Special Reports
2022 Quarter 2 Issue 47
Heating and Cooling Auxiliary Equipments for the Controls in Wide Temperature Ranges
Shini provides a full range of plastic auxiliary equipment and its heating and cooling series, including the mould temperature controller, water chiller, integrated cooling/heating machine, etc. These are indispensable auxiliary equipment to improve productivity and product quality in the modern technology industry.
The full name of the integrated cooling/heating machine is the cooling/heating temperature controller that is widely used in plastic, extrusion, injection molding, foaming equipment, medicine, chemical industry, automobile, and other fields. It features accurate temperature control and can heat up and cool down the temperature to the equipment's required value. Besides, it can control multiple machine temperatures to improve productivity and product quality, which is highly practicable.
The integrated cooling/heating machine is divided into two sections: 「heating section」and 「cooling section」, which can meet the demand of the circulating medium's rapid heating or cool in a short time. The temperature range of the machine is 7 ℃ ~ 120 ℃. Different products have different temperature requirements in users' production processes. For example, the mould temperature controller needs to heat up at a high temperature, while the water chiller needs to cool down in low-temperature production. Using the cooling/heating temperature controller can solve the problem in one step so that the temperature control range can meet most working conditions. (In the traditional approach, to achieve the same function and effect, it needs to use the water-cooled water chiller to work with multiple mould temperature controllers, which occupies more space.)
The machine can automatically detect and control the current heating or cooling process according to the technological requirements and intelligently identify the current temperature with an overheat protection function. Besides, it can control the equilibrium temperature of the mould and raise the mould temperature to the value required by the process in a concise time to keep the temperature within a small error and maintain a constant value. Moreover, it can also realize rapid switching, speed up production, and reduce energy consumption, thus improving the product's molding efficiency and reducing defective products.
Water-cooled Models:
Air-cooled Models:
The case of customer 1
Customer: A Filter Equipment Co., Ltd in Hangzhou
Customer Product: Filter related accessories for water treatment
Spec. of IMM: 180T-280T Material: PP
Why did the customer choose the cooling/heating temperature controller STC? The mould temperature of the customer has to be controlled at 15 ℃ ~ 35 ℃ (Different products have different temperature controls). Because of the requirement for low-temperature control, common mould temperature controllers without cooling functions, and standard water chillers without heating functions, they need a machine with both the heating and cooling functions. Finally, we recommend the customer use the cooling/heating temperature controller of Shini.
The customer's feedback: It features precise temperature control, which can meet the requirements of low-temperature control, and the product quality becomes better after using the machine.
Customer 02: An Auto Parts Co., Ltd. in Jiaxing
Customer Product: Automobile parts
Spec. of IMM: 1600T Material: PC
Why did the customer choose the cooling/heating temperature controller STC?
The mould temperature of the customer has to be controlled at 25℃~40℃, and sometimes the mould temperature can reach up to 90 ℃(Different products have different temperature controls). Because different customer moulds have different temperatures, common mould temperature controller without cooling function, and standard water chiller without heating function, they need a machine with both the heating and cooling functions. Finally, we recommend the customer use the cooling/heating temperature controller of Shini.
The feedback of the customer: It applies to different moulds' heating occasions of the customer;
This series of products has been fully developed and well applied in the market. Relevant models can choose IMMs from 60~1000 Tons, and customized products can meet greater demands.
