Special Reports
2022 Quarter 2 Issue 47
How to effectively prevent mould from being condensed in the production process?
In the plastic moulding process, the parameters require differ in thousands of ways according to the molding processes of different materials. Meanwhile, the mould temperature control is also different due to different production processes. Some moulds need a high working temperature during the production to ensure the precise product shape and size, and some moulds need a high-pressure and large flow of chilled water (usually at 7~10°C) during moulding to reduce the molding cycle and improve the productivity as much as possible. However, when using the chilled water, the temperature of the mould outer surface is also low, and the moisture in the air condenses on the mould surface and cavity, seriously affecting the plastic product’s quality.
Shini SMD-H mould sweat dehumidifier can continuously provide a large flow of dry air with constant temperature and low dew point to ensure the mould temperature and humidity are always kept in a stable dry environment. Besides, the dew point temperature of the mould ambient air is low to ensure that the moisture in the air will not condense on the mould surface, to avoid the mould surface condensing due to the temperature difference during mould opening, and improve the product quality and productivity.
The SMD-H adopts the principle of synchronous pre-dehumidification and fine dehumidification. External mist air indirectly contacts the chilled water in the cooler during the pre-dehumidification. A large amount of moisture in ambient air is condensed due to low temperature and enters the water container. When the water reaches the set liquid level, it triggers the water pump to discharge it automatically. The fine dehumidification takes the honeycomb rotor as its main moisture absorption device, and it can provide continuous and stable dry air with a low dew point. After moisture is absorbed, the honeycomb rotor will regain the suction ability after high-temperature regeneration to achieve continuous dehumidification. After dehumidification, the low dew-point dry air will enter the product molding area through the post cooler.
Currently, the SMD-H series has four models, and there are SMD-500H, SMD-1000H, SMD-2000H, and SMD-3000H, which can provide up to 3000m3/hr air quantity. It can meet the demands of various rapid injection molding processes to ensure the plastic product’s quality.
The return air collector is used to recycle the dry air in a closed-loop for equipment used in high temperature and humidity environments. The whole drying air can be used in a relatively independent condition with fewer outside influences.
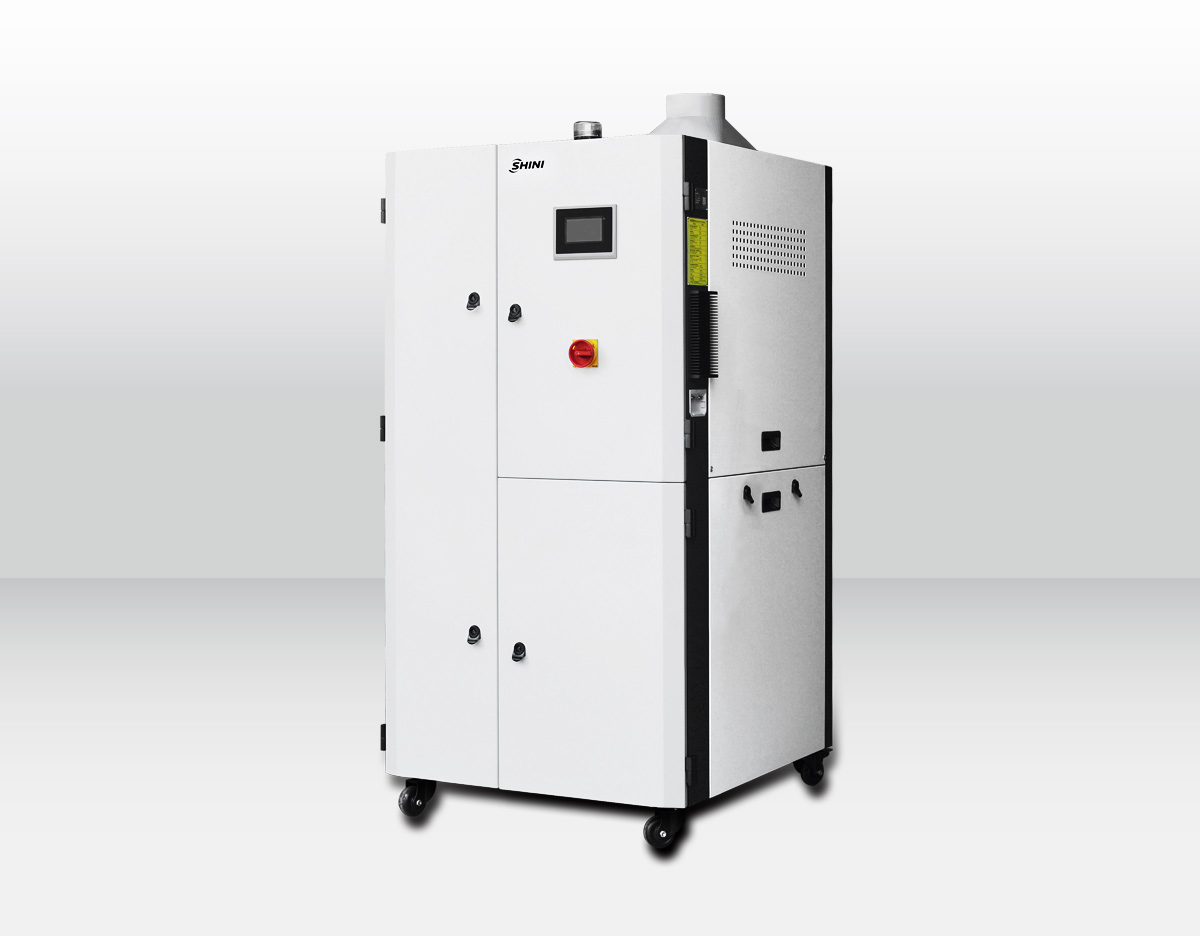
Shini SMD-H mould sweat dehumidifier can continuously provide a large flow of dry air with constant temperature and low dew point to ensure the mould temperature and humidity are always kept in a stable dry environment. Besides, the dew point temperature of the mould ambient air is low to ensure that the moisture in the air will not condense on the mould surface, to avoid the mould surface condensing due to the temperature difference during mould opening, and improve the product quality and productivity.
The SMD-H adopts the principle of synchronous pre-dehumidification and fine dehumidification. External mist air indirectly contacts the chilled water in the cooler during the pre-dehumidification. A large amount of moisture in ambient air is condensed due to low temperature and enters the water container. When the water reaches the set liquid level, it triggers the water pump to discharge it automatically. The fine dehumidification takes the honeycomb rotor as its main moisture absorption device, and it can provide continuous and stable dry air with a low dew point. After moisture is absorbed, the honeycomb rotor will regain the suction ability after high-temperature regeneration to achieve continuous dehumidification. After dehumidification, the low dew-point dry air will enter the product molding area through the post cooler.

The return air collector is used to recycle the dry air in a closed-loop for equipment used in high temperature and humidity environments. The whole drying air can be used in a relatively independent condition with fewer outside influences.
Special Reports
- Heating and Cooling Auxiliary Equipments for the Controls in Wide Temperature Ranges
- SPG Pump Group
- Advantages of Central Conveying System
- SDS Dry Cooler
- Why Are We Using the Material Distribution Station?
- Application of SMM Material Consumption Monitor for Hopper Receiver
- Application of Metal Detector in Plastics Moulding Industry
If you want to read other articles, back to2022 Quarter 2 Issue 47.