Special Reports
2022 Quarter 1 Issue 46
Different Applications of Single-shaft Shredder and Large Granulator
Shini has a good range of auxiliary equipment for plastic process needs. Among them, the granulating and recycling series has complete plastics granulating and recycling equipment. The products include the low-speed Granulator, central Granulator, roll-feed Granulator, and single-shaft Shredder that can significantly meet the granulating and shredding demands of plastic recycling on the market.
The single-shaft shredder is also called Plastics Shredding Machine and Single-shaft Shredding Machine, and it is driven by the relative rotation between the rotating cutter block and fixed blades. It adopts a milling smashing design and uses the screen to control the output granule size, which can shred the plastics into granules to get desired plastic granules. In the shredding chamber, the cutter structure is shown as below:
Materials’ shredding process
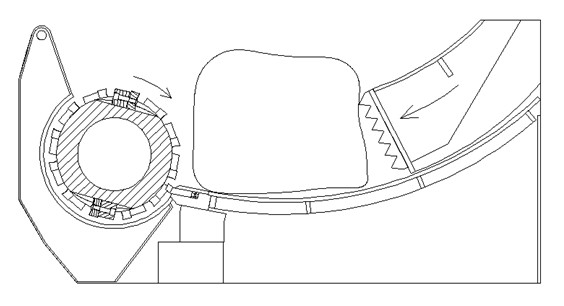
1. The pushing block pushes the materials to the rotating cutter shaft
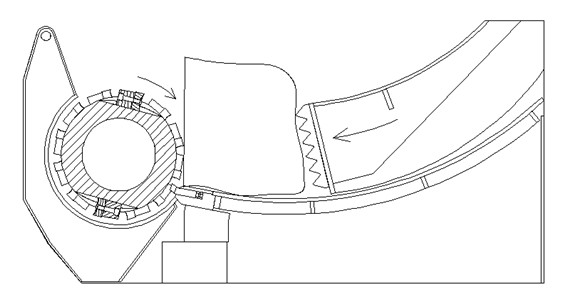
2. The rotating cutter block shreds the materials
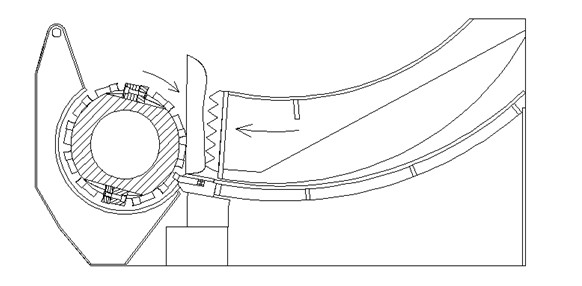
3. The pushing block continues to push the materials to the rotating cutter shaft, and the large materials are shredded into small pieces.
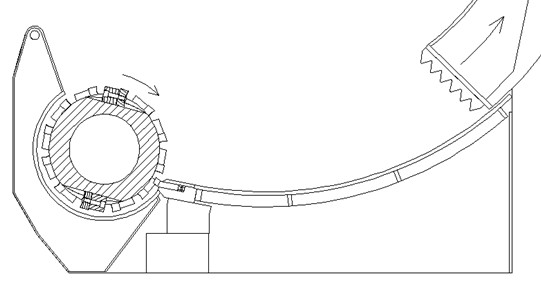
4. The pushing block returns and repeats the process until all the material is shredded into smaller pieces to pass through the screen.
Application: It applies to crushing especially large, thick, and solid materials, which has a wide application range, including large head wastes from the injection molding, blow molding, or extrusion molding.
A plastics granulator refers to a machine used for granulating plastic materials, and it can cut large plastic parts into suitable granules. Its working principle is the rotating blades in the cutting chamber rotating relatively against the fixed blade to crush the materials.
The Selection of Large Granulator
The feed port diameter, cutting chamber diameter, and cutting motor power of the large granulator are relatively huge, which can granulate large plastic materials. When the small or middle granulator is too hard to crush large plastic wastes, we can provide the large granulator to meet customer demand. The large granulator also has two different cutting chamber structures, and the application is as below:
3 Rotating Blades and 2 Fixed Blades (Standard Type)
The low cut point design and low initial cutting point of the fixed blade in the cutting chamber make big inlet space in the chamber, and the material can be easily grabbed and cut after entering the cutting chamber. The cutting chamber design is ideal for granulating large hollow objects and framework materials that can be crushed to desired particles directly after granulating, and the cutting chamber’s structure is as follows:
5 Rotating Blades and 3 Fixed Blades
This semi-closed rotor has smaller spaces between the blade rows, thus preventing material from falling into the rotor. The high cut point design and high initial cutting point of the fixed blade in the cutting chamber make small inlet space in the chamber; consequently, there is less aggressive action meaning no blockage or rotor stall even under the most extreme conditions. The cutting chamber design is ideal for granulating small head wastes, thick wall objects, and plates after the injection molding production, and the cutting chamber’s structure is as follows:
Application: The Central Granulator is a good choice for customers who have to crush many waste materials from injection molding, extrusion molding, or blow molding. The main parameters for the selection include the material size, required cutting ability (i.e., the amount to be crushed per hour), and whether it is fiber contained materials.
