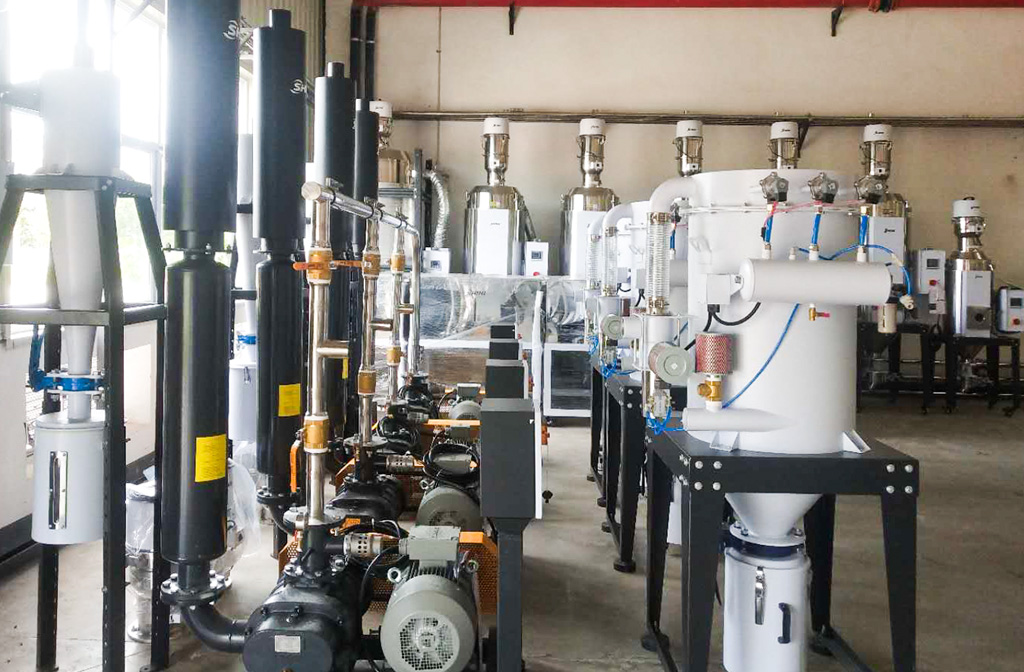
An Auto Parts Co., Ltd. in Chongqing mainly sells auto interior accessories and spare parts. The materials they commonly use are plastic PP granules and regrinds. The company has eight injection molding machines of 470t to 2400t. The control system reserves the expansion space, laying a solid foundation to expand production in the future. Moreover, it only needs to add the hardware to improve productivity, thus optimizing the cost while meeting the customer’s demands.
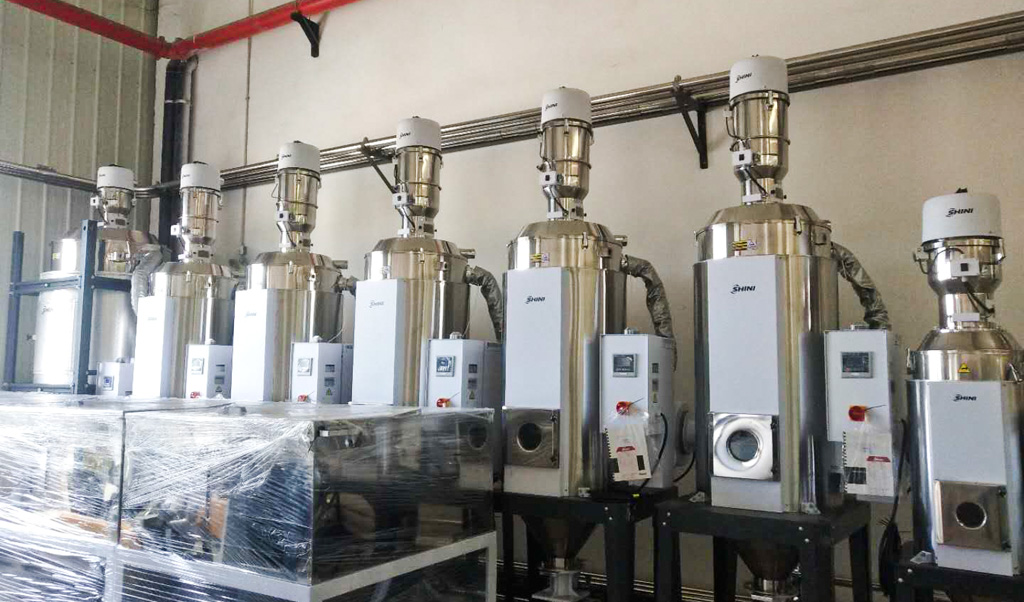
In the whole system, the materials are stored in the material storage tank to prevent misoperation during material supplement. The material storage tank is equipped with the material error-proofing function, which uses the wireless barcode scanning guns to scan the