Special Reports
2022 Quarter 1 Issue 46
The Origin of the SCC Cooling Consumption Monitor
The essential auxiliary equipment for different molding processes is so different in the plastics molding process. Among them, the central cooling water system is foremost with the features of high integration, convenient management, space-saving, controllable load, etc. It has competitive advantages that are different from other single-unit cooling equipment, which the market has highly acclaimed. The pipeline of central cooling water system usually adopts the main pipeline with branch pipelines: The main pipe is used to provide cold water from the machine room to the injection molding workshop, and the branch pipe mainly supplies the cold water from the main pipeline to the injection molding machine. Continuous cold water circulating takes away the heat generated from the molding unit (including mould, hot runner, mould temp. controller, etc.) to ensure the quality of the molding products, shorten the molding cycle, and improve productivity. In cold water circulation, it’s inevitably to consume a lot of cooling capacity as a large amount of heat has to be taken away. In addition, as it is known to all, energy can’t be generated without reason. All the energy is produced at a cost, so is the cooling capacity. It takes up a part of the production cost; thus, cooling consumption detection has also become a necessary item in plastic molding.
The SCC Cooling Consumption Monitor has just met the market demand for the detection, mainly used in the central cooling water system and mounted inside each branch pipe. The real-time acquisition of the flow and temperature can accurately record the water flow, inlet, and outlet water temperature and calculate the instantaneous and total cooling consumption. After the acquisition, all the data, such as flow, temperature, cooling capacity, and other parameters, can be displayed and checked in real-time. Also, they can be output to other platforms via the standard interface RS485 to realize data interconnection and sharing, convenient centralized monitoring, and data recording and analyzing.
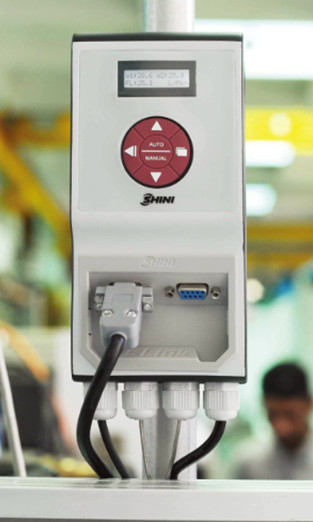
Currently, according to different diameters and flows of the branch water pipes, SCC provides four different sizes to the customer, fully meeting the demands of various occasions. It is easy to install, operate, and use. It can provide a more comprehensive data analysis, judgment, and adjustment basis for molding production..
The actual energy management system mainly detects the electricity consumption assists in detecting the water, gas, and cooling consumption. It can precisely monitor real-time electricity, total cooling capacity, total flow, instantaneous flow, inlet return water temperature, temperature difference, total working time, detector’s working status, and other parameters. That boosts the enterprise to establish a set of advanced, reliable, and safe platforms for energy system operation, manipulation, and management, thus improving the operation and management efficiency of the energy system.
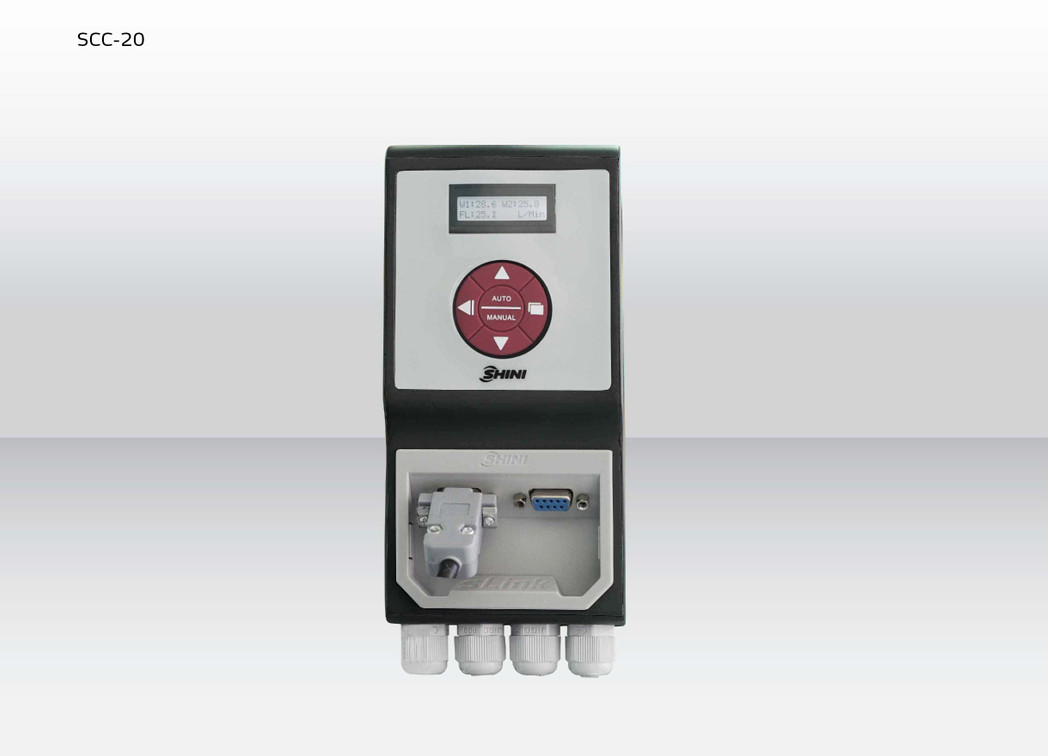
The SCC Cooling Consumption Monitor has just met the market demand for the detection, mainly used in the central cooling water system and mounted inside each branch pipe. The real-time acquisition of the flow and temperature can accurately record the water flow, inlet, and outlet water temperature and calculate the instantaneous and total cooling consumption. After the acquisition, all the data, such as flow, temperature, cooling capacity, and other parameters, can be displayed and checked in real-time. Also, they can be output to other platforms via the standard interface RS485 to realize data interconnection and sharing, convenient centralized monitoring, and data recording and analyzing.