The single-shaft shredder is also called Plastics Shredding Machine and Single-shaft Shredding Machine, and it is driven by the relative rotation between the rotating cutter block and fixed blades. It adopts a milling smashing design and uses the screen to control the output granule size, which can shred the plastics into granules to get desired plastic granules. In the shredding chamber, the cutter structure is shown as below:
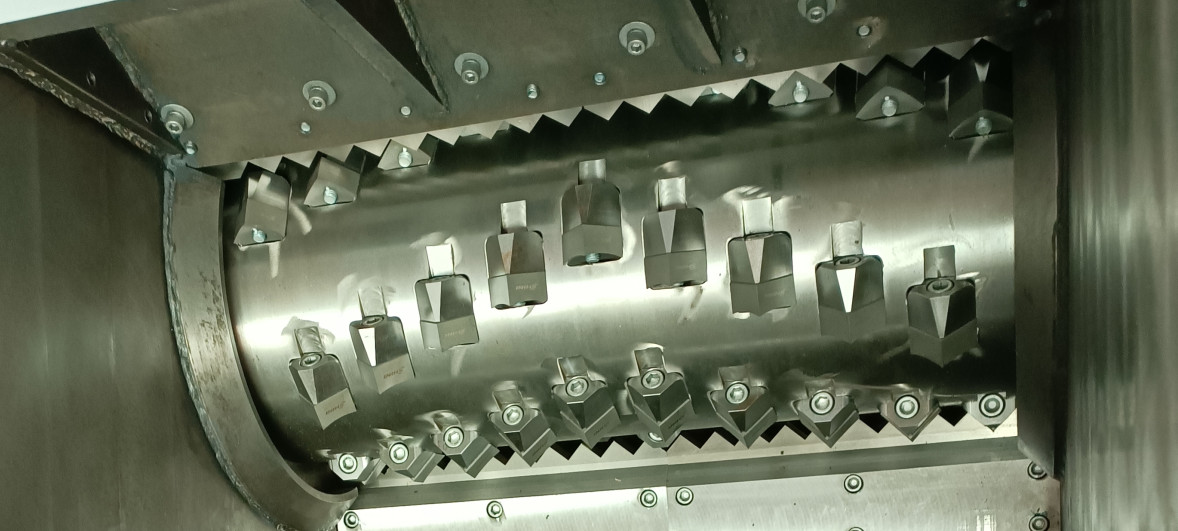
Materials’ shredding process
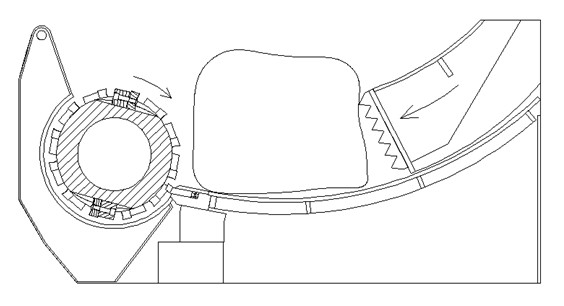
1. The pushing block pushes the materials to the rotating cutter shaft
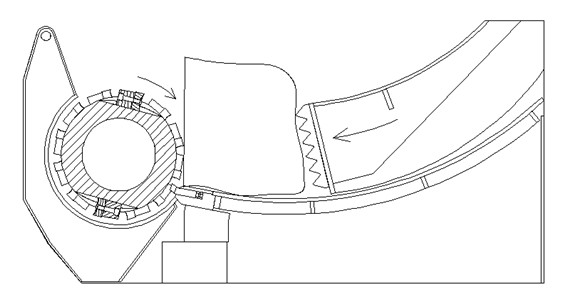
2. The rotating cutter block shreds the materials
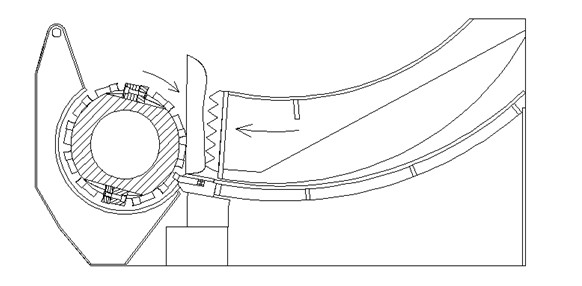
3. The pushing block continues to push the materials to the rotating cutter shaft, and the large materials are shredded into small pieces.