granule’s code. It started material suction when the code scanned is consistent with the system preset or the required material’s code. The whole system design integrates drying, dust-removing, storage, and material conveying in one. It only needs manual work to feed the materials in the tank. Then, switch to the correct material in the material distribution station and control station as demands, and the system can run automatically.
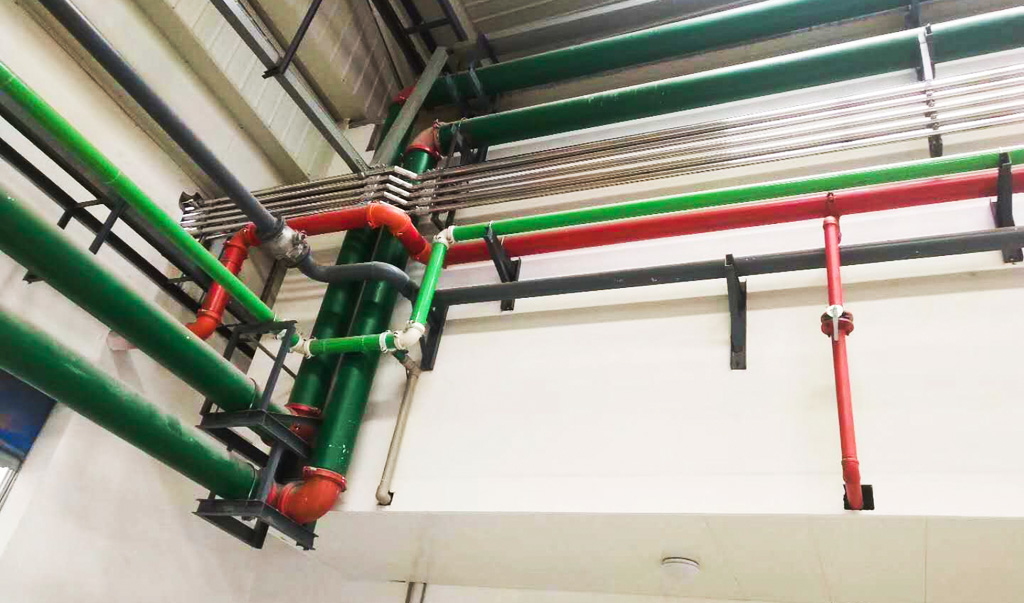
All pipe fittings are supported and fixed by workshop columns, walls, suspended ceilings, or other supports, making a neat workshop neat and in good order. That makes full use of the upper space and always keeps a good look and feel. Besides, the dust collective bin is placed away from the production site to maintain a clean environment.