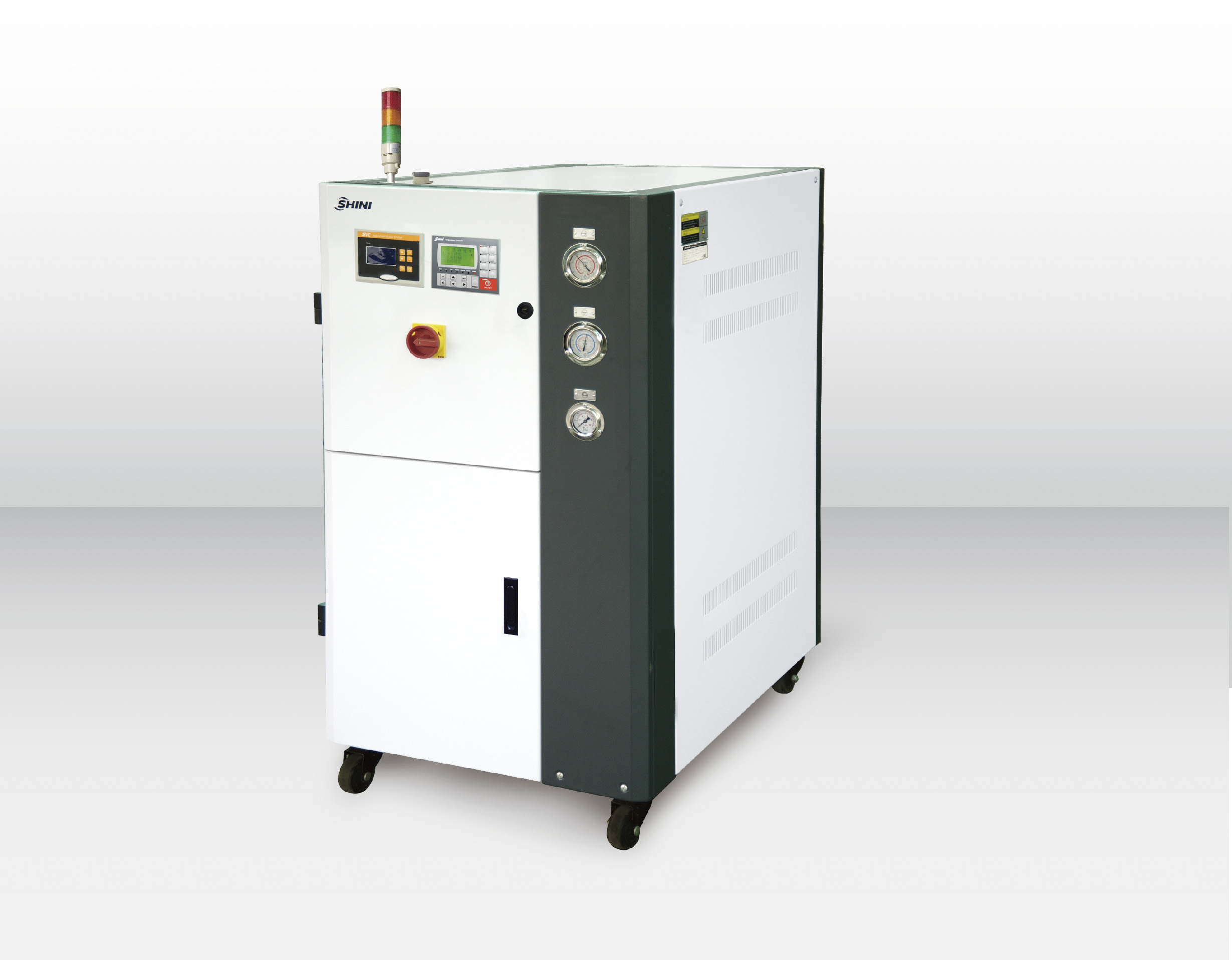
Cooling&Heating Mold Temperature Controller STC-5W
The full name of the integrated cooling/heating machine is the cooling/heating temperature controller that is widely used in plastic, extrusion, injection molding, foaming equipment, medicine, chemical industry, automobile, and other fields. It features accurate temperature control and can heat up and cool down the temperature to the equipment's required value. Besides, it can control multiple machine temperatures to improve productivity and product quality, which is highly practicable.