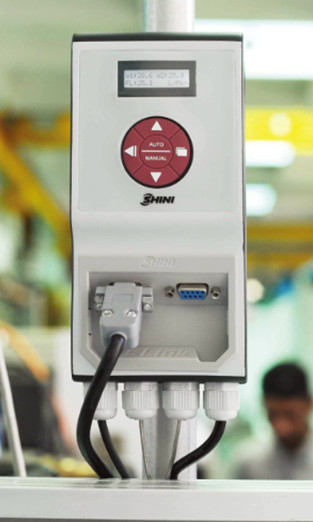
Field Application of the Cooling
Consumption Monitor
Currently, according to different diameters and flows of the branch water pipes, SCC provides four different sizes to the customer, fully meeting the demands of various occasions. It is easy to install, operate, and use. It can provide a more comprehensive data analysis, judgment, and adjustment basis for molding production..
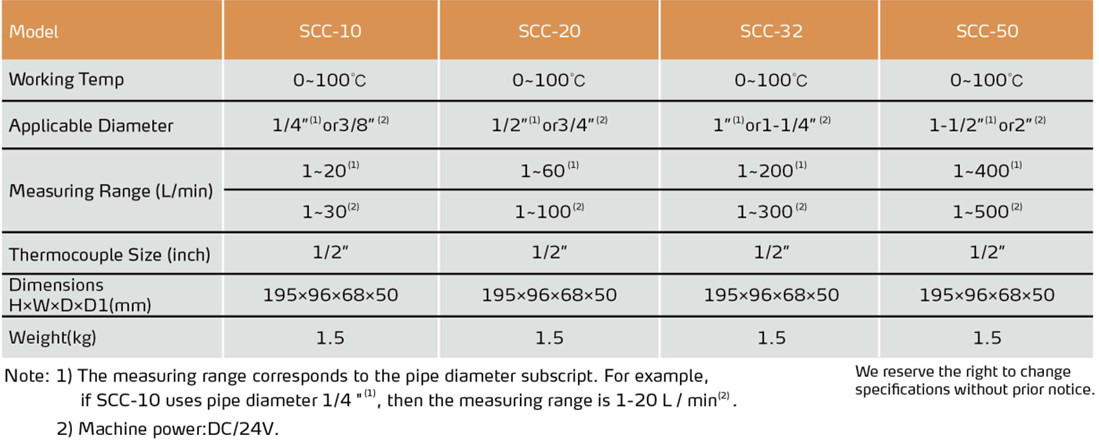
The actual energy management system mainly detects the electricity consumption assists in detecting the water, gas, and cooling consumption. It can precisely monitor real-time electricity, total cooling capacity, total flow, instantaneous flow, inlet return water temperature, temperature difference, total working time, detector’s working status, and other parameters. That boosts the enterprise to establish a set of advanced, reliable, and safe platforms for energy system operation, manipulation, and management, thus improving the operation and management efficiency of the energy system.
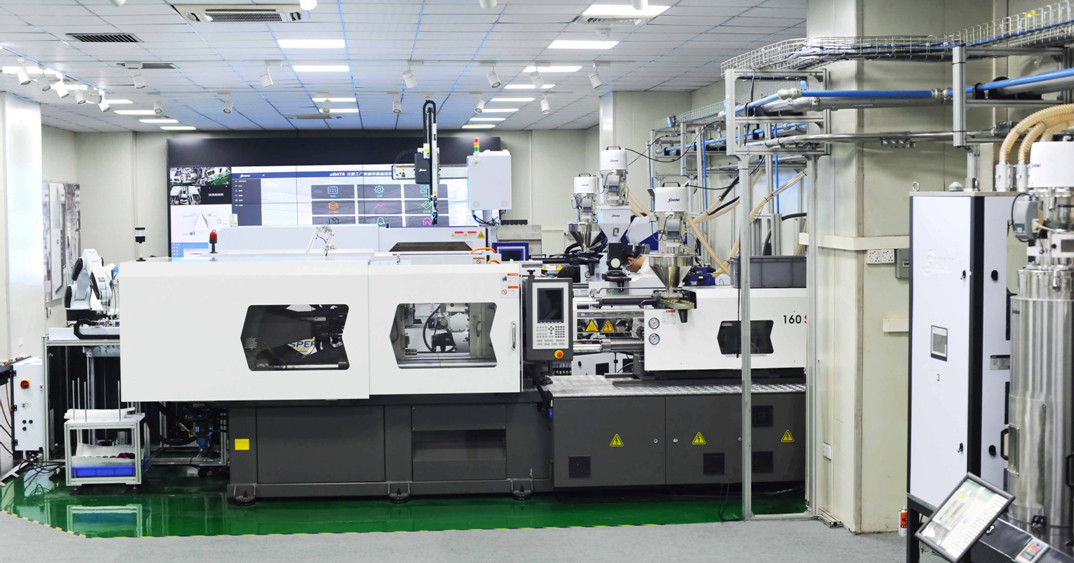
sFactory 4.0 Smart Injection Molding Plant
Special Reports
- Advantages of the Air-cooled Drying & Dehumidifying Equipment
- Why does the granulator use the dust-separating system?
- SGB Applied in the Dosing and Mixing of Long Glass-fiber Materials
- Pretreatment of PLA, an Eco-friendly Plastic Material
- The Application of Shut-off Suction Box
- How to choose the right micro-feeder
- Different Applications of Single-shaft Shredder and Large Granulator
- ShiniEurope
If you want to read other articles, back to2022 Quarter 1 Issue 46.