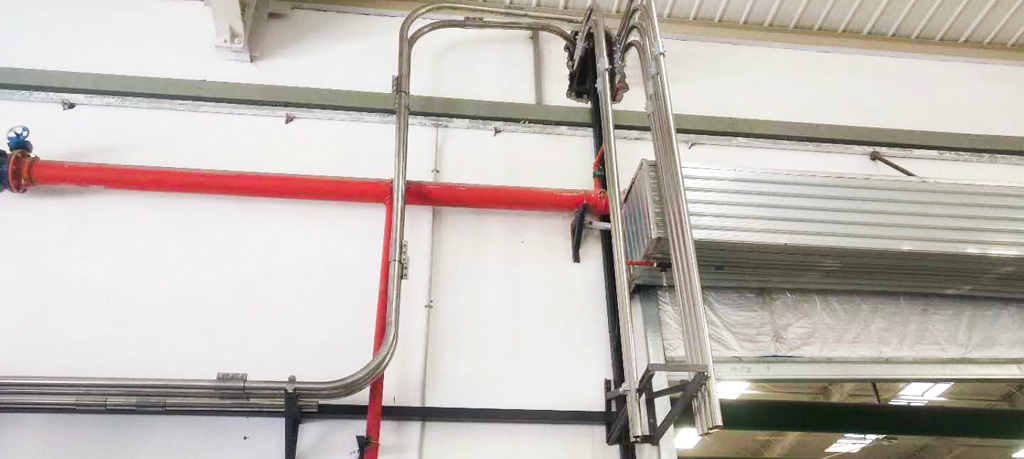
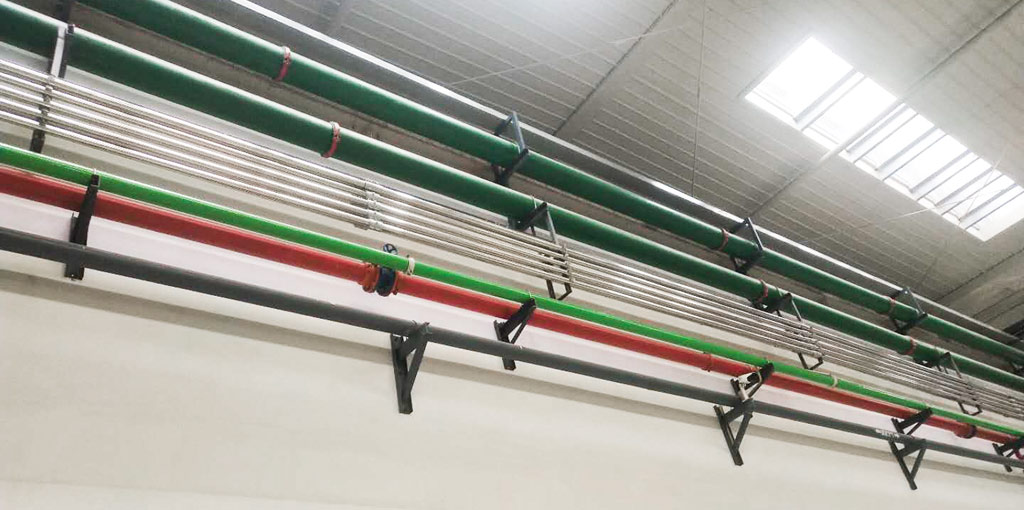
In the future, the era driven by the data is coming toward us, and the data from production, running equipment, etc., will push forward the progress of informatization. Therefore, Shini launched the central material processing system based on self develop sFactory Smart Plant software, providing the intelligent and integrated material processing solution. In addition, the Shini material processing solution can match other auxiliary equipment and systematic plans in practice to make all develop in-depth and expand in scope, providing the market with one-stop, simple, and practical solutions.