The integrated cooling/heating machine is divided into two sections: 「heating section」and 「cooling section」, which can meet the demand of the circulating medium's rapid heating or cool in a short time. The temperature range of the machine is 7 ℃ ~ 120 ℃. Different products have different temperature requirements in users' production processes. For example, the mould temperature controller needs to heat up at a high temperature, while the water chiller needs to cool down in low-temperature production. Using the cooling/heating temperature controller can solve the problem in one step so that the temperature control range can meet most working conditions. (In the traditional approach, to achieve the same function and effect, it needs to use the water-cooled water chiller to work with multiple mould temperature controllers, which occupies more space.)
The machine can automatically detect and control the current heating or cooling process according to the technological requirements and intelligently identify the current temperature with an overheat protection function. Besides, it can control the equilibrium temperature of the mould and raise the mould temperature to the value required by the process in a concise time to keep the temperature within a small error and maintain a constant value. Moreover, it can also realize rapid switching, speed up production, and reduce energy consumption, thus improving the product's molding efficiency and reducing defective products.
Water-cooled Models:
- Adopt a tube-in-shell condenser designed for quick heat transfer and excellent heat dissipation.
- The ambient temperature of the equipment is not affected by its operation, so which is no need for a separate air duct.
- The size of the water-cooled model is smaller than that of the air-cooled model.
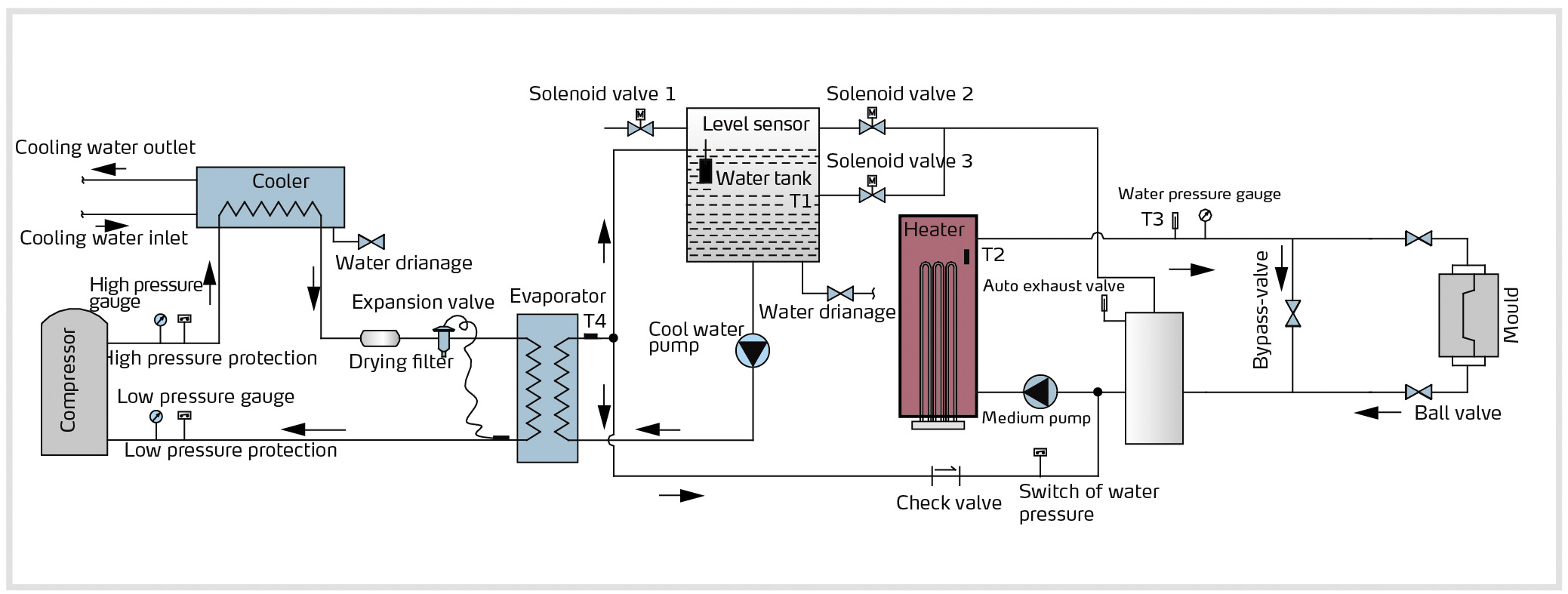
Working Principle
Air-cooled Models:
- Fin style condenser designed for excellent heat transfer and rapid cooling without any cooling water.
