Special Reports
2022 Quarter 2 Issue 47
Application of Metal Detector in Plastics Moulding Industry
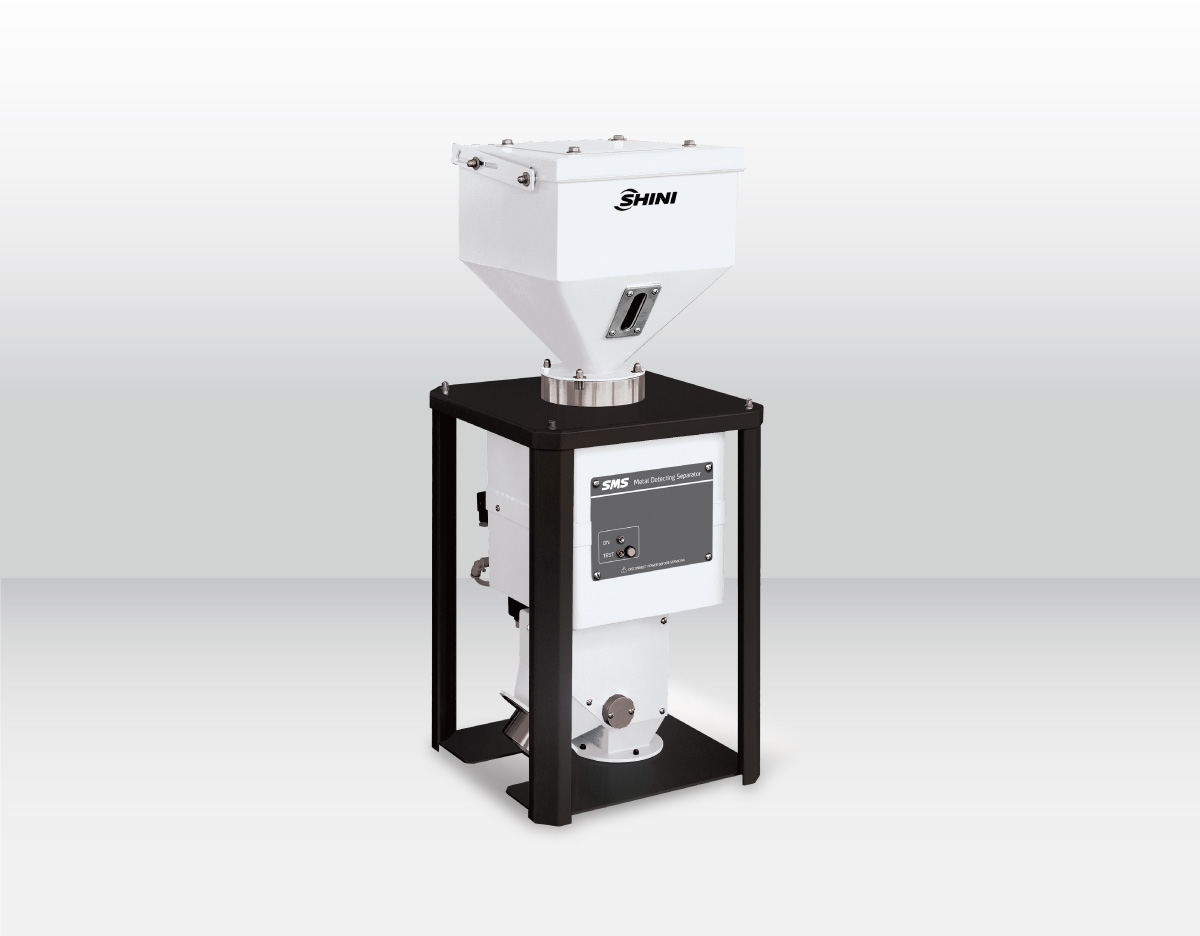
Plastic materials have been widely used in all aspects of people's lives. Plastic materials will be recycled on most occasions to save resources and lower production costs. However, there are many problems in the recycling process, such as unexpected metal impurities (e.g., copper, aluminum, tin, stainless steel, stainless iron) in the recycled plastics or sprues, which may lead to the injection molding machine and extruder screw, nozzle, cylinder fault, as well as flow, pipeline, and outlet blockage, product damage and other problems. Some impurities may also damage the mold. To clean up these impurities, it may need to disassemble the screw, injection nozzle, screen, and other components on the plastic injection molding machine, which not only affects the production but also increase the labor cost to repair the screw, nozzle, or screen and replace easy-broken parts. To solve the above problems and reduce potential risks of metal impurities to the plastics injection molding process, it's difficult to guarantee the product quality by only relying on regular manual inspection, which is inefficient with a high missed inspection rate. Plastic materials can be pretreated before entering the injection molding process, and use a metal separator to separate the metal impurities that may be contained in the plastics.
The SMS series metal separator developed by Shini features high precision, sensitivity, and reliability. It can easily replace the traditional manual separation, and the integrated metal impurities' rapid separation system is suitable for detecting bulk products. It can be detected even if the metal is sealed in the product. Besides, the SMS can quickly detect and separate various metal impurities in plastics, reducing downtime and maintenance accidents, increasing work efficiency, and reducing production costs. Its working principle is that when metal impurities pass through the metal detector, the electronic detector will send a signal to start the valve and discharge the materials containing metal impurities. It adopts a pneumatic discharge system with small volume and accurate discharge and can be directly installed on the hopper of the injection molding machine (extruder) or the stand floor. The detection channel of this model series can be divided into 35mm, 50mm, and 70mm, and the throughput is 600l/hr~3000l/hr, which can meet different customer demands. This product is suitable for detecting and separating metals mixed in food, medicine, plastics, chemical materials, food ingredients, and other industries, including iron and nonferrous metals (such as copper, aluminum, stainless steel), etc.
Advantages of using the metal separator:
1. Protect the production equipment from damage;
2. Improve the productivity
3. Improve the material utilization rate
4. Improve the product quality
5. Reduce the repair costs and losses caused by shutdown maintenance
6. Increase the products' safety and raise the product quality of the enterprise
Special Reports
- Heating and Cooling Auxiliary Equipments for the Controls in Wide Temperature Ranges
- SPG Pump Group
- Advantages of Central Conveying System
- How to effectively prevent mould from being condensed in the production process?
- SDS Dry Cooler
- Why Are We Using the Material Distribution Station?
- Application of SMM Material Consumption Monitor for Hopper Receiver
If you want to read other articles, back to2022 Quarter 2 Issue 47.