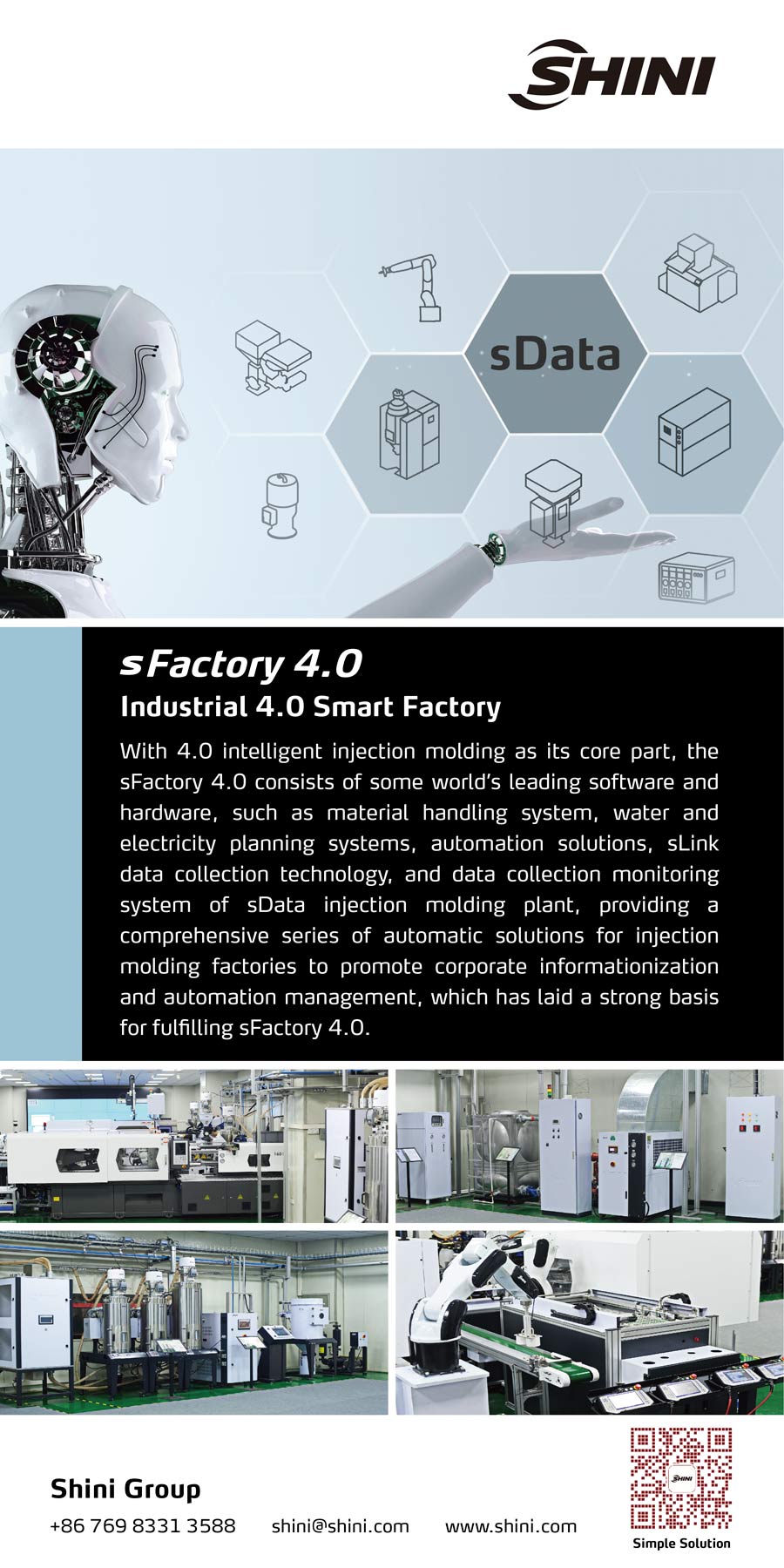
Experience Sharing
- A Step Towards the "New" Progress with Mutual Trust
- The Application of Plastic Molding Auxiliary Equipment in Auto Parts Industry
- Application of Large Granulator in Plastic Recycling Industry
- Automation in electric tools industry
If you want to read other articles, back to2022 Quarter 1 Issue 46.