- Reduce the demands on cooling water that saves the cost of auxiliary equipment.
- The condenser is easy to clean, which applies to models with low compressor power.
- Wide range of temperature control.
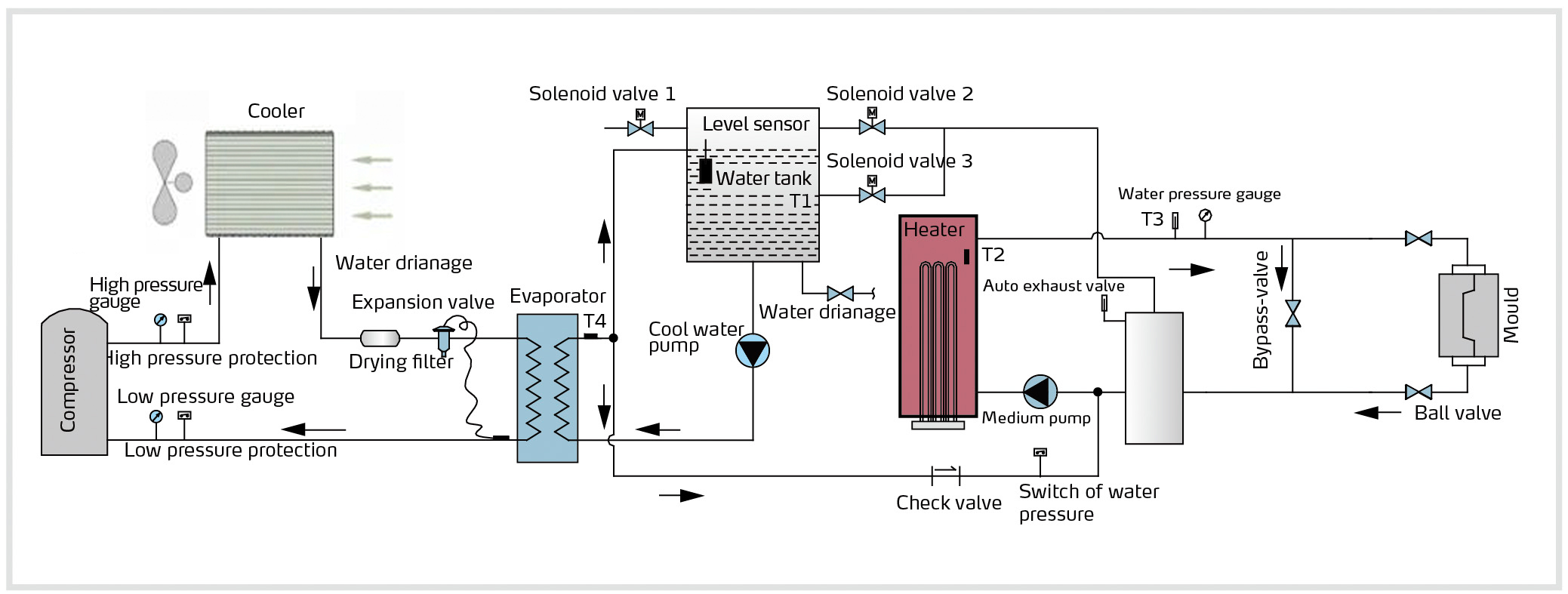
Working Principle
The case of customer 1
Customer: A Filter Equipment Co., Ltd in Hangzhou
Customer Product: Filter related accessories for water treatment
Spec. of IMM: 180T-280T Material: PP
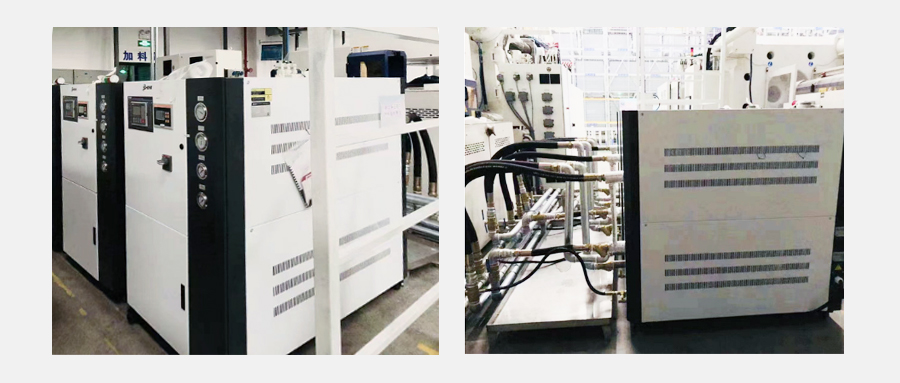
Why did the customer choose the cooling/heating temperature controller STC? The mould temperature of the customer has to be controlled at 15 ℃ ~ 35 ℃ (Different products have different temperature controls). Because of the requirement for low-temperature control, common mould temperature controllers without cooling functions, and standard water chillers without heating functions, they need a machine with both the heating and cooling functions. Finally, we recommend the customer use the cooling/heating temperature controller of Shini.
The customer's feedback: It features precise temperature control, which can meet the requirements of low-temperature control, and the product quality becomes better after using the machine.
Customer 02: An Auto Parts Co., Ltd. in Jiaxing
Customer Product: Automobile parts
Spec. of IMM: 1600T Material: PC