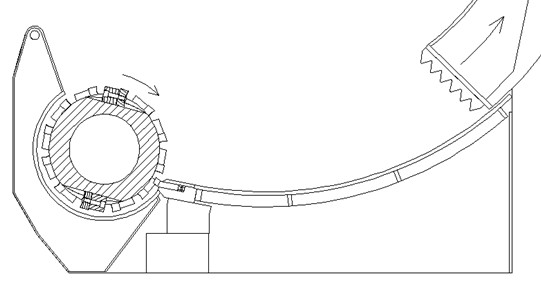
4. The pushing block returns and repeats the process until all the material is shredded into smaller pieces to pass through the screen.
Application: It applies to crushing especially large, thick, and solid materials, which has a wide application range, including large head wastes from the injection molding, blow molding, or extrusion molding.
A plastics granulator refers to a machine used for granulating plastic materials, and it can cut large plastic parts into suitable granules. Its working principle is the rotating blades in the cutting chamber rotating relatively against the fixed blade to crush the materials.
The Selection of Large Granulator
The feed port diameter, cutting chamber diameter, and cutting motor power of the large granulator are relatively huge, which can granulate large plastic materials. When the small or middle granulator is too hard to crush large plastic wastes, we can provide the large granulator to meet customer demand. The large granulator also has two different cutting chamber structures, and the application is as below:
3 Rotating Blades and 2 Fixed Blades (Standard Type)
The low cut point design and low initial cutting point of the fixed blade in the cutting chamber make big inlet space in the chamber, and the material can be easily grabbed and cut after entering the cutting chamber. The cutting chamber design is ideal for granulating large hollow objects and framework materials that can be crushed to desired particles directly after granulating, and the cutting chamber’s structure is as follows:
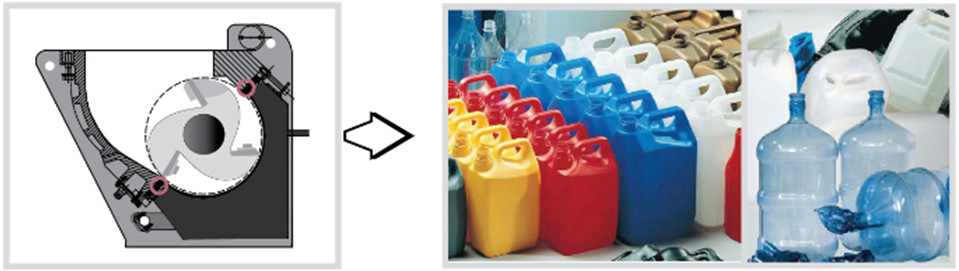
5 Rotating Blades and 3 Fixed Blades
This semi-closed rotor has smaller spaces between the blade rows, thus preventing material from falling into the rotor. The high cut point design and high initial cutting point of the fixed blade in the cutting chamber make small inlet space in the chamber; consequently, there is less aggressive action meaning no blockage or rotor stall even under the most extreme conditions. The cutting chamber design is ideal for granulating small head wastes, thick wall objects, and plates after the injection molding production, and the cutting chamber’s structure is as follows:
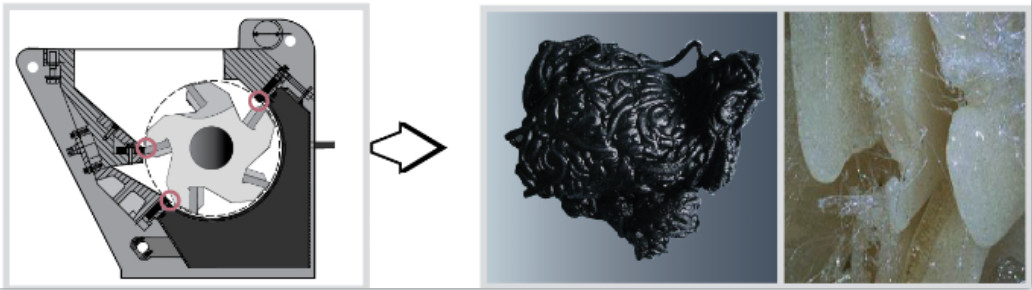
Application: The Central Granulator is a good choice for customers who have to crush many waste materials from injection molding, extrusion molding, or blow molding. The main parameters for the selection include the material size, required cutting ability (i.e., the amount to be crushed per hour), and whether it is fiber contained materials.
Special Reports
- Advantages of the Air-cooled Drying & Dehumidifying Equipment
- Why does the granulator use the dust-separating system?
- SGB Applied in the Dosing and Mixing of Long Glass-fiber Materials
- Pretreatment of PLA, an Eco-friendly Plastic Material
- The Application of Shut-off Suction Box
- How to choose the right micro-feeder
- ShiniEurope
- The Origin of the SCC Cooling Consumption Monitor
If you want to read other articles, back to2022 Quarter 1 Issue 46.