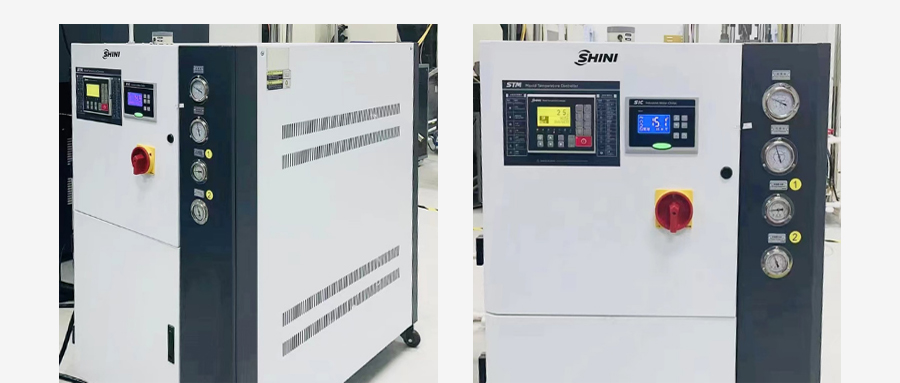
Why did the customer choose the cooling/heating temperature controller STC?
The mould temperature of the customer has to be controlled at 25℃~40℃, and sometimes the mould temperature can reach up to 90 ℃(Different products have different temperature controls). Because different customer moulds have different temperatures, common mould temperature controller without cooling function, and standard water chiller without heating function, they need a machine with both the heating and cooling functions. Finally, we recommend the customer use the cooling/heating temperature controller of Shini.
The feedback of the customer: It applies to different moulds' heating occasions of the customer;
This series of products has been fully developed and well applied in the market. Relevant models can choose IMMs from 60~1000 Tons, and customized products can meet greater demands.
Special Reports
- SPG Pump Group
- Advantages of Central Conveying System
- How to effectively prevent mould from being condensed in the production process?
- SDS Dry Cooler
- Why Are We Using the Material Distribution Station?
- Application of SMM Material Consumption Monitor for Hopper Receiver
- Application of Metal Detector in Plastics Moulding Industry
If you want to read other articles, back to2022 Quarter 2 Issue 47.